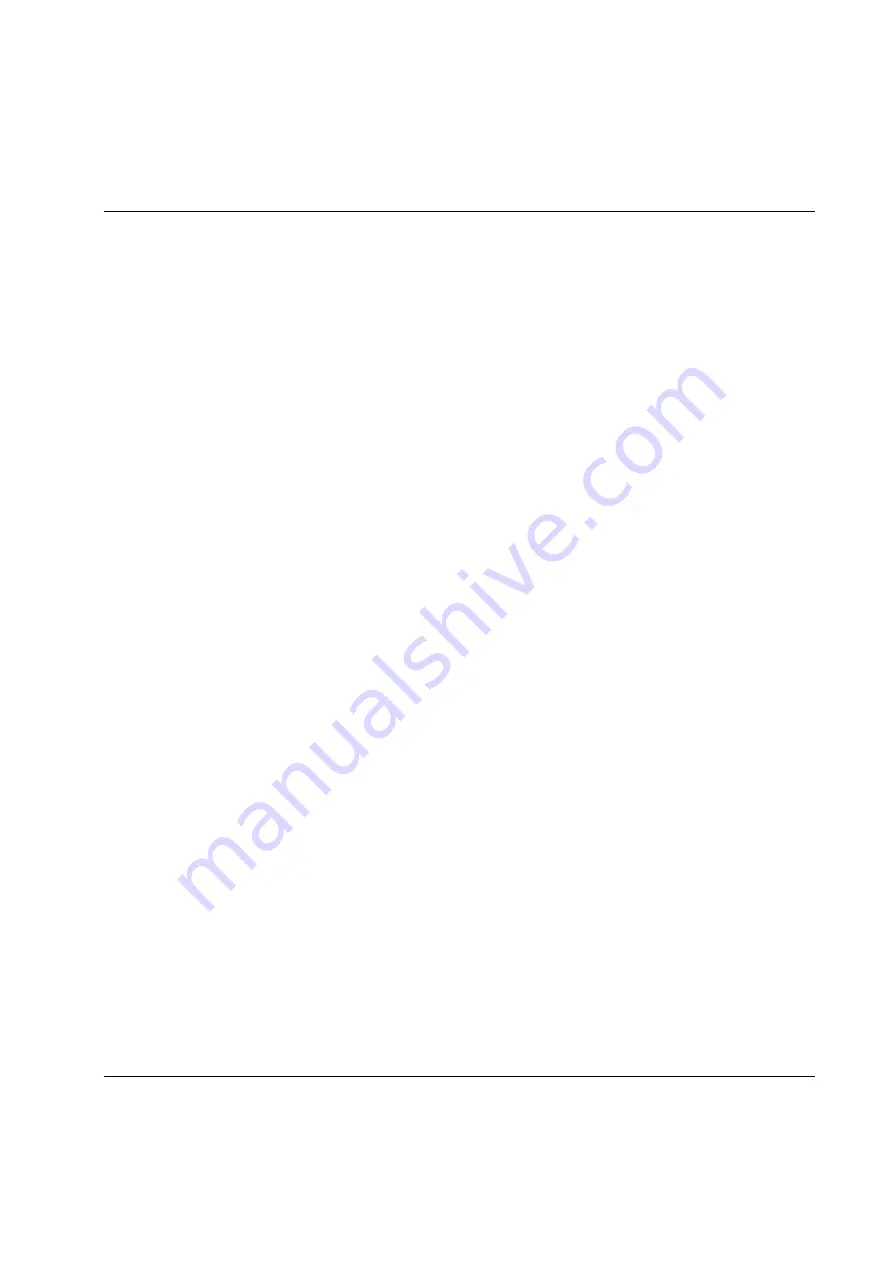
Tightening
370
9836 3521 01
The monitoring function can be started and stopped at any point during the cycle. When to start and stop
monitoring is configured for each program. The following alternatives are available as start conditions:
At cycle start (default)
When a specific step is started
When torque reaches a specified level
The following stop conditions are available:
At cycle end (default)
When torque reaches a specified level
Monitoring is performed when a CE-step is reached and the station orders the bolt to do monitoring. If the
CE-step has RM defined the cycle might continue after the first monitoring. If so, monitoring is waiting for a
new start. The only way to start monitoring after the first CE is to run a step with the
Start/restart
monitoring
parameter checked (see Step
– Control). When such a step is started monitoring is reset and
started. The next time a CE-step is reached monitoring is performed as specified in that step.
Monitoring evaluation is always performed as specified in the different monitoring checks. Should
monitoring not have been restarted and the bolt has terminated the monitoring reevaluates the checks
using the same measurement values as last evaluation. Thus the reported results will remain and events
will be generated if any errors are found. Check
Ignore monitoring errors when step ends NOK
if
events and error bits are not wanted during monitoring evaluation after Terminate.
If monitoring was never started or restarted and any step was started (and the bolt is not terminated) the
evaluation is done on reset monitoring measurement values, which causes Fatal errors for all checks that
have configured limits.
Monitoring can also be stopped when a step fails. To enable this check the
Stop monitoring when step
ends NOK
check box on The Tightening Program form, see chapter; : Program Settings. This, together
with the use of the Start/restart monitoring parameter for the steps (see Step
– Control) can be useful if
you want to report the result from the failing tightening.
Normally the first torque and angle transducers are recorded on the first monitoring buffer and the
secondary transducers recorded on the second monitoring buffer. If there is only one channel available it
is used for both buffers.
Example:
The spindle set up contains two enabled torque channels and one enabled angle channel the
second monitoring buffer will use torque channel two and angle channel one.
When monitoring is running and the bolt is run in its forward direction, the maximum torque value
measured in each angle interval will be stored in the corresponding buffer position.
When the bolt is run in its backward direction (and monitoring is running), the buffer is backed to the
position that corresponds to minimum angle reached during the step. The buffer adjustment is done when
the next step or monitoring evaluation starts. All values that correspond to the backed distance are
erased. Should you pass the point (that is, angle) where monitoring was started, the monitoring buffer will
be restarted the next time the bolt is run in its forward direction. This means that you cannot measure a
negative angle using the monitoring buffer. (Should you need to measure a negative cycle angle there is
Содержание PowerMACS 4000
Страница 1: ...User guide PowerMACS 4000 Atlas Copco Tools and Assembly Systems 9836 3521 01 2010 11 Edition 10 3 0...
Страница 2: ......
Страница 46: ...System Architecture 46 9836 3521 01...
Страница 127: ...Set Up and Maintenance 9836 3521 01 127 See chapter Station Set Up for a description of the parameters...
Страница 267: ...Tightening 9836 3521 01 267...
Страница 400: ...Tightening 400 9836 3521 01...
Страница 422: ...Peripheral Devices 422 9836 3521 01 When connected to a system the form will show show the signal values in realtime...
Страница 486: ...Peripheral Devices 486 9836 3521 01...
Страница 622: ...Peripheral Devices 622 9836 3521 01...
Страница 664: ...References 664 9836 3521 01...
Страница 668: ...9836 3521 01 2010 11 Edition 10 3 0 www atlascopco com...