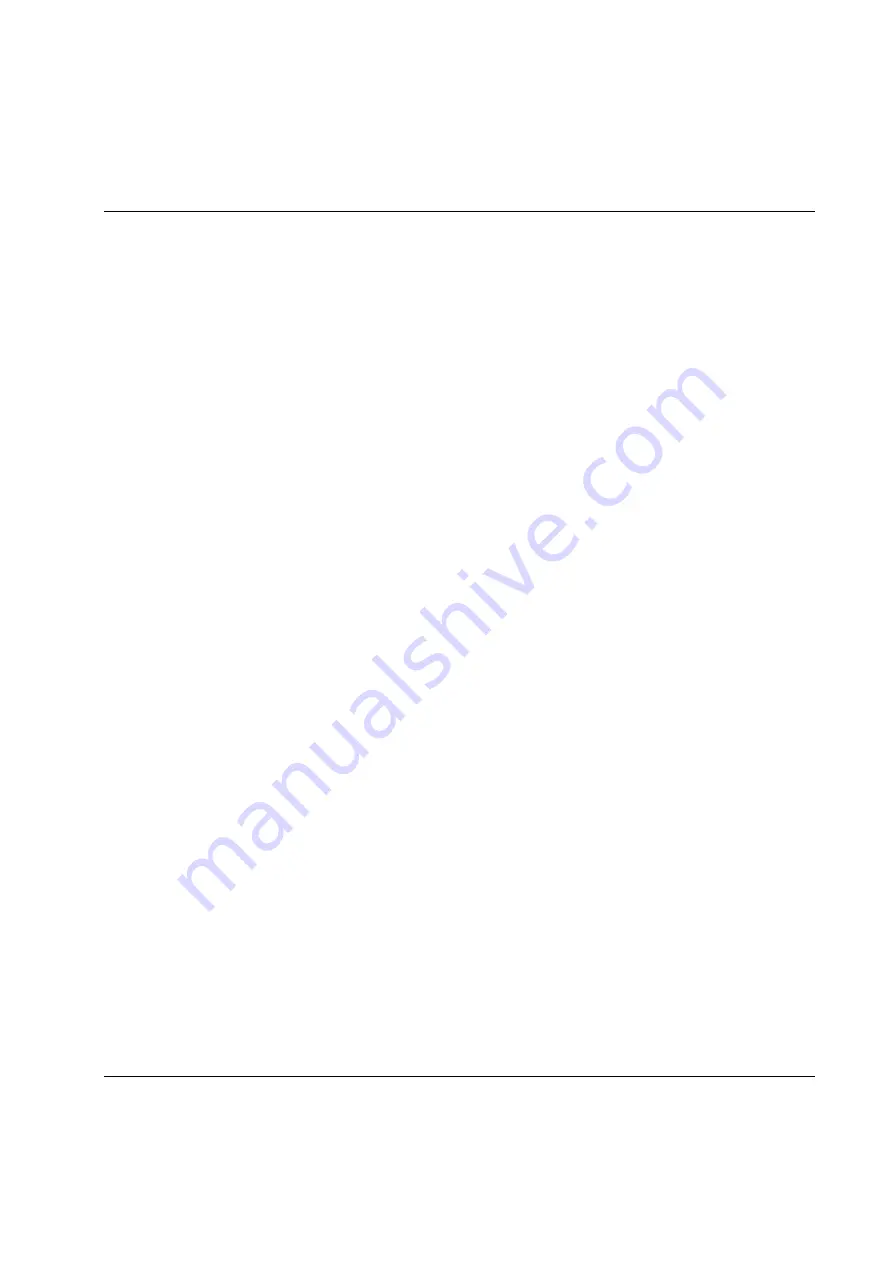
Set Up and Maintenance
136
9836 3521 01
Note! Allowing hold torque during RM dramatically increases the risk of burning the motors!
Report Cycle Data at emerg. stop
controls whether or not cycle data is reported for a cycle interrupted
by an emergency stop (caused by setting the PLC variables EMERGSTOP or MACHINESTOP, or if the
Station loses communication with one or more of its TCs). Uncheck it to automatically drop all result data
for such cycles.
With the
Automatically restart TC on fatal errors
parameter you can control whether or not the TCs
used by this Station should reset themselves if they run into an unrecoverable software error. If the TC
running the Station controller is automatically restarted it will
always
set its own status, and the status of
all its bolts, to NOK to make sure that a NOK cycle is not reported as OK by accident. This is done also if
the Station was not running a cycle when it restarted. All TCs that is restarted due to a fatal error will
generate an event in the event log when they do so. More detailed information on the error causing the
restart can be retrieved using the TC Crash Log.
With the
Disconnect bolts that fails to start
parameters the Station can be configured to automatically
disconnect bolts that cannot be started either due to a communication error (Ethernet) or a servo error.
Set
Max no. of bolts to disconnect
to the maximum number of bolts that may be disconnected
automatically due to communication or servo errors. Possible values are between from zero up to the
number of TCs in the Station minus one.
The radio buttons
Select Disconnect with status OK
and
Disconnect with status NOK
controls with
which status the bolts are reported if they are disconnected.
Note! It is not recommended to use the Select Disconnect with status OK choice since it will
cause non-tightened bolts to be reported as OK.
As long as the total number of automatically disconnected bolts is less than
Max no. of bolts to
disconnect
the event "Failed to reach TC. Bolt is disconnected (OK/NOK)" is generated for each TC that
cannot be contacted. When the maximum number of disconnects has been reached the event "Station
has no contact with spindle X" is generated for each additional failing bolt.
If at least one, and less then or equal the maximum number of allowed, bolt(s) have been disconnected
the event "Station starts the cycle even though X spindles could not be reached" is generated.
For each bolt that is disconnected due to servo failure during initialization the event "Failed to init servo.
Bolt is disconnected (OK/NOK)" is generated.
Press the
Open…
button to open the Advanced Station Settings form for additional settings, alternatively
you can right click on a station and select Advanced Station Settings from the popup menu.
Содержание PowerMACS 4000
Страница 1: ...User guide PowerMACS 4000 Atlas Copco Tools and Assembly Systems 9836 3521 01 2010 11 Edition 10 3 0...
Страница 2: ......
Страница 46: ...System Architecture 46 9836 3521 01...
Страница 127: ...Set Up and Maintenance 9836 3521 01 127 See chapter Station Set Up for a description of the parameters...
Страница 267: ...Tightening 9836 3521 01 267...
Страница 400: ...Tightening 400 9836 3521 01...
Страница 422: ...Peripheral Devices 422 9836 3521 01 When connected to a system the form will show show the signal values in realtime...
Страница 486: ...Peripheral Devices 486 9836 3521 01...
Страница 622: ...Peripheral Devices 622 9836 3521 01...
Страница 664: ...References 664 9836 3521 01...
Страница 668: ...9836 3521 01 2010 11 Edition 10 3 0 www atlascopco com...