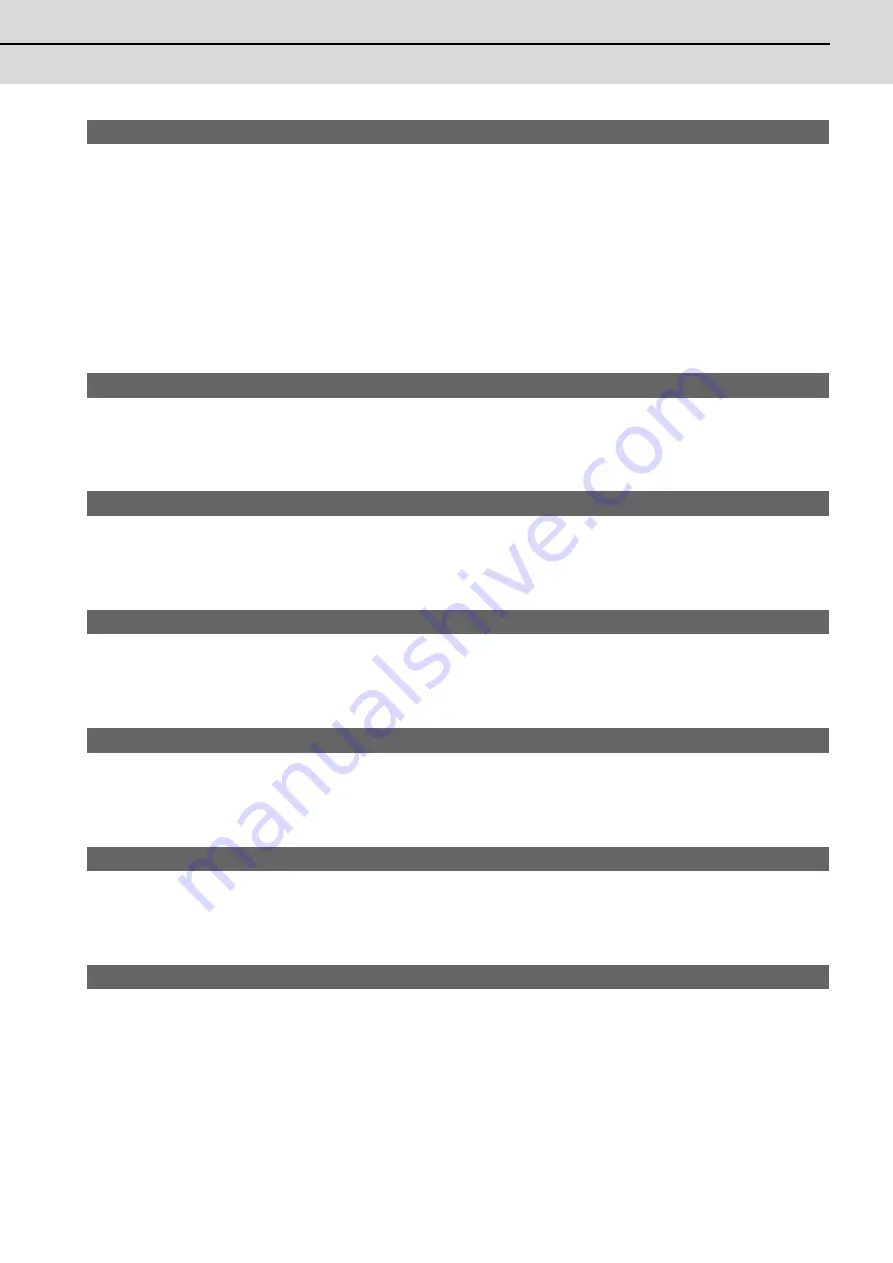
C70 Setup Manual
Appendix 1.4 Axis Specifications Parameters
247
【
#2180(PR)
】
S_DIN Speed monitor input door No.
Set the door signal input in the drive unit.
