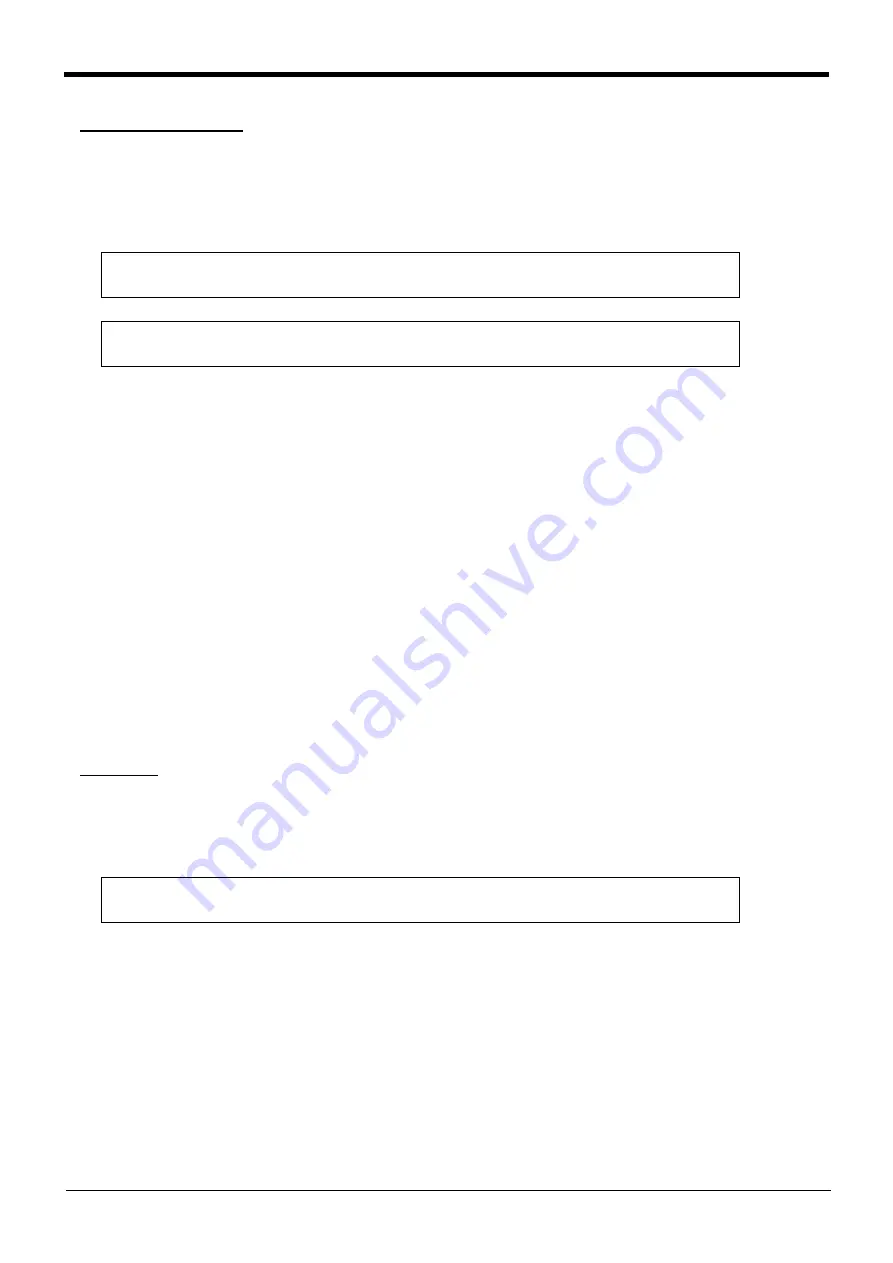
4-271
Detailed explanation of Robot Status Variable
4MELFA-BASIC IV
J_Fbc/J_AmpFbc
[Function]
J_Fbc:Returns the current position of the joint type that has been generated by encoder feedback.
J_AmpFbc:Returns the current feedback value of each axis
[Format]
[Terminology]
<Joint Type Variable>
Specify a joint type variable to be assigned.
<Mechanism Number>
Enter the mechanism number. 1 to 3, If the argument is omitted, 1 is set as the
default value.
[Reference Program]
1 J1=J_Fbc
' J1 will contain the current position of the joint that has been generated by
servo feedback.
2 J1=J_AmpFbc
' The present current feedback value is entered in J2.
[Explanation]
(1) J_Fbc returns the present position of the joint type generated by the feedback of the encoder.
(2) J_Fbc can check the difference between the command value to the servo and the delay in the actual
servo.
(3) J_Fbc can also check if there is a difference as a result of executing a Cmp Jnt instruction.
(4) This variable only reads the data.
[Reference]
J_Origin
[Function]
Returns the joint data when the origin has been set.
[Format]
[Terminology]
<Joint Type Variable>
Specify a joint type variable to be assigned.
<Mechanism Number>
Enter the mechanism number. 1 to 3, If the argument is omitted, 1 is set as the
default value.
[Reference Program]
1 J1=J_Origin(1)
' J1 will contain the origin setting position of mechanism 1.
[Explanation]
(1) Returns the joint data when the origin has been set.
(2) This can be used to check the origin, for instance, when the position of the robot shifted.
(3) This variable only reads the data.
Example) <Joint Type Variable>=J_Fbc [(<Mechanism Number>)]
Example) <Joint Type Variable>=J_AmpFbc [(<Mechanism Number>)]
Example) <Joint Type Variable>=J_Origin [(<Mechanism Number>)]