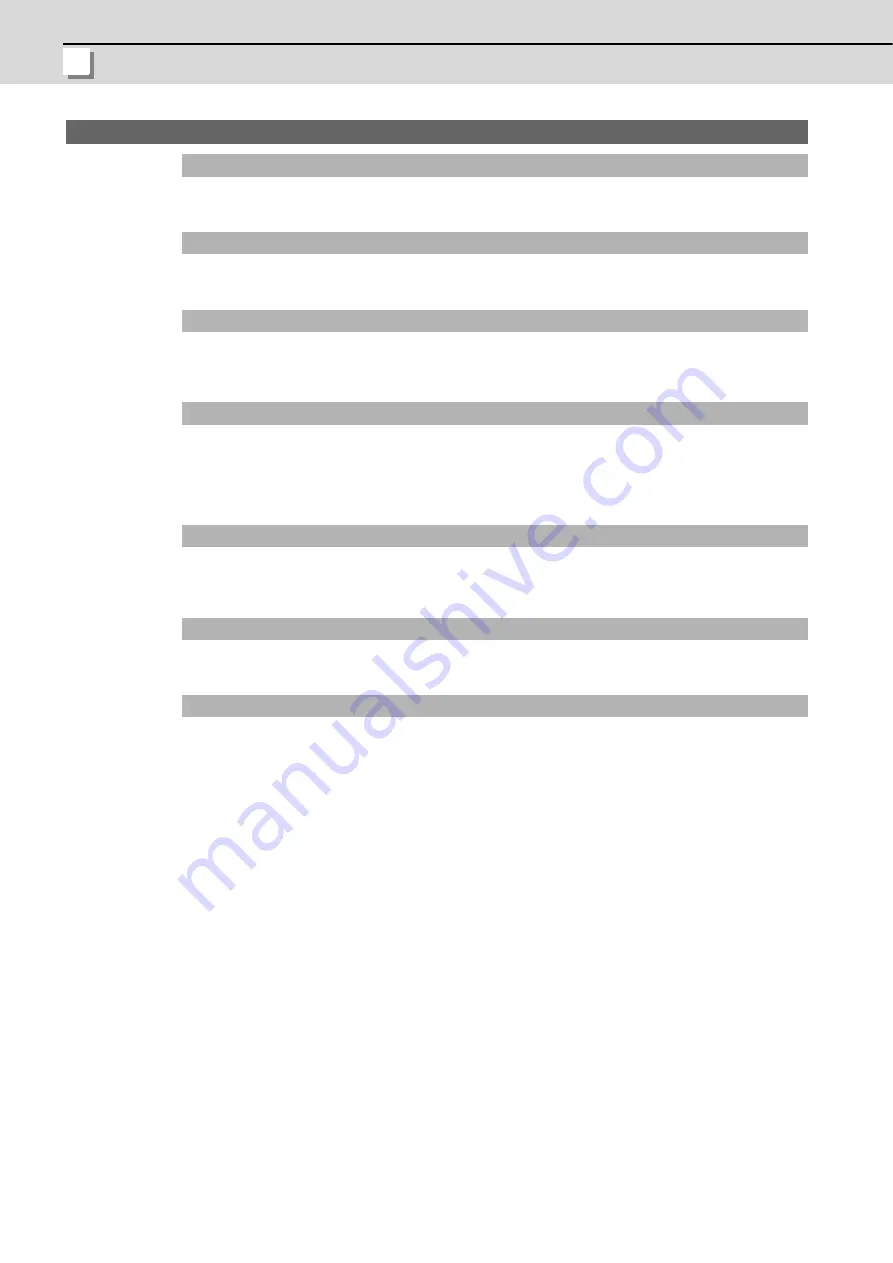
Appendix 1 Explanation of Parameters
MITSUBISHI CNC
204
【
#1226
】
aux10
bit0: Tool compensation data for external workpiece coordinate offset measurement
Select the tool offset data to be used for external workpiece coordinate offset measurement.
0: Tool length data and nose wear data
1: Tool length data
bit1: Optional block skip type
Select whether to enable optional block skipping in the middle of a block.
0: Enable block skipping only at the beginning of a block.
1: Enable block skipping at the beginning of the block and in the middle of a block.
bit2: Single block stop timing
Select the timing at which the single block signal is enabled.
0: Enable the single block stop after the block is finished, when the signal goes ON during
automatic operation startup.
1: Enable the single block stop when the signal is ON at the end of the block.
bit3 : C axis reference position return type
Select the type of reference position return for the C axis.
0 : Return to the zero point by G28 reference position return command and manual reference
position return start-up.
1 : The reference position return will be carried out before executing the first block of the first C axis
command after switching over to the C aix mode in an automatic mode. Return to the zero point
by G28 reference position return command and manual reference position return start-up.
bit4: S command during constant surface speed
Select whether to output a strobe signal when S command is issued in constant surface speed
mode.
0: Output no strobe signal in constant surface speed mode.
1: Output strobe signals even in constant surface speed mode.
bit5: Dog/OT signal arbitrary assignment enabled
Select whether to enable the signal assignment for the origin dog and H/W OT.
0: Disable
1: Enable arbitrary allocation
bit6: Setting and display unit selection
Select the unit to be used as the setting/display unit or handle feed unit from the command unit or
internal unit.
0: Internal unit
1: Command unit
(Note 1) This parameter is enabled only in initial millimeter mode (when "#1041 I_inch" is set to "0").
The internal unit is always used in initial inch mode (when "#1041 I_inch" is set to "1").
(Note 2) This parameter is enabled immediately after it is set.
(Note 3) If addition setting is performed for tool and workpiece offset data with the command unit
"inch" and internal unit "mm", an error may occur.
Related parameter: "#1152 I_G20 (Initial command unit)"
Summary of Contents for C70
Page 1: ......
Page 3: ......
Page 9: ......
Page 11: ......
Page 13: ......
Page 18: ...1 1 Outline ...
Page 21: ...1 Outline MITSUBISHI CNC 4 ...
Page 22: ...5 2 GOT Initial Setup ...
Page 73: ...2 GOT Initial Setup MITSUBISHI CNC 56 ...
Page 74: ...57 3 PLC CPU Initial Setup ...
Page 91: ...3 PLC CPU Initial Setup MITSUBISHI CNC 74 ...
Page 92: ...75 4 CNC CPU Initial Setup ...
Page 105: ...4 CNC CPU Initial Setup MITSUBISHI CNC 88 ...
Page 106: ...89 5 Connecting and Setting up Multiple CNC CPU Modules ...
Page 115: ...5 Connecting and Setting up Multiple CNC CPU Modules MITSUBISHI CNC 98 ...
Page 116: ...99 6 Setting Machine Parameters ...
Page 130: ...113 7 Setting the Position Detection System ...
Page 153: ...7 Setting the Position Detection System MITSUBISHI CNC 136 ...
Page 154: ...137 8 Deceleration Check ...
Page 159: ...8 Deceleration Check MITSUBISHI CNC 142 ...
Page 160: ...143 9 Setting the Tool Entry Prohibited Range ...
Page 169: ...9 Setting the Tool Entry Prohibited Range MITSUBISHI CNC 152 ...
Page 170: ...153 10 Data Backup and Restoration ...
Page 184: ...167 Appendix 1 Explanation of Parameters ...
Page 435: ...Appendix 1 Explanation of Parameters MITSUBISHI CNC 418 ...
Page 436: ...419 Appendix 2 Explanation of Alarms ...
Page 608: ...591 Appendix 3 Display on 7 segment LED ...
Page 624: ......
Page 628: ......