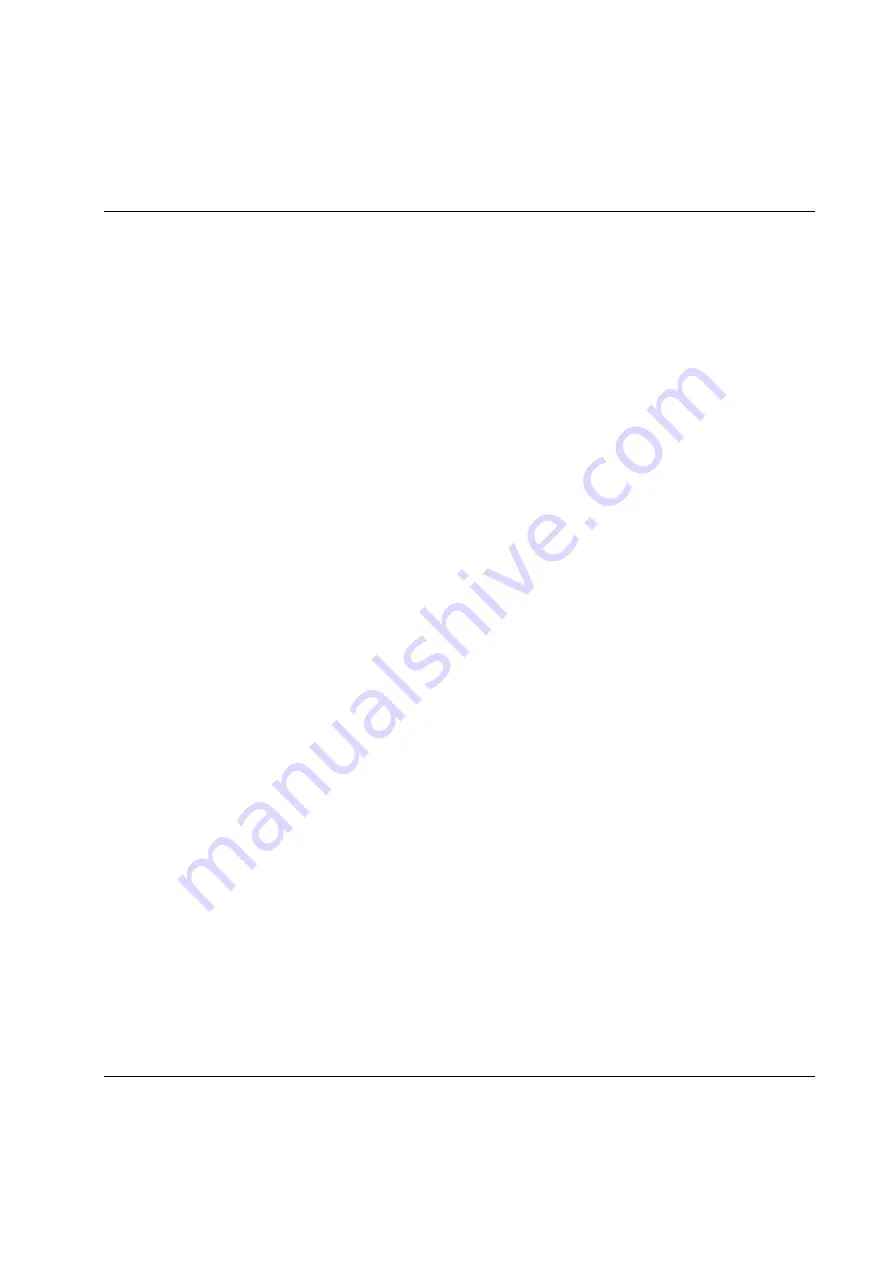
PLC
246
9836 3521 01
BOLTCTRL2_BOLTSEL[3] = 0
BOLTCTRL2_BOLTSEL[4] = 0
Then order the station to remove the last result stored for the selected bolts by changing
BOLTCTRL2_CMD from 0 to 1.
Wait for BOLTCTRL2_STS to become 0 (idle OK). This indicates that the station has completed
the drop command.
4. To loose and retighten only the failing bolts the OK bolts must be inhibited. Therefore set up
BOLTCONTROL as below:
BOLTCONTROL[1] = 0 (* Connected normally *)
BOLTCONTROL[2] = 0 (* Connected normally *)
BOLTCONTROL[3] = 3 (* Do not run *)
BOLTCONTROL[4] = 3 (* Do not run *)
5. Loose the bolts by setting MODE to 2 and start the cycle. Wait for the cycle to be completed.
6. Remove the result of the loosening cycle by repeating step 3 above.
7. Retighten bolt "B1" and "B2" again using MODE 1 and starting the cycle. Wait for the cycle to be
completed.
8. Given that the complete tightening now is considered done, either since the retightening of bolt
"B1" and "B2" ended OK, or that no more attempts are allowed, releases the produced cycle data
by setting DATAHOLD to FALSE.
The cycle data produced using the above sequence will the be:
Time: 2005-07-08 13:00:00
Status: OK
Bolt: B3 Program: Tighten Status: OK
Bolt: B4 Program: Tighten Status: OK
Bolt: B1 Program: Tighten Status: OK
(the result from the retightening)
Bolt: B2 Program: Tighten Status: OK
(the result from the retightening)
while the same operations without using the BOLTCTRL2 bolt data drop function would be:
Time: 2003-07-08 13:00:00
Status: NOK
Bolt: B1 Program: Tighten Status: NOK
(the result from the first tightening)
Bolt: B2 Program: Tighten Status: NOK
(the result from the first tightening)
Bolt: B3 Program: Tighten Status: OK
Bolt: B4 Program: Tighten Status: OK
Bolt: B1 Program: Loosen Status: OK
(the result from the loosening)
Bolt: B2 Program: Loosen Status: OK
(the result from the loosening)
Bolt: B1 Program: Tighten Status: OK
(the result from the retightening)
Bolt: B2 Program: Tighten Status: OK
(the result from the retightening)
Содержание PowerMACS 4000
Страница 1: ...User guide PowerMACS 4000 Atlas Copco Tools and Assembly Systems 9836 3521 01 2010 11 Edition 10 3 0...
Страница 2: ......
Страница 46: ...System Architecture 46 9836 3521 01...
Страница 127: ...Set Up and Maintenance 9836 3521 01 127 See chapter Station Set Up for a description of the parameters...
Страница 267: ...Tightening 9836 3521 01 267...
Страница 400: ...Tightening 400 9836 3521 01...
Страница 422: ...Peripheral Devices 422 9836 3521 01 When connected to a system the form will show show the signal values in realtime...
Страница 486: ...Peripheral Devices 486 9836 3521 01...
Страница 622: ...Peripheral Devices 622 9836 3521 01...
Страница 664: ...References 664 9836 3521 01...
Страница 668: ...9836 3521 01 2010 11 Edition 10 3 0 www atlascopco com...