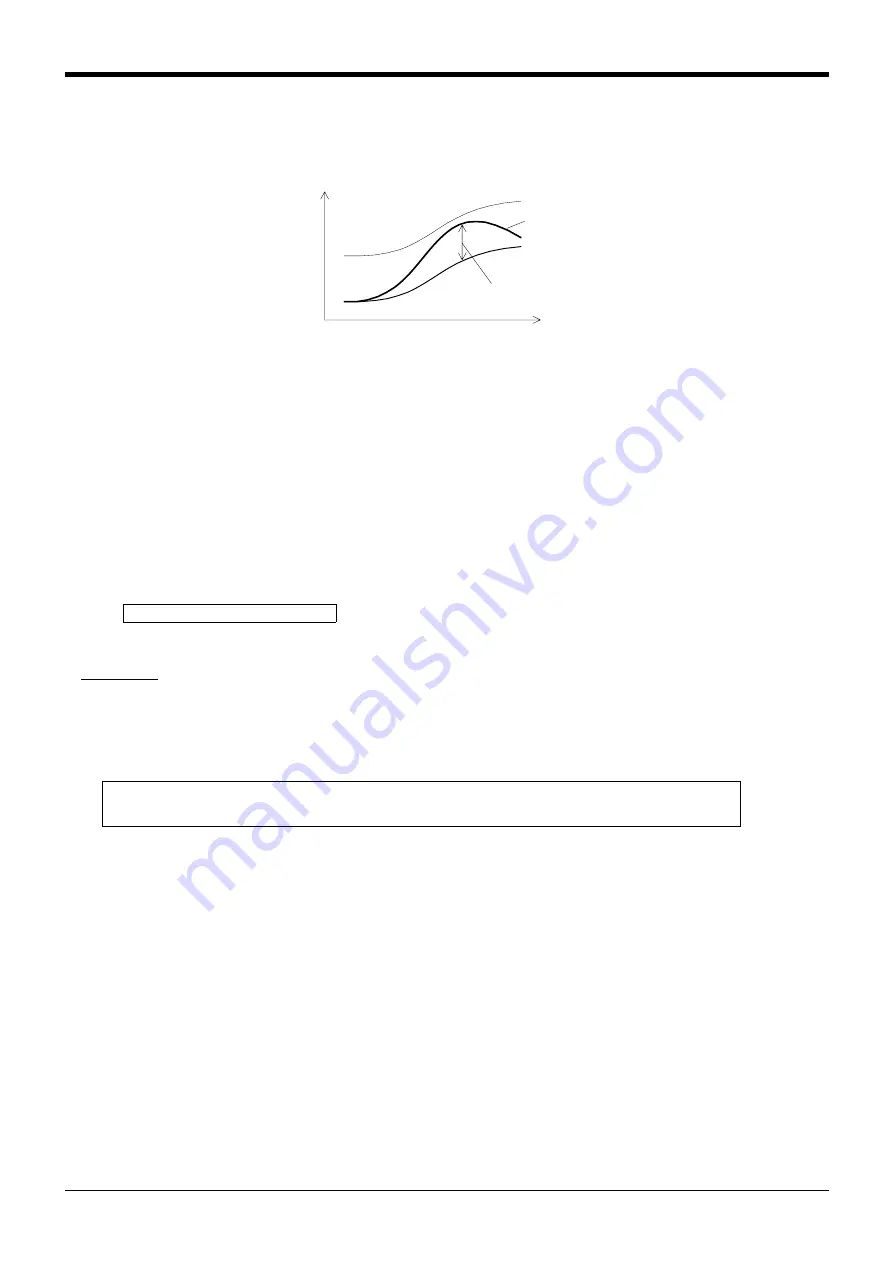
4MELFA-BASIC IV
Detailed explanation of Robot Status Variable
4-270
[Explanation]
(1) Keep the maximum value of the error of the estimated torque and actual torque of each axis while impact
detection function is valid.
(2) When this value is 100%, it indicates that the maximum error value is the same as the manufacturer's ini-
tial value of the allowable impact level.
(3) For robots that prohibit the use of impact detection, 0.0 is always returned for all axes.
(4) The maximum error value is initialized to 0.0 when the servo is turned ON during the execution of a
ColChk ON or COLLVL instruction.
(5) Because they are joint-type variables, it will be conversion values from rad to deg if they are read as joint
variables. Therefore, substitute each axis element by a numeric variable as shown in the syntax exam-
ple when using these joint-type variables.
(6) This variable only reads the data.
[Reference]
ColChk (Col Check), ColLvl (Col Level), M_ColSts, P_ColDir
[Available robot type]
J_ECurr
[Function]
Returns the current encoder pulse value.
[Format]
[Terminology]
<Joint Type Variable>
Specify a joint type variable to be assigned.
<Mechanism Number>
Enter the mechanism number. 1 to 3, If the argument is omitted, 1 is set as the
default value.
[Reference Program]
1 J1=J_ECurr(1)
' JA will contain the encoder pulse value of mechanism 1.
2 MA=JA. 1
’ Loads the encoder pulse value of the J1 axis to the MA.
[Explanation]
(1) Although the value to be returned is a pulse value, use the joint type as the substitution type. Then, spec-
ify joint component data, and use by substituting in a numeric variable.
(2) This variable only reads the data.
RV-6SD/6SDL/12SD/12SDL series
Example) <Joint Type Variable>=J_ECurr [(<Mechanism Number>)]
Estimated
torque
Actual torque
COLMXL
COLLVL
Torque
Time