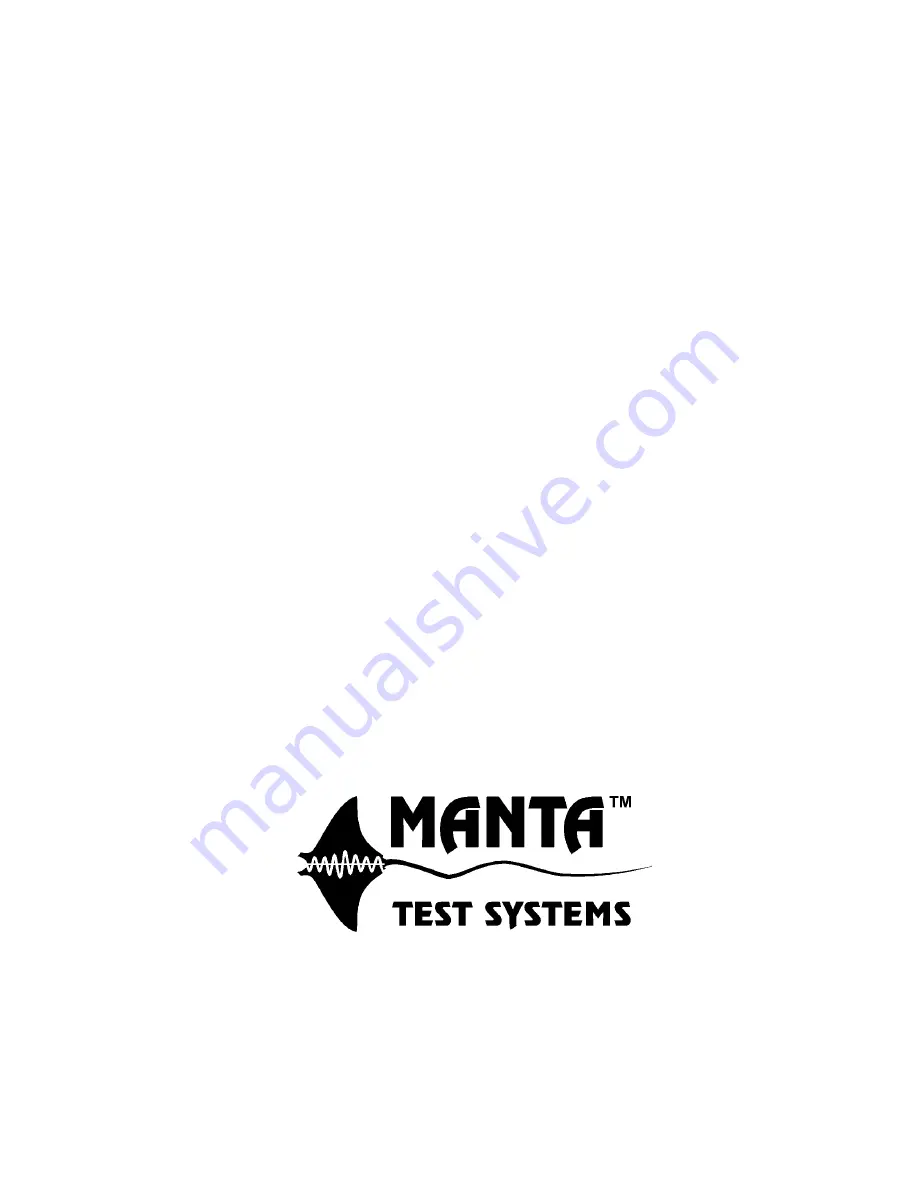
Manta Test Systems Incorporated
4060B Sladeview Crescent, Unit #1
Mississauga, Ontario, L5L 5Y5, Canada
Tel: +1(905) 828-6469 Fax: +1(905) 828-6850
e-mail: [email protected] Internet: http://www.mantatest.com
MTS-1700 SERIES
ADVANCED UNIVERSAL PROTECTIVE
RELAY TEST SYSTEM
OPERATION AND REFERENCE MANUAL
Fifteenth Edition
February 2003