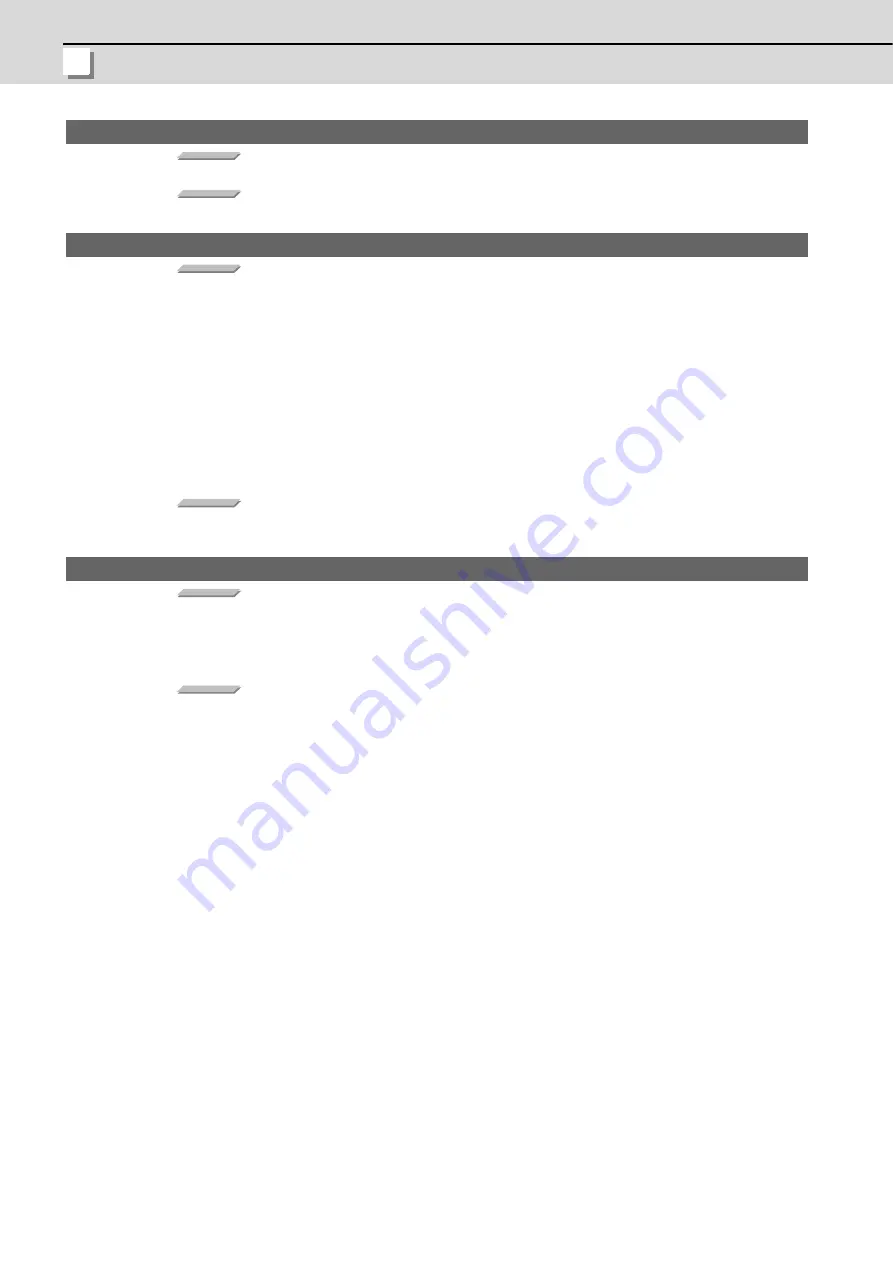
Appendix 2 Explanation of Alarms
MITSUBISHI CNC
458
Y05 Initial parameter error 12800 0
Details
There is a problem in the value set for the parameter.
