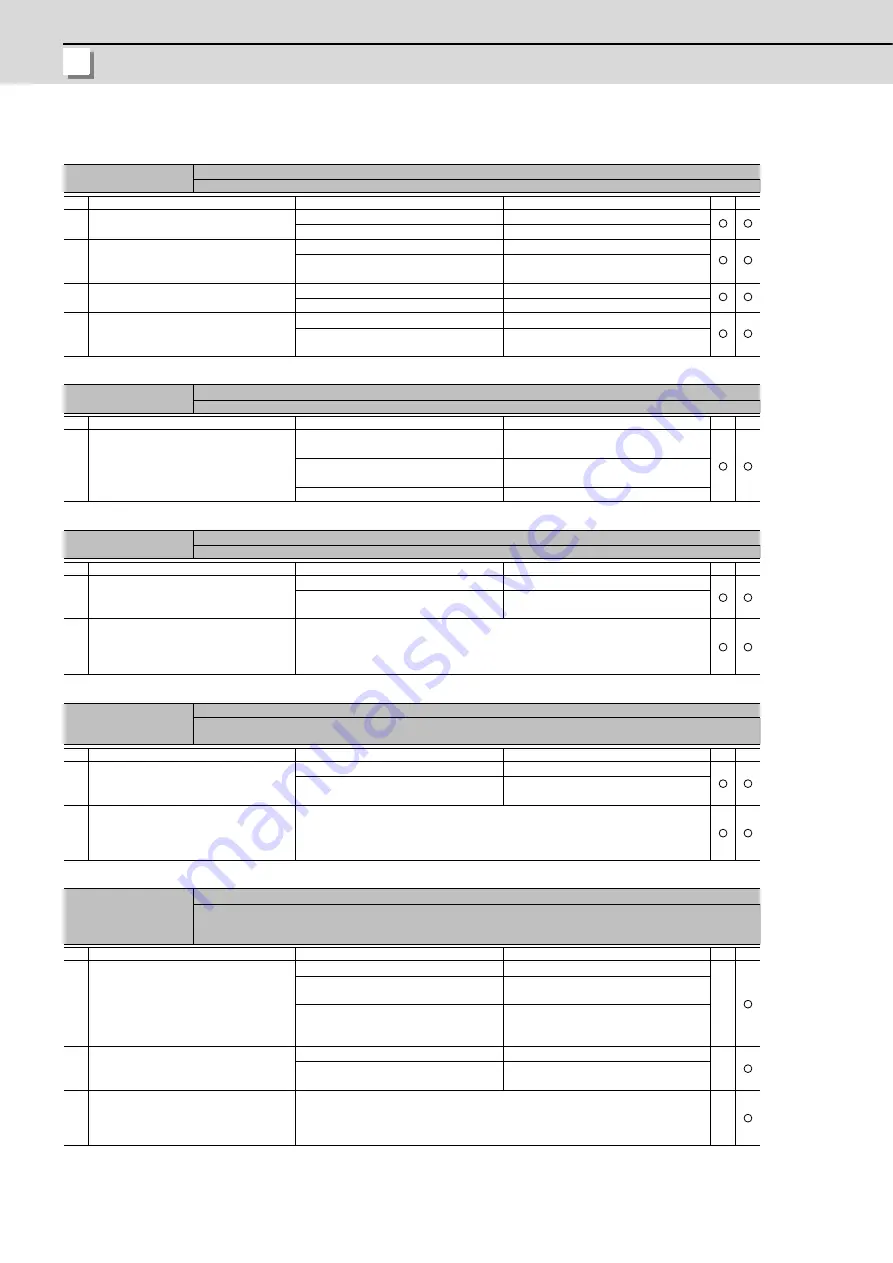
Appendix 2 Explanation of Alarms
MITSUBISHI CNC
558
Appendix 2.16.3.2 Troubleshooting for each alarm No.
Alarm No.
10
Insufficient voltage
Insufficient bus voltage was detected in main circuit.
Investigation details
Investigation results
Remedies
SV
SP
1
Check the timing when the alarm occurs.
The moment of READY ON
Check the investigation item No. 2.
During operation
Increase the power supply capacity (KVA).
2
Did the external contactor turn ON at the
READY ON?
The external contactor did not turn ON.
Check the investigation item No. 3.
The external contactor turned ON,
but the alarm occurred immediately.
Check the investigation item No. 4.
3
Check the wiring of contactor excitation
circuit.
The wiring is correct.
Replace the contactor.
The wiring is not correct.
Rewire.
4
Check the input voltage of the drive unit by
a tester. (Voltage between L1 and L2, L2
and L3, L1 and L3)
The input voltage is normal.
Replace the drive unit.
The input voltage is abnormal.
