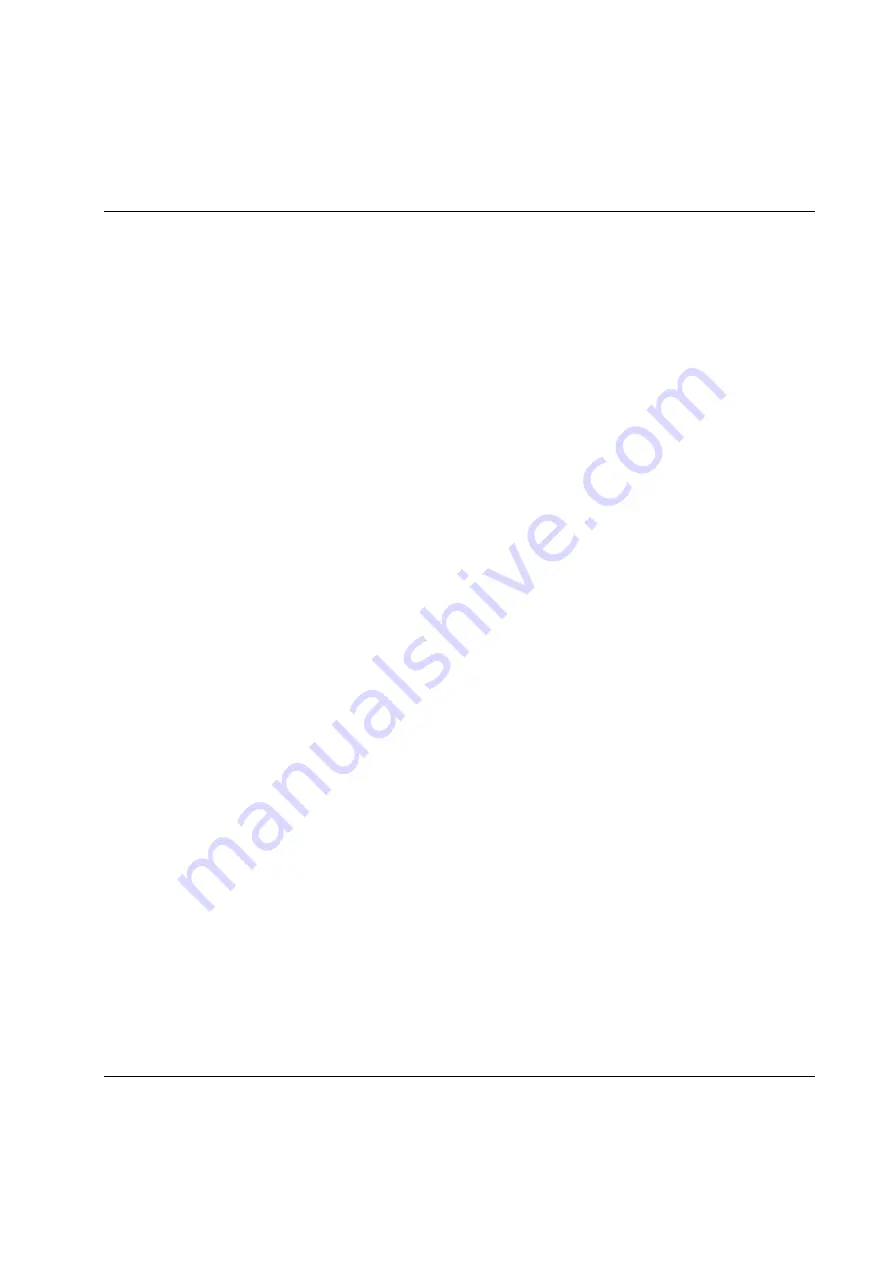
Tightening
322
9836 3521 01
level are named
Bolt var. 01
,
Bolt var. 02
, etc. The first 40 variables of each type are marked with a
T
, to
indicate that these are scaled according to the torque unit selection in the reporters.
It is also possible to select
Not reported
, which mean that no value will be reported for the check.
Checks that run in a zone, i.e. have
Operate on
set to
Zone
, can not use the
Specialized variable
for
reporting, only the
Step var
and
Bolt var
are avaliable.
Note:
It is only possible to use the same variable once in each step. For example, with two Peak Torque
checks on the same step with channel selection Torque 1, only one can use the specialized variable Peak
T1, the other one must use one of the general variables (or not reported). Setup problems will detect any
errors and generate warnings if needed.
6.5.4.2 Check peak torque
Parameters:
TH
(Torque high),
TL
(Torque low),
Set null position
(Store peak position to Null position register) (only available for Gauging)
Set peak position
(Store peak position to Peak position register) (only available for
Gauging)
Function:
The peak torque from check start to check stop is checked to be between the high limit
TH
and the low limit
TL
.
Both limits are optional. Leaving them blank disables the check but the result value is still
calculated and reported.
If the check operates on step it starts at step start. It ends when the step ends, including
overshoot time. If the check operates on zone the check starts when the selected zone
starts and ends when the zone ends.
If
Set null position
or
Set peak position
is set the peak position, that is the angle where
the peak torque was found, is stored in the corresponding position register. It is possible to
return to this position later with the step
to Position (only available for Gauging).
This check requires that at least one sample is collected after the torque spike elimination
phase. If not, and at least one limit is specified, the steps status is set to
Fatal
and the error
bit of the respective limit is set.
Содержание PowerMACS 4000
Страница 1: ...User guide PowerMACS 4000 Atlas Copco Tools and Assembly Systems 9836 3521 01 2010 11 Edition 10 3 0...
Страница 2: ......
Страница 46: ...System Architecture 46 9836 3521 01...
Страница 127: ...Set Up and Maintenance 9836 3521 01 127 See chapter Station Set Up for a description of the parameters...
Страница 267: ...Tightening 9836 3521 01 267...
Страница 400: ...Tightening 400 9836 3521 01...
Страница 422: ...Peripheral Devices 422 9836 3521 01 When connected to a system the form will show show the signal values in realtime...
Страница 486: ...Peripheral Devices 486 9836 3521 01...
Страница 622: ...Peripheral Devices 622 9836 3521 01...
Страница 664: ...References 664 9836 3521 01...
Страница 668: ...9836 3521 01 2010 11 Edition 10 3 0 www atlascopco com...