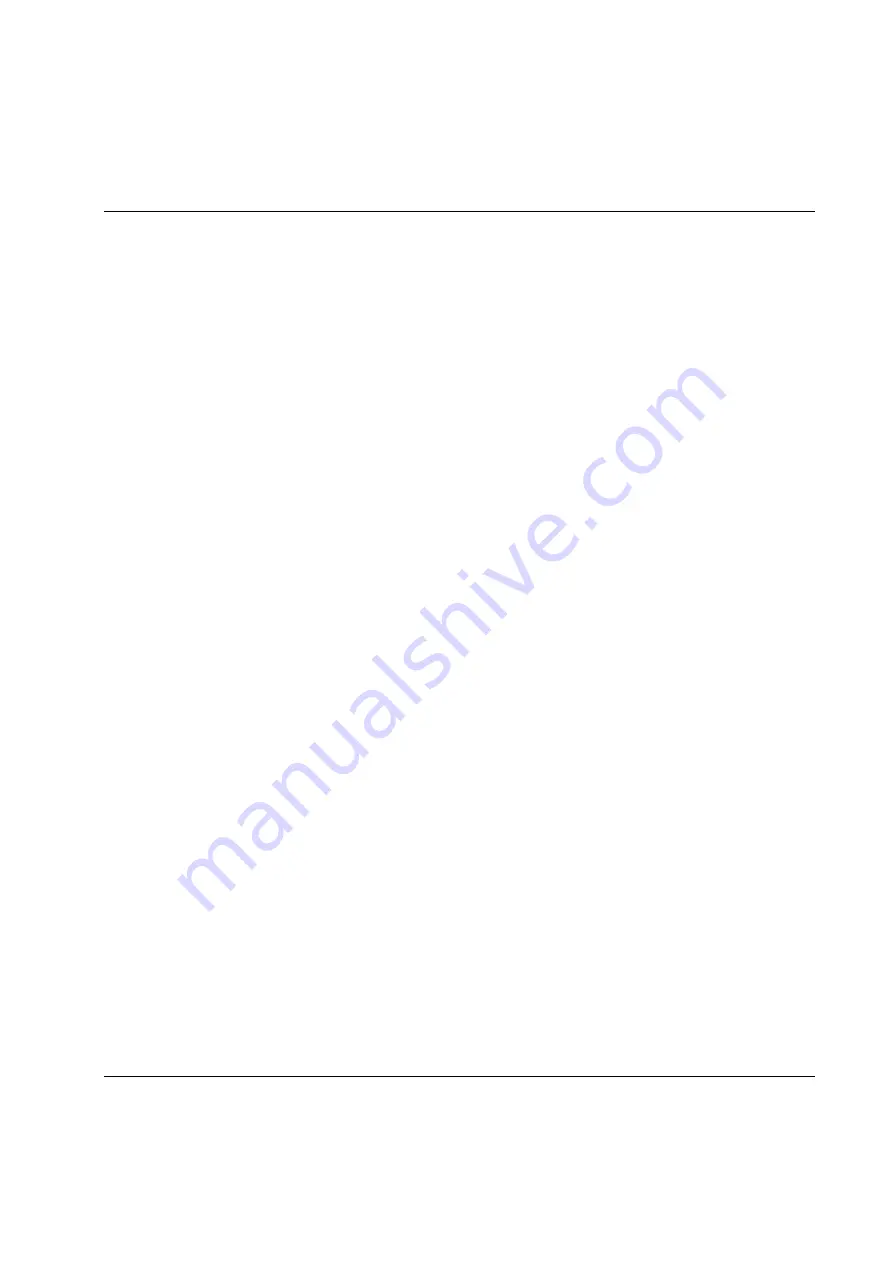
Tightening
366
9836 3521 01
Hold torque
. This alternative does not stop any ongoing motion. The servo will maintain the torque
it has when the step is stopped. Note! This means that if there is not contradicting force the spindle
will continue to run. This stop condition is used for step types DT - Run until Dyna-Tork
, method 2, and DT3 - Run until Dyna-Tork
Continue rotation
(only available for Gauging)
With this stop condition the spindle will not stop between steps, but instead continue to rotate.
During the time between the steps the restrictions
Torque, Remove fastener torque limit
and
Transducer Protection
will still be active. The same limits as in the step before will be used.
There will also be a time restriction of 60 seconds for the continue rotation. If any of the limits are
exceeded the spindle will be stopped directly and the fatal error
CROT
will be set, together with
error-code for the error that stopped the spindle.
Failing Step No
will be set to the step before and
the reject settings in this step will be used.
When the next step starts the speed will be ramped to the target speed of that step with the ramp
programmed in this step. If the next step has a different direction compared to the previous step
the direction change will be made with a speed ramp. An event will also be generated to warn the
user that this has happened.
If the evaluation of any checks fails for a spindle that run
Continue rotation
the motor will be
switched off and the spindle will roll out to a stop. The same will also happen if another spindle fails
and starts to run reject management. However, if
Allow hold torque also during RM
is checked
in the Station Set Up the spindle will continue to rotate in both these cases.
6.5.6.3 Ramps & Other
– Store Position (only available for Gauging)
It is possible to store the current position at the end of each step and later return to this position with the
step
Run to Position
.
Set Null position
is a
combo box with following choices:
Keep old value
(default): The null position is not changed
Half pos
: The null position is set to the position half way through the step.
Full pos
: The null position is set to the current position at the end of the step (after the over shoot
time has passed)
Set Half position
is a checkbox. If checked the half position will be set to the position half way through
the step, otherwise the half position will not be changed. Default value is not checked.
Half position is defined as half the angle from step start (after backlash is done) to step stop (the angle
there the braking of the spindle begins).
In
Program Settings-Settings
there is a checkbox
Reset Position
. If checked all four position registers
(Null, Half, Peak and Low) will be cleared at cycle start, otherwise the positions stored in a previous cycle
will be kept.
Any movement between the programs will be measured and the distance to the position registers will be
updated accordingly.
Содержание PowerMACS 4000
Страница 1: ...User guide PowerMACS 4000 Atlas Copco Tools and Assembly Systems 9836 3521 01 2010 11 Edition 10 3 0...
Страница 2: ......
Страница 46: ...System Architecture 46 9836 3521 01...
Страница 127: ...Set Up and Maintenance 9836 3521 01 127 See chapter Station Set Up for a description of the parameters...
Страница 267: ...Tightening 9836 3521 01 267...
Страница 400: ...Tightening 400 9836 3521 01...
Страница 422: ...Peripheral Devices 422 9836 3521 01 When connected to a system the form will show show the signal values in realtime...
Страница 486: ...Peripheral Devices 486 9836 3521 01...
Страница 622: ...Peripheral Devices 622 9836 3521 01...
Страница 664: ...References 664 9836 3521 01...
Страница 668: ...9836 3521 01 2010 11 Edition 10 3 0 www atlascopco com...