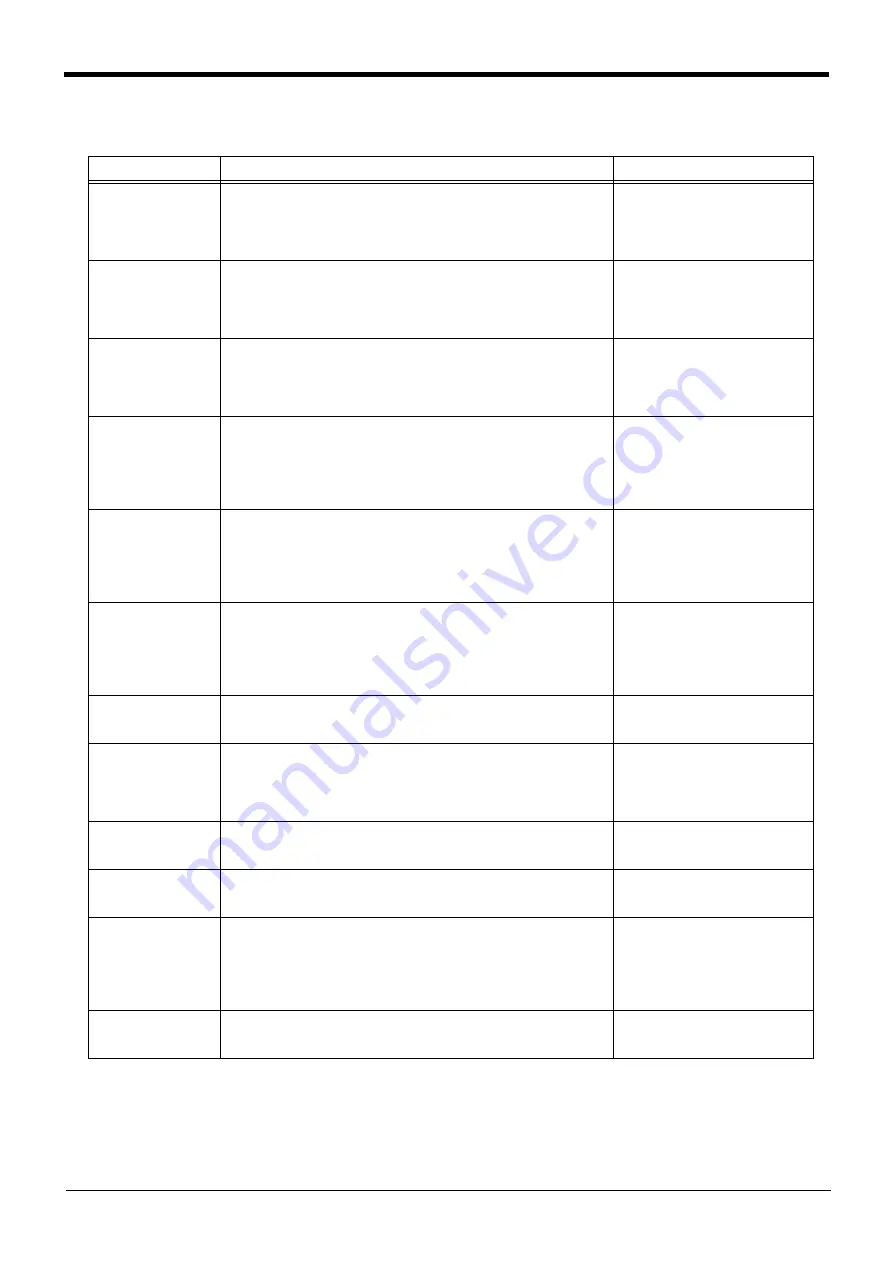
2-11
Functions Related to Movement and Control
2Explanation of functions
2.3 Functions Related to Movement and Control
This controller has the following characteristic functions.
Function
Explanation
Explanation page
Optimum speed control This function prevents over-speed errors as much as possible by limiting
the speed while the robot is tracking a path, if there are postures of the
robot that require the speed to be limited while moving between two
points. However, the speed of the hand tip of the robot will not be con-
stant if this function is enabled.
Optimum acceleration/
deceleration control
This function automatically determines the optimum acceleration/deceler-
ation time when the robot starts to move or stops, according to the weight
and center of gravity settings of the hand, and the presence of a work-
piece. The cycle time improves normally, although the cycle time
decreases by the condition..
Page 229, "Oadl (Optimal Accelera-
tion)"
,
Page 213, "Loadset (Load Set)"
XYZ compliance
With this function, it is possible to control the robot in a pliable manner
based on feedback data from the servo. This function is particularly effec-
tive for fitting or placing workpieces. Teaching along the robot's orthogo-
nal coordinate system is possible. However, depending on the workpiece
conditions, there are cases where this function may not be used.
Page 167, "Cmp Tool (Composition
Tool)"
Impact Detection
The robot stops immediately if the robot's tool or arm interferes with a
peripheral device, minimizing damage.
This function can be activated during automatic operation as well as dur-
ing jog operation.
Note) Please note that this function cannot be used together with the
multi-mechanism control function.
Page 174, "ColChk (Col Check)"
Refer to "COL" parameter in
343, "5 Functions set with parame-
ters"
Maintenance Forecast
The maintenance forecast function forecasts the robot's battery, belt and
grease maintenance information based on the robot's operating status.
This function makes it possible to check maintenance information using
the optional Personal Computer Support software.
Note) Please note that this function cannot be used together with the
multi-mechanism control function.
Use optional Personal Computer
Support software.
Position Restoration
Support
The position restoration support function calculates the correction values
of OP data, tools and the robot base by only correcting a maximum of
several 10 points if a deviation in the joint axis, motor replacement, hand
deformation or a deviation in the robot base occurs, and corrects position
deviation. This function is implemented by optional Personal Computer
Support software.
Use optional Personal Computer
Support software.
Vertical multi-joint robot:
Continuous path con-
trol
This function is used to operate the robot between multiple positions con-
tinuously without acceleration or deceleration. This function is effective to
improvement of the cycle time.
Page 92, "(4) Continuous move-
ment"
Multitask program
operation
With this function, it is possible to execute programs concurrently by
grouping between programs for the robot movement, programs for com-
munication with external devices, etc. It is effective to shorten input/out-
put processing. In addition, it is possible to construct a PLC-less system
by creating a program for controlling peripheral jigs.
Refer to X*** instructions such as
Page 117, "4.2.1 What is multitask-
ing?"
.
Program constant exe-
cution function
With this function, it is possible to execute a program all the time after the
controller's power is turned on. This function is effective when using the
multitask functions to make the robot program serve as a PLC.
Refer to "SLTn" parameter start
attribute (ALWAYS) in
Functions set with parameters"
Continuity function
With this function, it is possible to store the status at power off and
resume from the same status when the power is turned on again.
Refer to "CTN" parameter in
343, "5 Functions set with parame-
ters"
Additional axis control
With this function, it is possible to control up to two axes as additional
axes of the robot. Since the positions of these additional axes are stored
in the robot's teaching data as well, it is possible to perform completely
synchronous control. In addition, arc interpolation while moving additional
axes (travelling axes) is also possible. The additional axis interface card
optional is required of CR1/CR2 series controller.
Separate manual "ADDITIONAL
AXIS INTERFACE".
Multi-mechanism con-
trol
With this function, it is possible to control up to two (excluding the stan-
dard robots) robots (user mechanism) driven by servo motors, besides
the standard robots.
Separate manual "ADDITIONAL
AXIS INTERFACE".