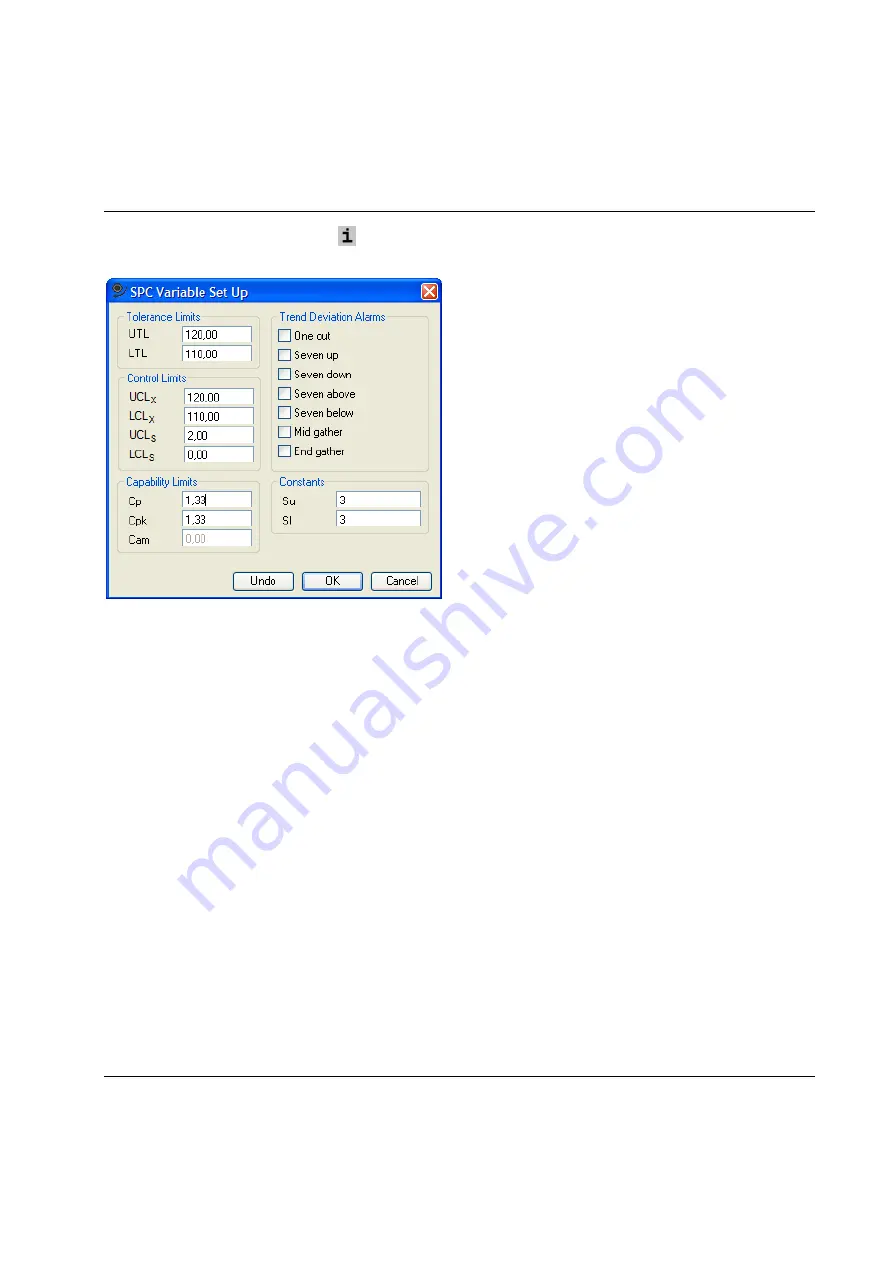
SPC and Statistics
9836 3521 01
409
If you press the Information button
a dialog box is presented where you can enter various check values
for the selected variable.
If you have marked
Auto recalculation of limits
on the first page, the
UCL
X
,
LCL
X
, UCL
R/S
and
LCL
R/S
,
fields will show current value of the control limits. If you disable automatic recalculation you can manually
enter control limits in these fields.
Cam limit is only applicable if cam can be calculated.
Check one or more of the check boxes in the
Trend Deviation Alarms
frame to have the SPC and TDA
data monitored for any of the following deviations:
One out
: One point outside control levels
Seven up
: Seven points consecutively increasing
Seven down
: Seven points consecutively decreasing
Seven above
: Seven points consecutively above average
Seven below
: Seven points consecutively below average
Mid gather
: More than 90% of the points in mid third
End gather
: Less than 40% of the points in mid third
If a deviation is detected an event of type SPC is generated and stored in the Event Log (see also View
Event Log).
Содержание PowerMACS 4000
Страница 1: ...User guide PowerMACS 4000 Atlas Copco Tools and Assembly Systems 9836 3521 01 2010 11 Edition 10 3 0...
Страница 2: ......
Страница 46: ...System Architecture 46 9836 3521 01...
Страница 127: ...Set Up and Maintenance 9836 3521 01 127 See chapter Station Set Up for a description of the parameters...
Страница 267: ...Tightening 9836 3521 01 267...
Страница 400: ...Tightening 400 9836 3521 01...
Страница 422: ...Peripheral Devices 422 9836 3521 01 When connected to a system the form will show show the signal values in realtime...
Страница 486: ...Peripheral Devices 486 9836 3521 01...
Страница 622: ...Peripheral Devices 622 9836 3521 01...
Страница 664: ...References 664 9836 3521 01...
Страница 668: ...9836 3521 01 2010 11 Edition 10 3 0 www atlascopco com...