Remedy
Correct the value set for parameter "#12800 chgauxno (Auxiliary axis number)".
Y05 Initial parameter error 22014 (sub-number)
Details
There is a problem, whose details are indicated by the sub-number, in the value set for the parameter.
[sub-numbers]
0001: A value other than "0" is set for the parameter #22014 when multi-secondary-axis synchronous
control option is not available.
0002: More than 3 groups of axes are designated for synchronous control and multi-secondary-axis
synchronous control combined.
0003: The axis designated as a secondary axis for multi-secondary-axis synchronous control is also
designated as an axis for synchronous control.
0004: The axis designated as the primary axis for multi-secondary-axis synchronous control is also
being designated as an axis for synchronous control.
0005: An axis that is used in more than one part systems is being designated as the primary axis.
0006: An axis that is designated as a secondary axis is also being designated as the primary axis.
Remedy
Correct the values set for "#1068 slavno (Secondary axis number)" and/or "#22014 Mastno (Multi-
secondary-axis sync primary axis number)".
Y06 mcp_no setting error
Details
- MCP Nos. of the servo/spindle drive units are not continuous.
- There is a duplicate setting.
- Axis No. is out of the setting range.
- Channel No. is out of the setting range.
Remedy
Check the values set for the following parameters.
- "#1021 mcp_no (Drive unit I/F channel No. (servo))"
- "#3031 smcp_no (Drive unit I/F channel No. (spindle))"
(Note 1) "#1021 mcp_no (Drive unit I/F channel No. (servo))" and "#3031 smcp_no (Drive unit I/F
channel No. (spindle))" must be continuous.
(Note 2) This alarm is displayed taking precedence over the alarms "Y02 System alarm", "Y07 Too
many axes connected" and "Y09 Too many axisno connected".
(Note 3) Also for the spindle whose parameter "#3024 sout Spindle connection" is set to "0", set the
MCP No. to "#3031 smcp_no Drive unit I/F channel No. (spindle)". (C70 S/W Ver.D3 or later)
Summary of Contents for C70
Page 1: ......
Page 3: ......
Page 9: ......
Page 11: ......
Page 13: ......
Page 18: ...1 1 Outline ...
Page 21: ...1 Outline MITSUBISHI CNC 4 ...
Page 22: ...5 2 GOT Initial Setup ...
Page 73: ...2 GOT Initial Setup MITSUBISHI CNC 56 ...
Page 74: ...57 3 PLC CPU Initial Setup ...
Page 91: ...3 PLC CPU Initial Setup MITSUBISHI CNC 74 ...
Page 92: ...75 4 CNC CPU Initial Setup ...
Page 105: ...4 CNC CPU Initial Setup MITSUBISHI CNC 88 ...
Page 106: ...89 5 Connecting and Setting up Multiple CNC CPU Modules ...
Page 115: ...5 Connecting and Setting up Multiple CNC CPU Modules MITSUBISHI CNC 98 ...
Page 116: ...99 6 Setting Machine Parameters ...
Page 130: ...113 7 Setting the Position Detection System ...
Page 153: ...7 Setting the Position Detection System MITSUBISHI CNC 136 ...
Page 154: ...137 8 Deceleration Check ...
Page 159: ...8 Deceleration Check MITSUBISHI CNC 142 ...
Page 160: ...143 9 Setting the Tool Entry Prohibited Range ...
Page 169: ...9 Setting the Tool Entry Prohibited Range MITSUBISHI CNC 152 ...
Page 170: ...153 10 Data Backup and Restoration ...
Page 184: ...167 Appendix 1 Explanation of Parameters ...
Page 435: ...Appendix 1 Explanation of Parameters MITSUBISHI CNC 418 ...
Page 436: ...419 Appendix 2 Explanation of Alarms ...
Page 608: ...591 Appendix 3 Display on 7 segment LED ...
Page 624: ......
Page 628: ......