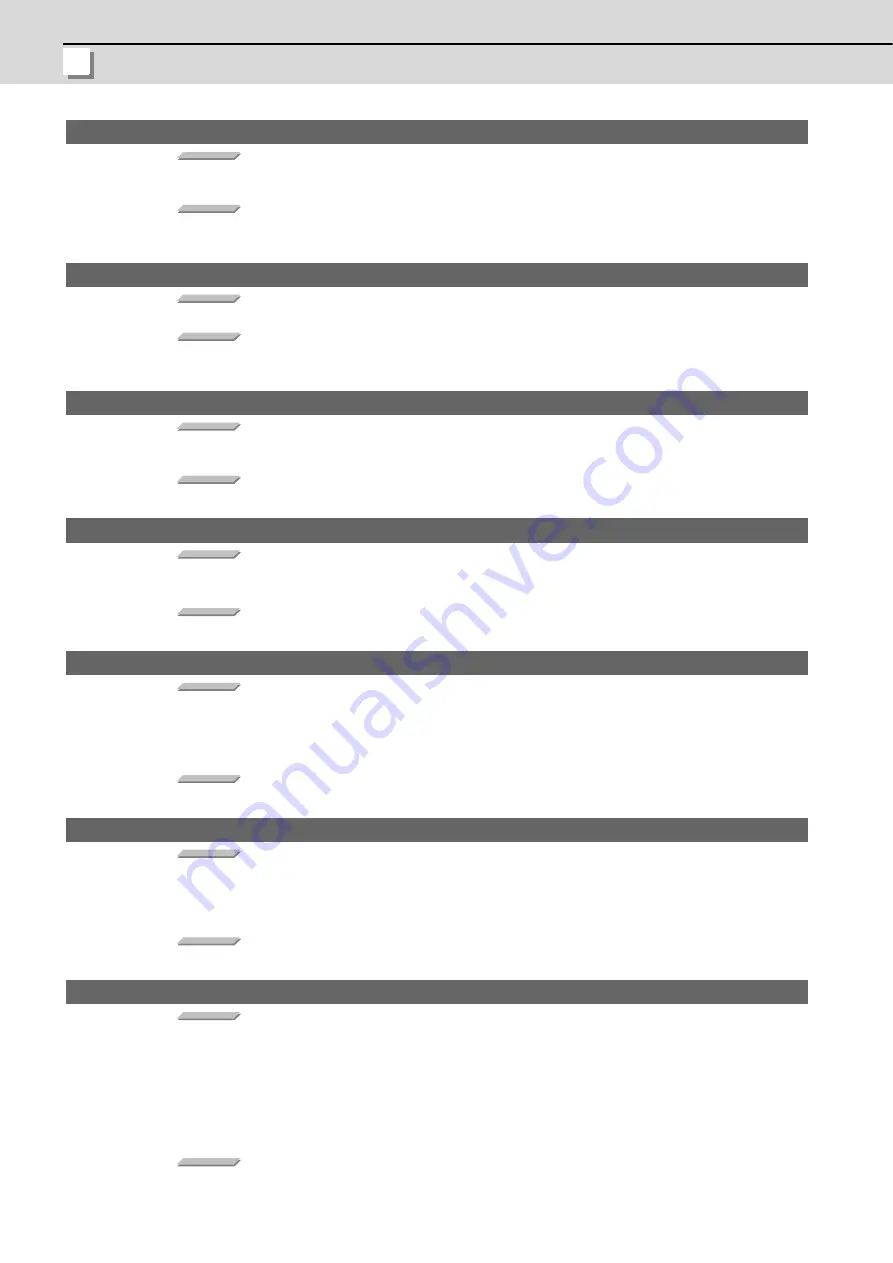
Appendix 2 Explanation of Alarms
MITSUBISHI CNC
538
P460 TAPE I/O ERROR
Details
An error has occurred in the tape reader. Otherwise an error has occurred in the printer during macro
printing.
Remedy
- Check the power and cable of the connected devices.
- Correct the I/O device parameters.
P461 FILE I/O ERROR
Details
- A file of the machining program cannot be read.
Remedy
- In memory mode, the programs stored in memory may have been destroyed. Output all of the
programs and tool data and then format the system.
P480 No spec: Milling
Details
- Polar coordinate interpolation was commanded when the polar coordinate interpolation
specifications were not provided.
Remedy
- Check the specifications.
P481 Illegal G code (mill)
Details
- An illegal G code was used during cylindrical interpolation or polar coordinate interpolation.
- The G07.1 command was issued during the tool radius compensation.
Remedy
- Correct the program.
P482 Illegal axis (mill)
Details
- G07. 1 was commanded when the cylindrical compensation is disabled.
- G12. 1 was commanded when the polar coordinate interpolation is disabled.
- Cylindrical interpolation/polar coordinate interpolation was commanded before tool compensation
cancellation is completed.
Remedy
- Correct the machining program, parameters and PLC interface signals.
P484 R-pnt ret incomplete (mill)
Details
- Movement was commanded to an axis that had not completed reference position return during the
milling mode.
- Movement was commanded to an axis that had not completed reference position return during
cylindrical interpolation or polar coordinate interpolation.
Remedy
- Carry out manual reference position return.
P485 Illegal modal (mill)
Details
- The command unacceptable in the cylindrical interpolation was issued.
- A T command was issued during the cylindrical interpolation or polar coordinate interpolation mode.
- Cylindrical interpolation or polar coordinate interpolation was commanded during the constant
surface speed control mode (G96).
- A plane selection command was issued during the polar coordinate interpolation mode.
- A movement command was issued when the plane was not selected just before or after the G07.1
command.
Remedy
- Correct the program.
Summary of Contents for C70
Page 1: ......
Page 3: ......
Page 9: ......
Page 11: ......
Page 13: ......
Page 18: ...1 1 Outline ...
Page 21: ...1 Outline MITSUBISHI CNC 4 ...
Page 22: ...5 2 GOT Initial Setup ...
Page 73: ...2 GOT Initial Setup MITSUBISHI CNC 56 ...
Page 74: ...57 3 PLC CPU Initial Setup ...
Page 91: ...3 PLC CPU Initial Setup MITSUBISHI CNC 74 ...
Page 92: ...75 4 CNC CPU Initial Setup ...
Page 105: ...4 CNC CPU Initial Setup MITSUBISHI CNC 88 ...
Page 106: ...89 5 Connecting and Setting up Multiple CNC CPU Modules ...
Page 115: ...5 Connecting and Setting up Multiple CNC CPU Modules MITSUBISHI CNC 98 ...
Page 116: ...99 6 Setting Machine Parameters ...
Page 130: ...113 7 Setting the Position Detection System ...
Page 153: ...7 Setting the Position Detection System MITSUBISHI CNC 136 ...
Page 154: ...137 8 Deceleration Check ...
Page 159: ...8 Deceleration Check MITSUBISHI CNC 142 ...
Page 160: ...143 9 Setting the Tool Entry Prohibited Range ...
Page 169: ...9 Setting the Tool Entry Prohibited Range MITSUBISHI CNC 152 ...
Page 170: ...153 10 Data Backup and Restoration ...
Page 184: ...167 Appendix 1 Explanation of Parameters ...
Page 435: ...Appendix 1 Explanation of Parameters MITSUBISHI CNC 418 ...
Page 436: ...419 Appendix 2 Explanation of Alarms ...
Page 608: ...591 Appendix 3 Display on 7 segment LED ...
Page 624: ......
Page 628: ......