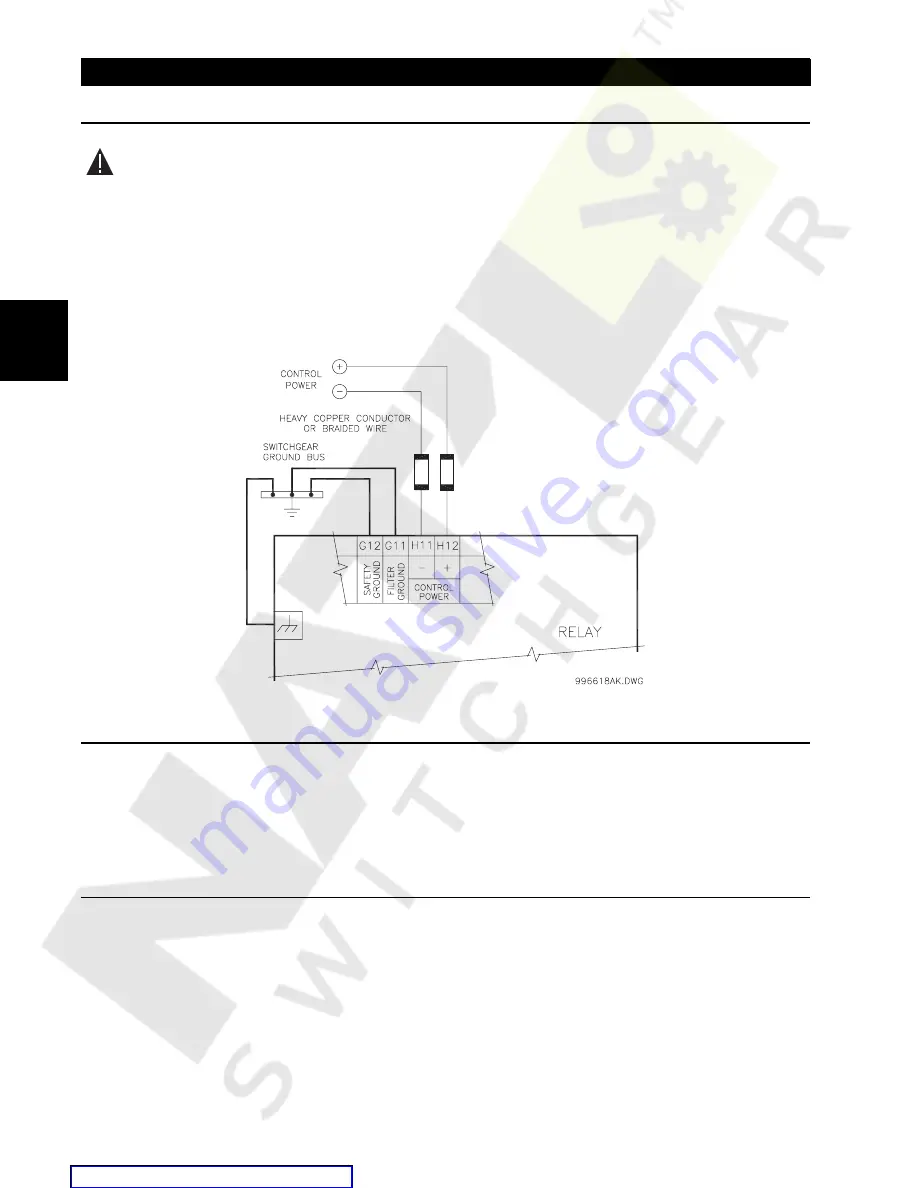
3-10
745 Transformer Management Relay
GE Multilin
3.2 TYPICAL WIRING
3 INSTALLATION
3
3.2.8 CONTROL POWER
Control power supplied to the relay must match the installed power supply range. If the applied voltage
does not match, damage to the unit may occur.
The label found on the left side of the relay specifies its order code or model number. The installed power supply operating
range will be one of the following.
LO: 25 to 60 V DC or 20 to 48 V AC
HI: 88 to 300 V DC or 70 to 265 V AC
Ensure the applied control voltage matches the requirements of the relay’s switching power supply. For example, the HI
power supply will work with any DC voltage from 88 to 300 V, or any AC voltage from 70 to 265 V. The internal fuse may
blow if the applied voltage exceeds this range.
Figure 3–11: CONTROL POWER CONNECTION
3.2.9 ANALOG INPUT
Terminals A1 (+) and A2 (–) are provided for the input of a current signal, from one of the following: 0 to 1 mA, 0 to 5 mA,
0 to 20 mA, or 4 to 20 mA transducer outputs. This current signal can represent any external quantity, such as temperature,
current or voltage. Be sure to observe polarity markings for correct operation. Both terminals are clamped to within 36 volts
of ground with surge protection. As such, common mode voltages should not exceed this limit. Shielded wire, with only one
end of the shield grounded, is recommended to minimize noise effects. The A2 (–) terminal must be connected to the A5
(Analog Output Common) terminal at the 745.
3.2.10 TAP POSITION INPUT
Terminals A3 (+) and A4 (–) are provided to monitor the position of an Onload Tap Changer from a stepped-resistance posi-
tion indicator device. Terminal A3 is connected internally to a 4.3 mA current source. This current is used to measure the
value of the external resistance. The 745 uses the measured resistance value to calculate the Tap Position. See Section
5.2.2 Dynamic CT Ratio Mismatch Correction on page 5–5 for more details on the tap position input.
The maximum total resistance the Tap Changer input can measure is 5.1 K
Ω
. For example, the maximum resistance incre-
ment per tap for a 33-position Tap Changer should not exceed 151
Ω
.
WARNING
Содержание TRANSFORMER MANAGEMENT RELAY 745
Страница 2: ...Courtesy of NationalSwitchgear com ...