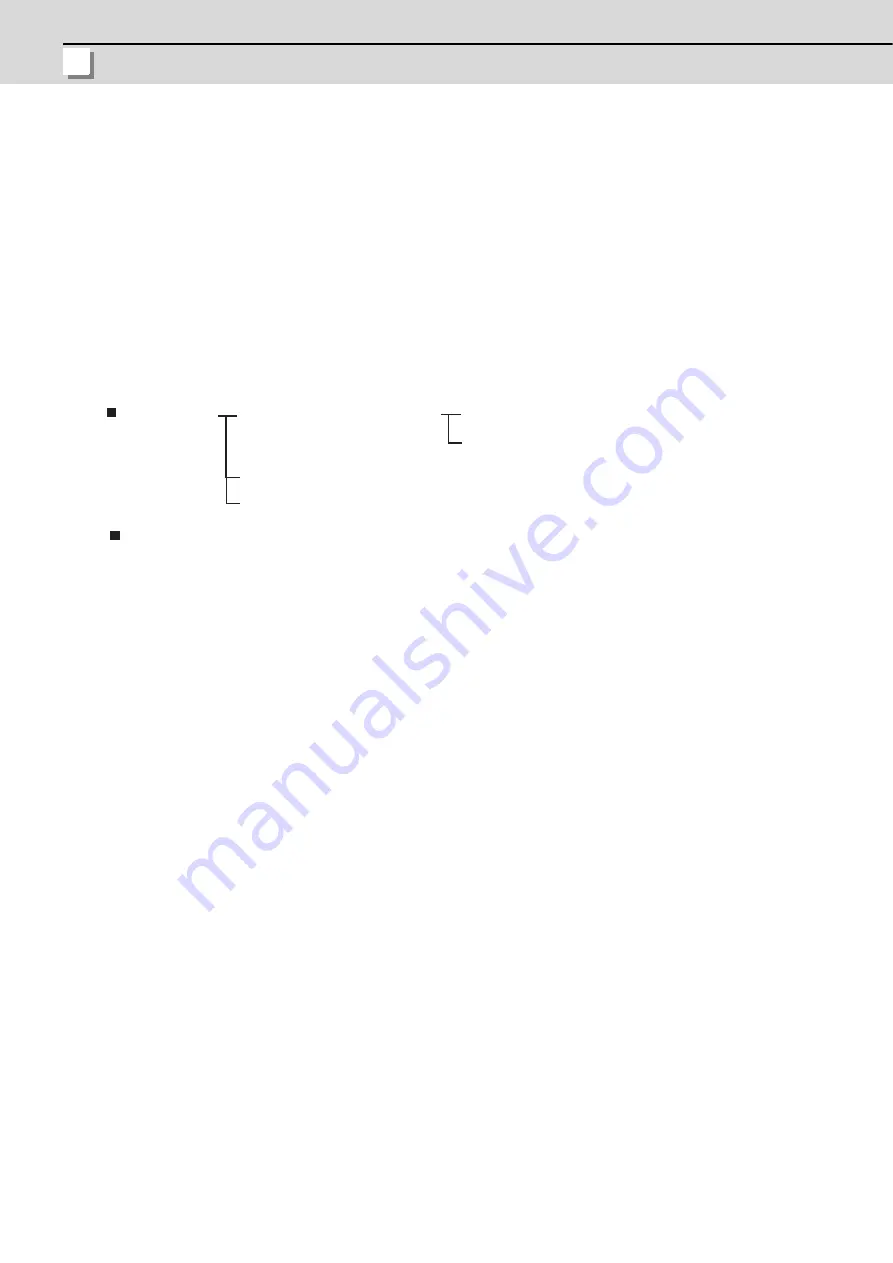
7 Setting the Position Detection System
MITSUBISHI CNC
114
There are two kinds of position detection system: one is "relative position detection", which determines the reference
position (zero point) at every CNC power-ON; the other is "absolute position detection", which allows to start the
operation without redetermining the reference position (zero point) after the CNC power-ON.
Reference position determination method for "Relative position detection" is "dog-type method (dog-type reference
position return)" only, and for "Absolute position detection", "dogless-type" as well as "dog-type" is available. "Dogless-
type" has three methods: "machine end stopper method", "marked point alignment method" and "marked point alignment
method II".
Set the parameter "#2049 type (Absolute position detection method)" for the type and method of absolute position zero
point initialization set.
(Note)
Determining and storing the reference position (absolute position zero point) is also required to carry out
"absolute position detection".
7.1 Setting the Original Dog
When carrying out the dog-type reference point return, the origin dog signal device No. will be assigned by setting the
following parameters.
Parameter "#2073" will be valid only when "#1226 aux10/bit" is set to "1".
#1226 aux10/bit5: Set "1" (.assigning the signal is valid).
#2073 zrn_dog: Set the input device for assinging the origin dog signal. (Setting range 0000 to 02FF(Hexadecimal))
(Note 1) When "Near-point dog ignored" (R2421) signal is set to ON, the origin dog signal associated with a specific
control axis can be ignored.
(Note 2) When parameter "#1226 aux10/bit5" is set to "1", do not set the same device No. to "#2073" to "#2075".
Setting the same device No. may cause the emergency stop. However, the device number will not be checked
if the ignore signal (R2420, R2421) is set to the axis.
Automatic initialization
Dog-less type
Machine end stopper method
Manual initialization
Marked point alignment method
Parameter "#2049 type"
Dog type
1
1
2
4
3
Marked point alignment method II
Summary of Contents for C70
Page 1: ......
Page 3: ......
Page 9: ......
Page 11: ......
Page 13: ......
Page 18: ...1 1 Outline ...
Page 21: ...1 Outline MITSUBISHI CNC 4 ...
Page 22: ...5 2 GOT Initial Setup ...
Page 73: ...2 GOT Initial Setup MITSUBISHI CNC 56 ...
Page 74: ...57 3 PLC CPU Initial Setup ...
Page 91: ...3 PLC CPU Initial Setup MITSUBISHI CNC 74 ...
Page 92: ...75 4 CNC CPU Initial Setup ...
Page 105: ...4 CNC CPU Initial Setup MITSUBISHI CNC 88 ...
Page 106: ...89 5 Connecting and Setting up Multiple CNC CPU Modules ...
Page 115: ...5 Connecting and Setting up Multiple CNC CPU Modules MITSUBISHI CNC 98 ...
Page 116: ...99 6 Setting Machine Parameters ...
Page 130: ...113 7 Setting the Position Detection System ...
Page 153: ...7 Setting the Position Detection System MITSUBISHI CNC 136 ...
Page 154: ...137 8 Deceleration Check ...
Page 159: ...8 Deceleration Check MITSUBISHI CNC 142 ...
Page 160: ...143 9 Setting the Tool Entry Prohibited Range ...
Page 169: ...9 Setting the Tool Entry Prohibited Range MITSUBISHI CNC 152 ...
Page 170: ...153 10 Data Backup and Restoration ...
Page 184: ...167 Appendix 1 Explanation of Parameters ...
Page 435: ...Appendix 1 Explanation of Parameters MITSUBISHI CNC 418 ...
Page 436: ...419 Appendix 2 Explanation of Alarms ...
Page 608: ...591 Appendix 3 Display on 7 segment LED ...
Page 624: ......
Page 628: ......