Use this parameter only when the axis with a door signal belongs to several door groups.
The correspondence between the door signals and bits are as follows.
bit0 : Door1 signal
bit1 : Door2 signal
:
bitF : Door16 signal
If the axis does not receive any door signal, set to "0".
An error (Y20 0027) will occur in the following cases.
- Several bits are enabled.
- Any bit other than those set in "#2118 S_DSl" is enabled.
---Setting range---
0000 to FFFF (HEX)
【
#2181(PR)
】
sscfeed1 Safety observation speed 1
Set the safety observation speed, which is at the machine end, in the multi-step speed monitor mode
1.
---Setting range---
0 to 18000 (mm/min or °/min)
【
#2182(PR)
】
sscfeed2 Safety observation speed 2
Set the safety observation speed, which is at the machine end, in the multi-step speed monitor mode
2.
---Setting range---
0 to 18000 (mm/min or °/min)
【
#2183(PR)
】
sscfeed3 Safety observation speed 3
Set the safety observation speed, which is at the machine end, in the multi-step speed monitor mode
3.
---Setting range---
0 to 18000 (mm/min or °/min)
【
#2184(PR)
】
sscfeed4 Safety observation speed 4
Set the safety observation speed, which is at the machine end, in the multi-step speed monitor mode
4.
---Setting range---
0 to 18000 (mm/min or °/min)
【
#2187(PR)
】
chgPLCax PLC axis switchover axis No.
Set the I/F No. of a PLC axis to use when switching between NC axis and PLC axis. Set the I/F No.
of a vacant PLC axis. Set to "0" when not using.
---Setting range---
0 to 8
【
#2605(PR)
】
BR_SIG Brake output signal number
Set a safety signal number for executing the brake test.
The brake test is not executed when "0" is set.
(E.g.) If "0x0c" is set, the brake output signal is Y0C on the side of PLC or Y20C on the side of NC
(when initial device number is 200).
* The safety output signal set in this parameter does not check the signal state on the NC side and
PLC side during brake test.
---Setting range---
0 to 0x1FF
Summary of Contents for C70
Page 1: ......
Page 3: ......
Page 9: ......
Page 11: ......
Page 13: ......
Page 18: ...1 1 Outline ...
Page 21: ...1 Outline MITSUBISHI CNC 4 ...
Page 22: ...5 2 GOT Initial Setup ...
Page 73: ...2 GOT Initial Setup MITSUBISHI CNC 56 ...
Page 74: ...57 3 PLC CPU Initial Setup ...
Page 91: ...3 PLC CPU Initial Setup MITSUBISHI CNC 74 ...
Page 92: ...75 4 CNC CPU Initial Setup ...
Page 105: ...4 CNC CPU Initial Setup MITSUBISHI CNC 88 ...
Page 106: ...89 5 Connecting and Setting up Multiple CNC CPU Modules ...
Page 115: ...5 Connecting and Setting up Multiple CNC CPU Modules MITSUBISHI CNC 98 ...
Page 116: ...99 6 Setting Machine Parameters ...
Page 130: ...113 7 Setting the Position Detection System ...
Page 153: ...7 Setting the Position Detection System MITSUBISHI CNC 136 ...
Page 154: ...137 8 Deceleration Check ...
Page 159: ...8 Deceleration Check MITSUBISHI CNC 142 ...
Page 160: ...143 9 Setting the Tool Entry Prohibited Range ...
Page 169: ...9 Setting the Tool Entry Prohibited Range MITSUBISHI CNC 152 ...
Page 170: ...153 10 Data Backup and Restoration ...
Page 184: ...167 Appendix 1 Explanation of Parameters ...
Page 435: ...Appendix 1 Explanation of Parameters MITSUBISHI CNC 418 ...
Page 436: ...419 Appendix 2 Explanation of Alarms ...
Page 608: ...591 Appendix 3 Display on 7 segment LED ...
Page 624: ......
Page 628: ......