The measured voltage fluctuates.
Increase the power supply capacity (KVA).
Replace the power supply.
Alarm No.
11
Axis selection error
The axis selection rotary switch is incorrectly set.
Investigation details
Investigation results
Remedies
SV
SP
1
Check the setting of the axis selection
switch (rotary switch) on the top of the unit.
The same axis No. is set for the L and M
axes.
Correctly set the axis No.
0 = No. 1 axis, 1 = No. 2 axis, ...
The value is duplicated with other axis.
Correctly set the axis No.
0 = No. 1 axis, 1 = No. 2 axis, ...
The axis No. is correctly set.
Replace the drive unit.
Alarm No.
12
Memory error 1
Hardware error (a CPU or an internal memory error was detected during the power ON self-check.
Investigation details
Investigation results
Remedies
SV
SP
1
Check the repeatability.
The error is always repeated.
Replace the drive unit.
The state returns to normal once, but occurs
sometimes thereafter.
Check the investigation item No. 2.
2
Check if there is any abnormality in the
unit's ambient environment.
(Ex. Ambient temperature, noise,
grounding)
Take remedies according to the causes of the abnormality in the ambient environment.
Alarm No.
13
Software processing error 1
An error was detected in the software execution state.
Software processing has not finished within the specified time.
Investigation details
Investigation results
Remedies
SV
SP
1
Check the repeatability.
The error is always repeated.
Replace the drive unit.
The state returns to normal once, but occurs
sometimes thereafter.
Check the investigation item No. 2.
2
Check if there is any abnormality in the
unit's ambient environment.
(Ex. Ambient temperature, noise,
grounding)
Take remedies according to the causes of the abnormality in the ambient environment.
[1] Machine grounding check
Alarm No.
16
Initial magnetic pole position detection error
In linear motor or IPM spindle motor using absolute position detector, the servo ON has been set before the magnetic pole
shift amount(servo:SV028,spindle:SP118) is set. In the initial magnetic pole position detection control, the pole position was
not correctly set.
Investigation details
Investigation results
Remedies
SV
SP
1
Check the parameters, SV028 (for the
servo) and SP118(for the spindle).
The parameters have not been set.
Set the magnetic shift pole amount(SP118).
The parameters have been set, but the
alarm occurs.
Carry out the magnetic pole estimation
again, as the setting value is wrong.
The setting parameter value is the same
even when initial magnetic pole function
was executed again.
Check the investigation item No. 2.
2
Check the repeatability.
The error is always repeated.
Replace the drive unit.
The state returns to normal once, but occurs
sometimes thereafter.
Check the investigation item No. 3.
3
Check if there is any abnormality in the
unit's ambient environment.
(Ex. Ambient temperature, noise,
grounding)
Take remedies according to the causes of the abnormality in the ambient environment.
[1] Machine grounding check
[2] Shield connection of the cable
Summary of Contents for C70
Page 1: ......
Page 3: ......
Page 9: ......
Page 11: ......
Page 13: ......
Page 18: ...1 1 Outline ...
Page 21: ...1 Outline MITSUBISHI CNC 4 ...
Page 22: ...5 2 GOT Initial Setup ...
Page 73: ...2 GOT Initial Setup MITSUBISHI CNC 56 ...
Page 74: ...57 3 PLC CPU Initial Setup ...
Page 91: ...3 PLC CPU Initial Setup MITSUBISHI CNC 74 ...
Page 92: ...75 4 CNC CPU Initial Setup ...
Page 105: ...4 CNC CPU Initial Setup MITSUBISHI CNC 88 ...
Page 106: ...89 5 Connecting and Setting up Multiple CNC CPU Modules ...
Page 115: ...5 Connecting and Setting up Multiple CNC CPU Modules MITSUBISHI CNC 98 ...
Page 116: ...99 6 Setting Machine Parameters ...
Page 130: ...113 7 Setting the Position Detection System ...
Page 153: ...7 Setting the Position Detection System MITSUBISHI CNC 136 ...
Page 154: ...137 8 Deceleration Check ...
Page 159: ...8 Deceleration Check MITSUBISHI CNC 142 ...
Page 160: ...143 9 Setting the Tool Entry Prohibited Range ...
Page 169: ...9 Setting the Tool Entry Prohibited Range MITSUBISHI CNC 152 ...
Page 170: ...153 10 Data Backup and Restoration ...
Page 184: ...167 Appendix 1 Explanation of Parameters ...
Page 435: ...Appendix 1 Explanation of Parameters MITSUBISHI CNC 418 ...
Page 436: ...419 Appendix 2 Explanation of Alarms ...
Page 608: ...591 Appendix 3 Display on 7 segment LED ...
Page 624: ......
Page 628: ......