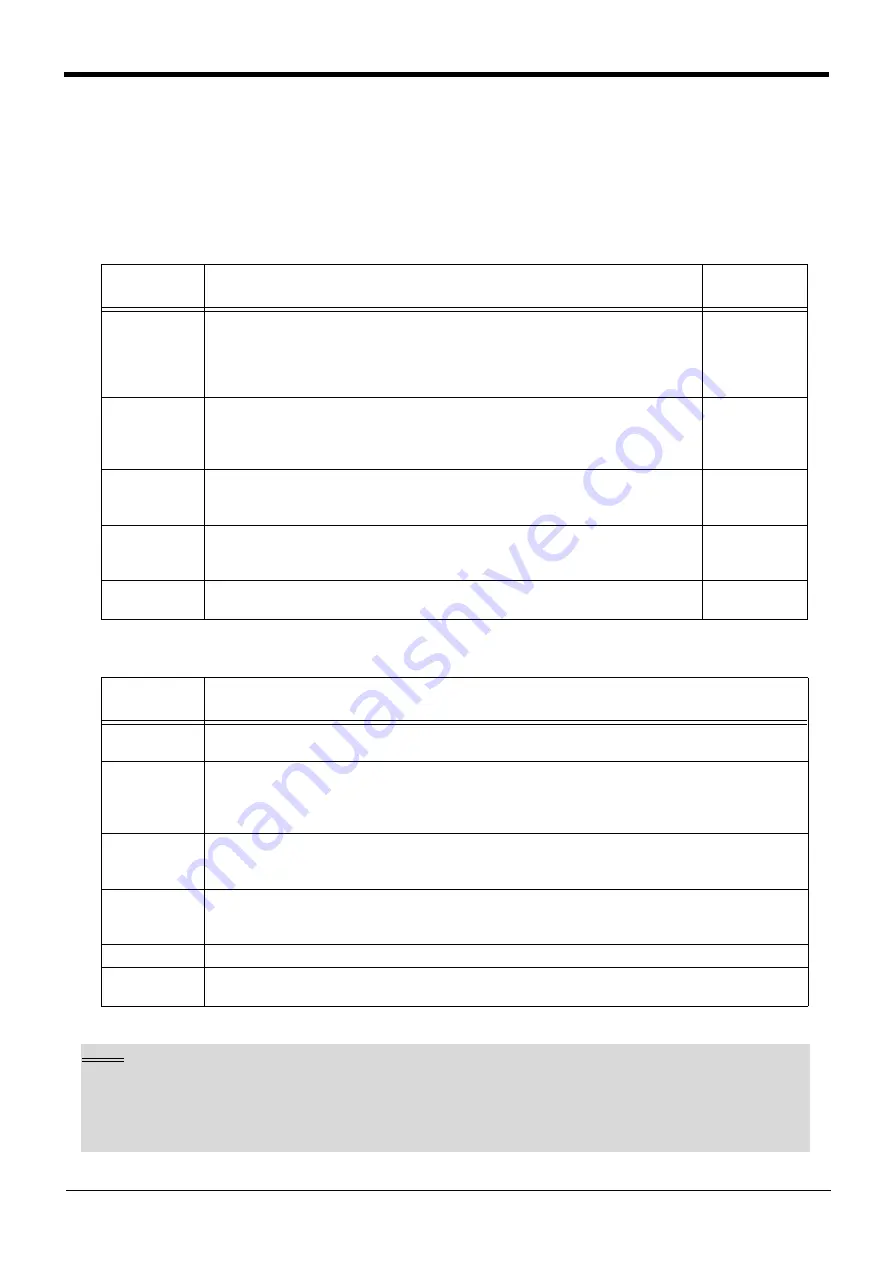
5-405
About the impact detection function
5Functions set with parameters
2)How to use the function at program operation
The initial state of the impact detection function at program operation is specified by a parameter. In prac-
tice, however, the function is used by changing the setting in a program using a MELFA-BASIC V instruc-
tion. The parameters for setting the initial state and instructions related to the impact detection function are
shown in the table below. Refer to
Page 152, "4.11 Detailed explanation of command words"
and
Detailed explanation of Robot Status Variable" for the detailed explanation of the instructions.
Table 5-20:Parameters to be set for the impact detection function at program operation.
Table 5-21:MELFA-BASIC V instructions and status variables used in the impact detection function at
program operation
Prameter
name
Description and value
Setting value at
shipment
COL
Define whether to enable or disable the impact detection function as well as
whether it is valid or invalid immediately after turning the power supply on.
Element 1: Enables (1) the impact detection function (enable (1)/disable (0))
Element 2: Set enable (1) as the initial state of the impact detection function at
program operation (enable (1)/disable (0)).
RV-SD series
0,0,1
RH-SDH series
1,0,1
COLLVL
Set the detection level (sensitivity) of each joint axis at jog operation (including
pause status).
(Reference) In the case of RV-3SD
The initial setting is 100, 100, 100, 100, 100, 100, 100, 100.
The setting var-
ies depending
on the model.
HNDDAT*
* is 1 to 8
Set the hand conditions (via tool coordinates).
(Reference) In the case of RV-3SD
The initial setting is 3.5,284.0,284.0,286.0,0.0,0.0,75.0.
The setting var-
ies depending
on the model.
WRKDAT*
* is 1 to 8
Set the workpiece conditions (via tool coordinates).
0.0, 0.0, 0.0,
0.0, 0.0, 0.0,
0.0
HNDHOLD*
* is 1 to 8
Specify whether to grab (1) or not grab (0) workpieces when the HOpen and
HClose instructions are executed.
0,1
Instruction/
Status variable
Description
ColChk
Enables or disables the impact detection function or specifies the NOERR mode.
Example: ColChk ON
'Enable the impact detection function.
COLLVL
Specifies the detection level (sensitivity) of the impact detection function for each joint axis. This
value is a scaling factor that amplifies the detection level standard value prescribed in the impact
detection function (unit: %).
Example: COLLVL 80, 120, 120, 120, 50, 80,
'Specify the detection levels of axes J1 to J6.
LoadSet
Specifies the hand and workpiece conditions. Use this instruction when the hand to be used or
workpieces to be grabbed are changed during program operation.
Example: LoadSet 1, 0
'Specify conditions of the HNDDAT1 and WRKDAT0 parameters.
J_ColMxl
Returns the maximum difference value between the estimated torque and actual torque by convert-
ing it to the detection level. It is referenced when adjusting the arguments of the COLLVL instruction
(unit: %).
M_ColSts
Returns 1 when an interference is detected. It is used as interrupt condition in the NOERR mode.
P_ColDir
Returns the robot operation direction (operation ratios in the X, Y and Z directions) when an interfer-
ence is detected. It is used in retreat operation in the NOERR mode.
Point
If the impact detection function is enabled for the entire program, the probability of erroneous detection
becomes higher accordingly. Hence, the detection level must be lowered in order to eliminate erroneous
detection. As a result, the interference detection sensitivity may be lowered for operations for which
impact detection is required. Thus, it is a good idea to use the impact detection function only for opera-
tions that may cause interference, so that the detection sensitivity may be kept high when in use.