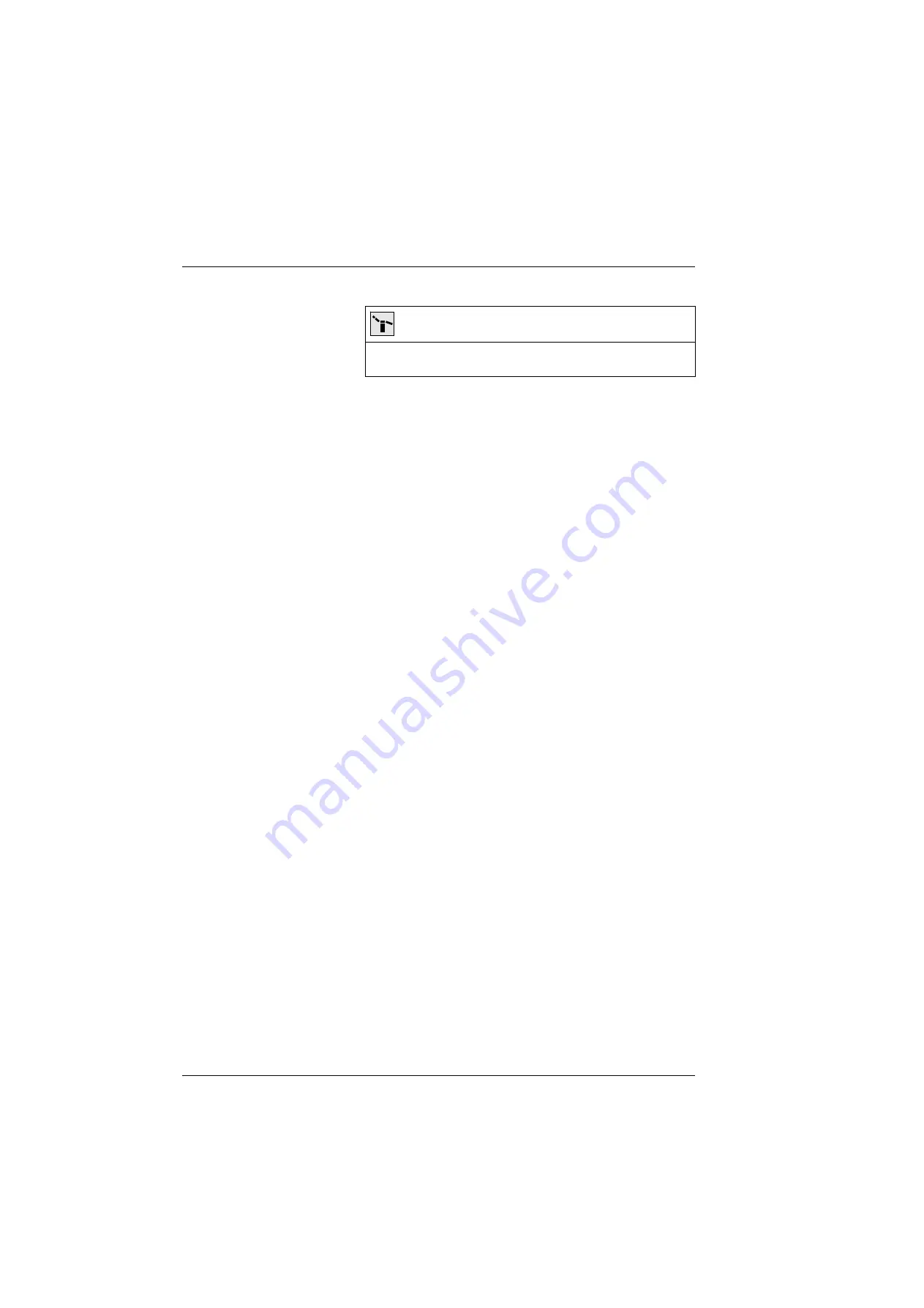
Cable W155
246
Service Manual TruSystem 7000 Operating Table – 1 764 986 – 10/2016
13. Put on the pad.
TEST
Perform recheck according to IEC 60601-1; perform function test
and final check.
Summary of Contents for TruSystem 7000
Page 1: ...TruSystem 7000 Operating Table Service Manual...
Page 4: ...Service Manual TruSystem 7000 Operating Table 1 764 986 10 2016...
Page 10: ...Contents 10 Service Manual TruSystem 7000 Operating Table 1 764 986 10 2016...
Page 297: ...Circuit Diagram Service Manual TruSystem 7000 Operating Table 1 764 986 10 2016 297...
Page 298: ...Circuit Diagram 298 Service Manual TruSystem 7000 Operating Table 1 764 986 10 2016...
Page 300: ...Hydraulics Diagram 300 Service Manual TruSystem 7000 Operating Table 1 764 986 10 2016...
Page 302: ...Hydraulic Jack Unit 302 Service Manual TruSystem 7000 Operating Table 1 764 986 10 2016...
Page 304: ...Service Information 304 Service Manual TruSystem 7000 Operating Table 1 764 986 10 2016...
Page 305: ......