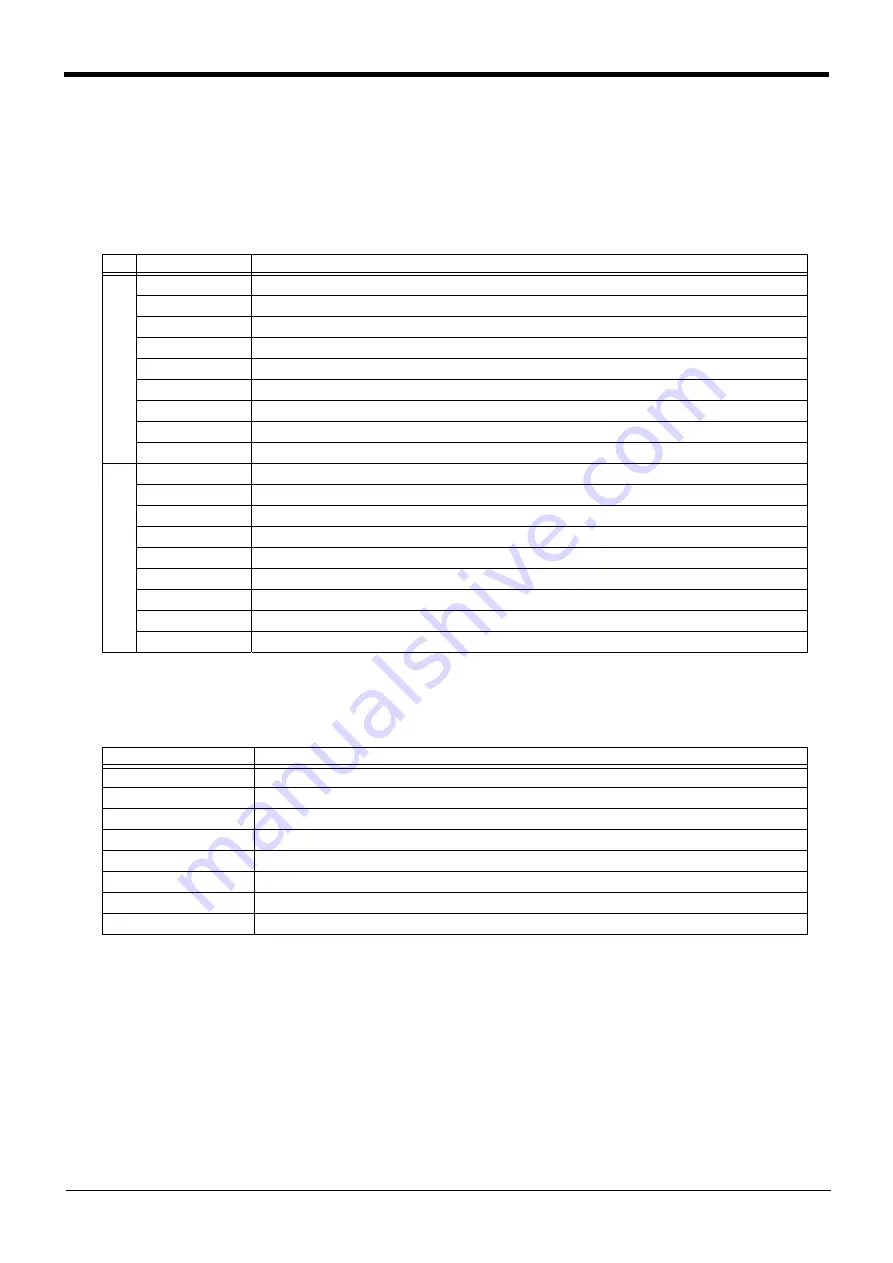
5-377
Hand and Workpiece Conditions (optimum acceleration/deceleration settings)
5Functions set with parameters
5.16 Hand and Workpiece Conditions (optimum acceleration/deceleration settings)
Optimum acceleration/deceleration control allows the optimum acceleration/deceleration to be performed by
LoadSet and Oadl instructions automatically in response to the load at the robot tip. The following parame-
ters must be set correctly in order to obtain the optimum acceleration/deceleration.
This parameter is also used in the impact detection function installed in the RV-SD/RH-SDH series.
When using the impact detection function during jog operation, set HNDDAT0 and WRKDAT0 correctly.
The factory default setting is as follows.
Parameter values define, from the left in order, weight, size X, Y, and Z, and center of gravity X, Y, and Z. Up
to eight hand conditions and eight workpiece conditions can be set. For the size of a hand, enter the length
of a rectangular solid that can contain a hand. Optimal acceleration/deceleration will be calculated from the
hand condition and the workpiece condition specified by a LoadSet instruction.
Parameter values that define grasping or not grasping is shown from the left for cases where the hand is
open or closed.
"0" = Set to not grasping
"1" = Set to grasping
Depending on the hand's open/close status, optimum acceleration/deceleration calculation will be per-
formed for either hand-alone condition or hand-and-workpiece condition.
The hand's open/close status can be changed by executing the HOpen/HClose instruction.
The coordinate axes used as references when setting the hand and workpiece conditions are shown below
for each robot model. The references of the coordinate axes are the same for both the hand and workpiece
conditions. Note that all the sizes are set in positive values.
Parameter
Value
se
tting th
e hand conditions
HNDDAT0
It varies with models.
HNDDAT1
Maximum load, 0.0, 0.0, 0.0, 0.0, 0.0, 0.0
HNDDAT2
Maximum load, 0.0, 0.0, 0.0, 0.0, 0.0, 0.0
HNDDAT3
Maximum load, 0.0, 0.0, 0.0, 0.0, 0.0, 0.0
HNDDAT4
Maximum load, 0.0, 0.0, 0.0, 0.0, 0.0, 0.0
HNDDAT5
Maximum load, 0.0, 0.0, 0.0, 0.0, 0.0, 0.0
HNDDAT6
Maximum load, 0.0, 0.0, 0.0, 0.0, 0.0, 0.0
HNDDAT7
Maximum load, 0.0, 0.0, 0.0, 0.0, 0.0, 0.0
HNDDAT8
Maximum load, 0.0, 0.0, 0.0, 0.0, 0.0, 0.0
setting
the wor
k
piece co
nditions
WRKDAT0
It varies with models.
WRKDAT1
0.0, 0.0, 0.0, 0.0, 0.0, 0.0, 0.0
WRKDAT2
0.0, 0.0, 0.0, 0.0, 0.0, 0.0, 0.0
WRKDAT3
0.0, 0.0, 0.0, 0.0, 0.0, 0.0, 0.0
WRKDAT4
0.0, 0.0, 0.0, 0.0, 0.0, 0.0, 0.0
WRKDAT5
0.0, 0.0, 0.0, 0.0, 0.0, 0.0, 0.0
WRKDAT6
0.0, 0.0, 0.0, 0.0, 0.0, 0.0, 0.0
WRKDAT7
0.0, 0.0, 0.0, 0.0, 0.0, 0.0, 0.0
WRKDAT8
0.0, 0.0, 0.0, 0.0, 0.0, 0.0, 0.0
Parameter
Value(Factory default)
HNDHOLD1
0, 1
HNDHOLD2
0, 1
HNDHOLD3
0, 1
HNDHOLD4
0, 1
HNDHOLD5
0, 1
HNDHOLD6
0, 1
HNDHOLD7
0, 1
HNDHOLD8
0, 1