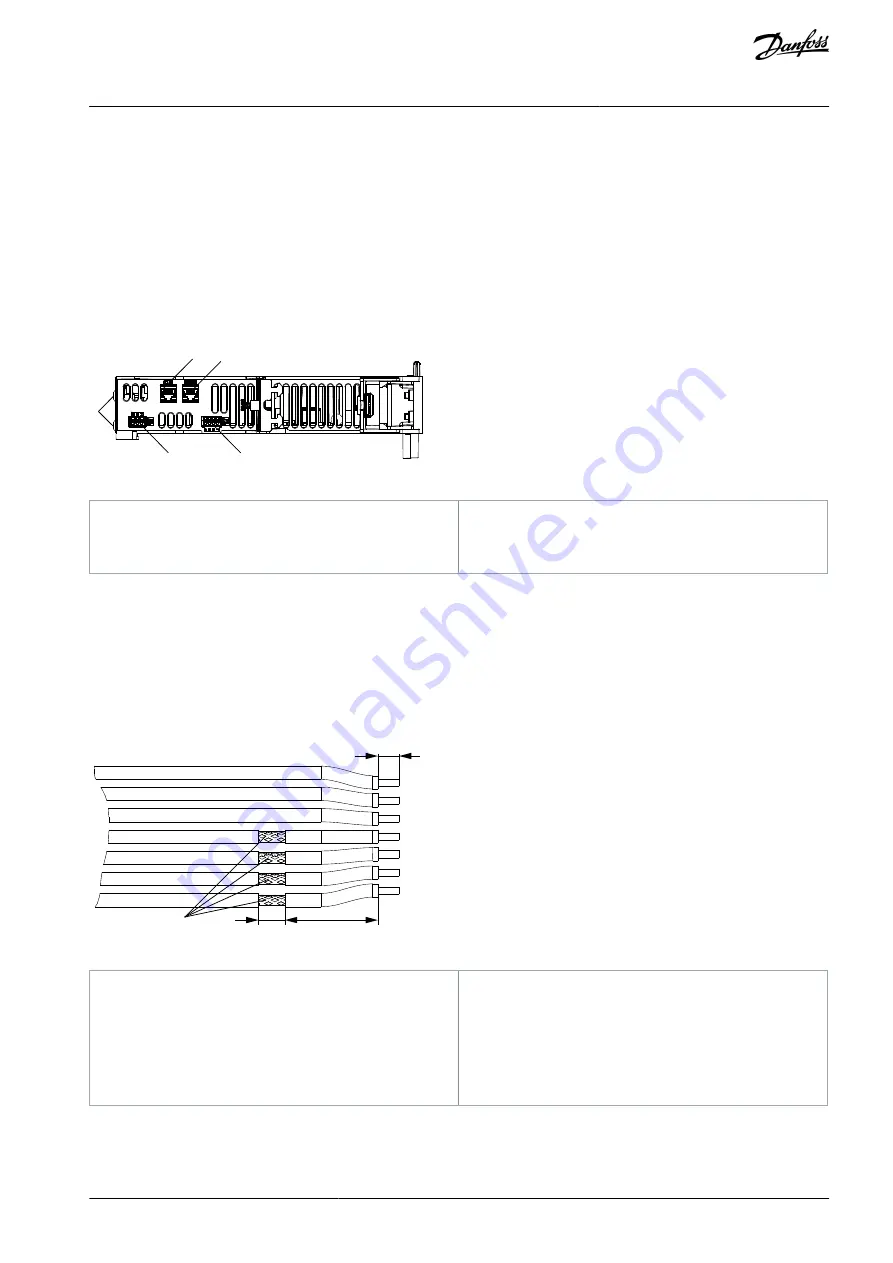
1.
2.
3.
4.
5.
6.
7.
1.
2.
3.
4.
Procedure
Insert the wires into the UDC, AUX, and STO connectors.
Secure the feed-in cable using the cable ties [3], ensuring that the shielded area is positioned exactly under the cable tie.
Secure the STO cable using the cable tie [4], ensuring that the shielded area is positioned exactly under the cable tie.
Insert the connectors on the feed-in cable into their corresponding terminal block on the DAM 510.
Tighten the screw on the EMC plate [6]. The tightening torque is 3 Nm.
Insert the RJ45 bus connector [2].
Connect the DAM 510 to PE using one of the PE screws on the front side [1] and a PE wire. The tightening torque is 3 Nm.
5.12 Connecting the Auxiliary Capacitors Module ACM 510
e3
0b
h3
50
.1
1
1
2
4
5
3
Illustration 51: Connectors on the Top of ACM 510
1
Ethernet connector IN (X1 IN)
2
Ethernet connector OUT (X2 OUT)
3
I/O connector (I/O ACM)
4
Relay connector (REL ACM)
Procedure
Connect the Ethernet cable from the output of the previous system module to the input connector (X1 IN) [1].
If I/Os are required, insert the wires into the I/O connector (I/O ACM) and insert the connector [3].
If a relay is required, insert the wires into the relay connector (REL ACM) and insert the connector [4].
Connect the ACM 510 to PE using one of the PE screws on the front side [5] and a PE wire.. The tightening torque is 3 Nm.
5.13 Connecting the Expansion Module EXM 510
12
53
15
8
1
2
3
4
5
6
7
e3
0b
h6
61
.1
0
Illustration 52: Expansion Module Cable
1
24/48 V
2
GND
3
Functional earth
4
DC–
5
DC–
6
DC+
7
DC+
8
Shielded area
AQ262449648484en-000101 / 175R1135 | 79
Danfoss A/S © 2020.08
Electrical Installation
VLT® Servo Drive System ISD 510/DSD 510
Operating Guide