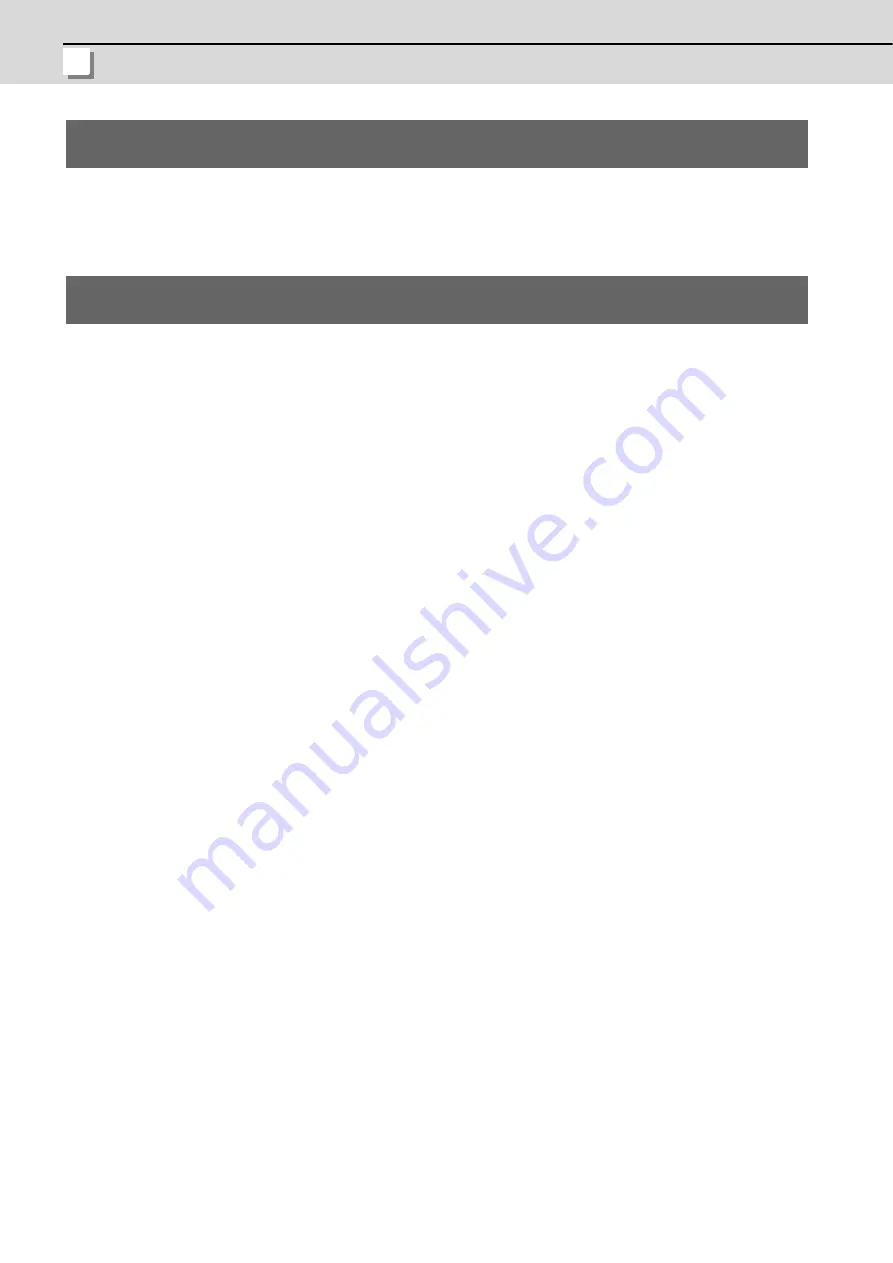
Appendix 1 Explanation of Parameters
MITSUBISHI CNC
360
【
#29067(PR)
】
Communication Status & Error Module side Transfer Cont
Each node communication status & error status read word count
Set a read word count of the data where the I/O communication status and I/O communication error
status of the slave node are saved.
The standard setting is "8".
---Setting range---
1 to 8
【
#29068(PR)
】
Communication Status & Error PLC side Device
Each node communication status & error status read device
Set a device to store the following data:
The slave node I/O communication status is saved into 1st to 4th word.
All bits will be turned OFF when the "I/O communication in progress" (X01) has been turned OFF.
Bit settings: 0: Communication canceled / 1: Communication in progress
<1st word>
bit0: 0th slave node
bit1: 1st slave node
:
bitF: 15th slave node
<2nd word>
bit0: 16th slave node
bit1: 17th slave node
:
bitF: 31st slave node
<3rd word>
bit0: 32nd slave node
bit1: 33rd slave node
:
bitF: 47th slave node
<4th word>
bit0: 48th slave node
bit1: 49th slave node
:
bitF: 63rd slave node
The slave node I/O communication error status is saved into 5th to 8th word.
All bits will be turned OFF when the "I/O communication in progress" (X01) has been turned OFF.
However, when the bit corresponding to the node is ON in the down node detection disabling setting,
the error of the node will not be detected.
Bit settings: 0: No communication error / 1: Communication error detected
<5th word>
bit0: 0th slave node
bit1: 1st slave node
:
bitF: 15th slave node
<6th word>
bit0: 16th slave node
bit1: 17th slave node
:
bitF: 31st slave node
<7th word>
bit0: 32nd slave node
bit1: 33rd slave node
:
bitF: 47th slave node
<8th word>
bit0: 48th slave node
bit1: 49th slave node
:
bitF: 63rd slave node
---Setting range---
Within the number of device points set in the PC parameter's device setting.
Summary of Contents for C70
Page 1: ......
Page 3: ......
Page 9: ......
Page 11: ......
Page 13: ......
Page 18: ...1 1 Outline ...
Page 21: ...1 Outline MITSUBISHI CNC 4 ...
Page 22: ...5 2 GOT Initial Setup ...
Page 73: ...2 GOT Initial Setup MITSUBISHI CNC 56 ...
Page 74: ...57 3 PLC CPU Initial Setup ...
Page 91: ...3 PLC CPU Initial Setup MITSUBISHI CNC 74 ...
Page 92: ...75 4 CNC CPU Initial Setup ...
Page 105: ...4 CNC CPU Initial Setup MITSUBISHI CNC 88 ...
Page 106: ...89 5 Connecting and Setting up Multiple CNC CPU Modules ...
Page 115: ...5 Connecting and Setting up Multiple CNC CPU Modules MITSUBISHI CNC 98 ...
Page 116: ...99 6 Setting Machine Parameters ...
Page 130: ...113 7 Setting the Position Detection System ...
Page 153: ...7 Setting the Position Detection System MITSUBISHI CNC 136 ...
Page 154: ...137 8 Deceleration Check ...
Page 159: ...8 Deceleration Check MITSUBISHI CNC 142 ...
Page 160: ...143 9 Setting the Tool Entry Prohibited Range ...
Page 169: ...9 Setting the Tool Entry Prohibited Range MITSUBISHI CNC 152 ...
Page 170: ...153 10 Data Backup and Restoration ...
Page 184: ...167 Appendix 1 Explanation of Parameters ...
Page 435: ...Appendix 1 Explanation of Parameters MITSUBISHI CNC 418 ...
Page 436: ...419 Appendix 2 Explanation of Alarms ...
Page 608: ...591 Appendix 3 Display on 7 segment LED ...
Page 624: ......
Page 628: ......