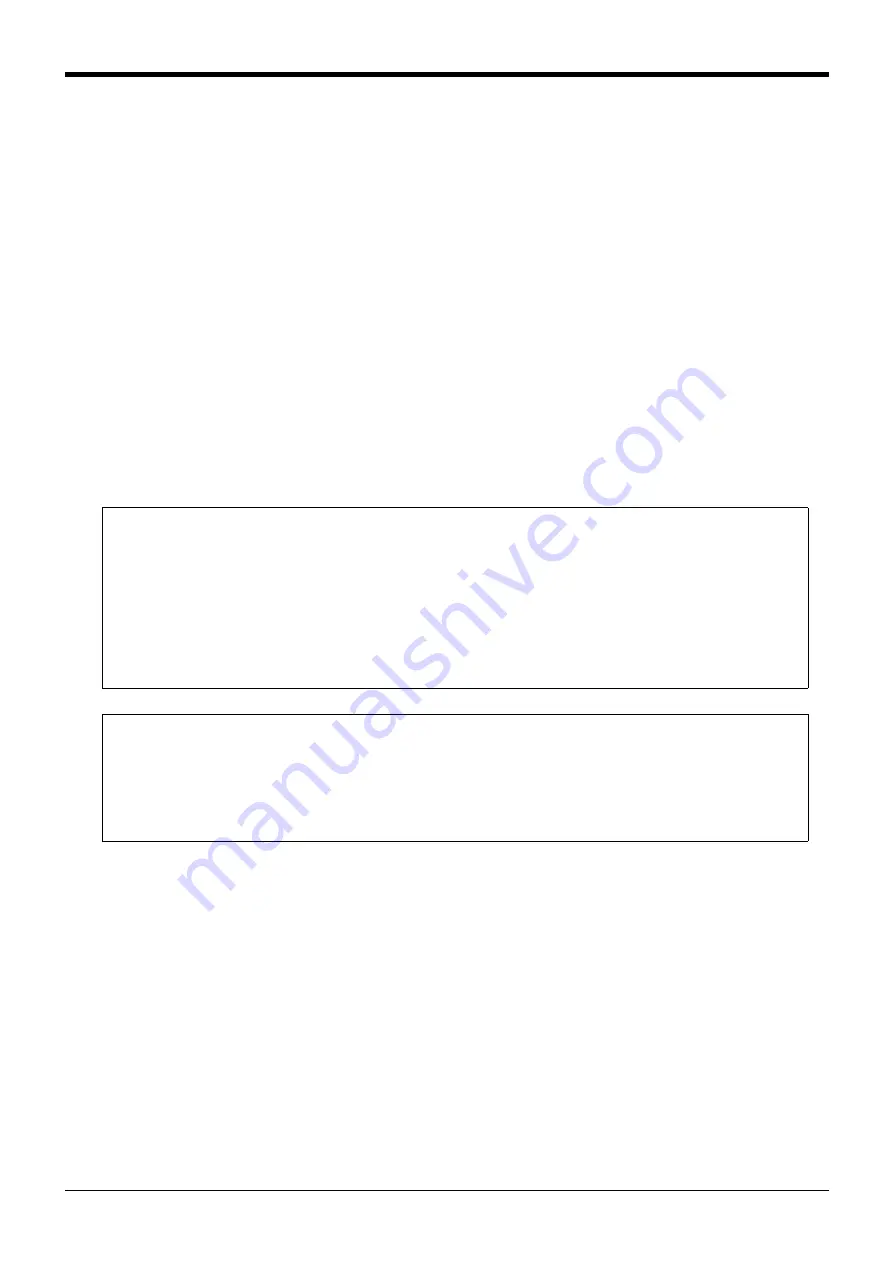
4MELFA-BASIC IV
Multitask function
4-120
4.2.4 Precautions for creating multitask program
(1) Relationship between number of tasks and processing time
During multitask operation, it appears as if several robot programs are being processed concurrently. How-
ever, in reality, only one line is executed at any one time, and the processing switches from program to pro-
gram (it is possible to change the number of lines being executed at a time. See the section for the "SLTn"
parameter in "Setting Functions by Parameters" on page 247). This means that if the number of tasks
increases, the overall program execution time becomes longer. Therefore, when using multitask operation,
the number of tasks should be kept to a minimum. However, programs of other tasks executing movement
instructions (the Mov and Mvs instructions) are processed at any time.
(2) Specification of the maximum number of programs executed concurrently
The number of programs to be run in parallel is set with parameter TASKMAX. (The default value is 8.) To
run more than 8 programs in parallel, change this parameter.
(3) How to pass data between programs via external variables
Data is passed between programs being executed in multitask operation via program external variables
such as M_00 and P_00 (refer to
Page 137, "4.3.22 External variables"
) and the user-defined external vari-
ables (refer to
Page 138, "4.3.24 User-defined external variables"
). An example is shown below. In this
example, the on/off status of input signal 8 is judged by the program specified in task slot 2. Then this pro-
gram notifies the program specified in task slot 1 that the signal is turned on by means of the external vari-
able M_00.
(4) Confirmation of operating status of programs via robot status variables
The status of the program running with multitask can be referred to from any slot using the robot status vari-
ables (M_Run, M_Wai, M-ERR).
Example) M1 = M_Run (2) The operation status of slot 2 is obtained.
Refer to
Page 140, "4.3.26 Robot status variables"
for details on the robot status variables.
(5) The program that operates the robot is basically executed in slot 1.
The program that describes the robot arm's movement, such as with the Mov commands, is basically set
and executed in slot 1. To run the program in a slot other than slot 1, the robot arm acquisition and release
command (GetM, RelM) must be used. Refer to
Page 152, "4.11 Detailed explanation of command words"
in this manual for details on the commands.
(6) How to perform the initialization processing via constantly executed programs
Programs specified in task slots whose start condition is set to ALWAYS are executed continuously (repeat-
edly) if the operation mode is set to REP. Therefore, in order to perform the initialization processing via such
programs, they should be programmed in such a way that the initialization processing is not executed more
than once, for example by setting an initialization complete flag and perform a conditional branch based on
<Slot 1>
1 M_00=0
; Substitute 0 in M_00
2 *L
3 If M_00=0 Then *L
; Wait for M_00 value to change from 0.
4 M_00=0
; Substitute 0 in M_00
5 Mov P1
; Proceed with the target work.
6 Mov P2
:
10 GoTo *L
; Repeat from step 2.
<Slot 2>
(Program of signals and variables)
1 If M_In(8) <> 1 Then *A1
; Branch to line 30 if input signal 8 is not ON.
2 M_00=1
; Substitute 1 in M_00
3 *A1
4 Mov P1
; Proceed with the target work.
: