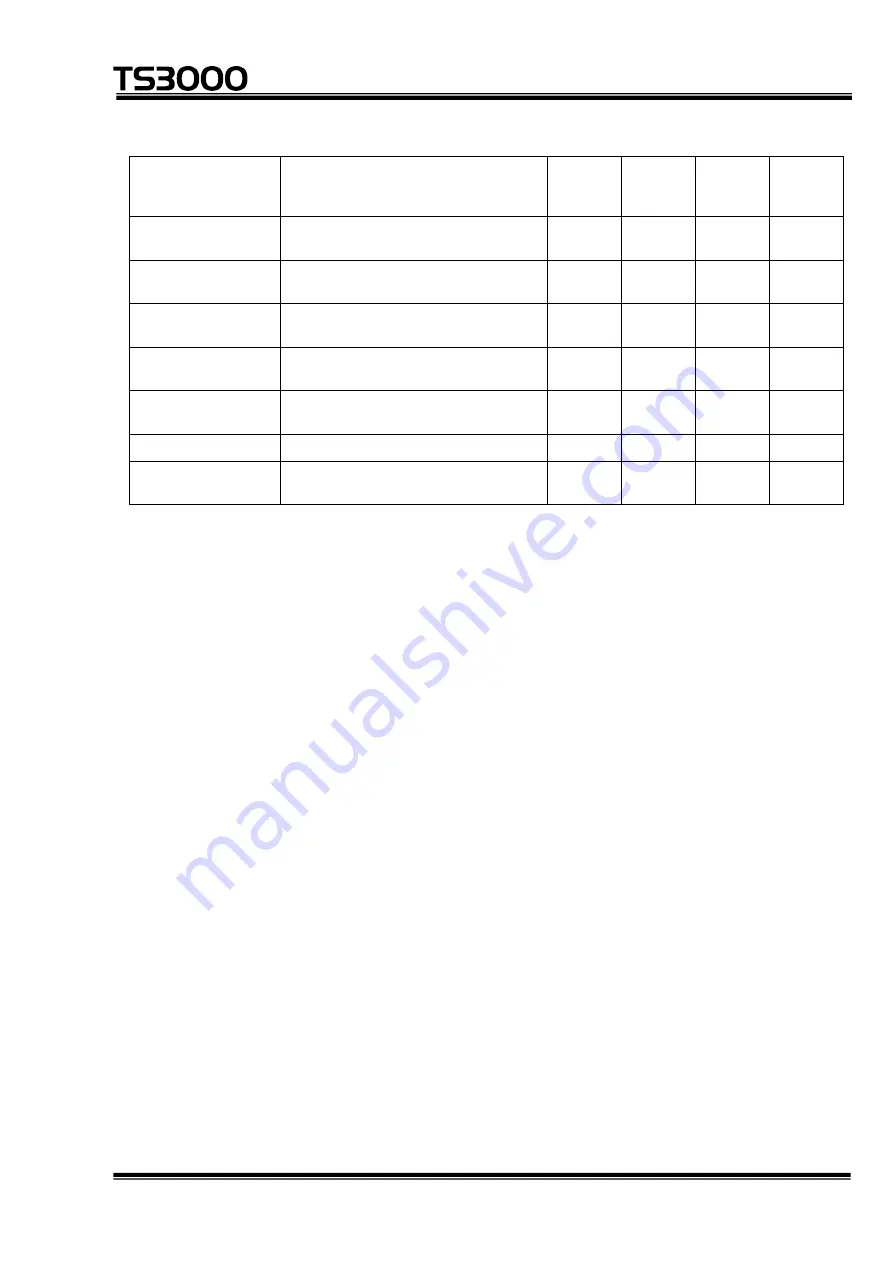
STE 85412
– 1-2 –
TP3000 OPERATOR’S MANUAL
series Robot Controller
Function
Descriptions
Control
panel
Teach
pendant
External
control
signal
HOST
commu-
nication
Work coordinate
system selection
Used to select the work coordinate
system.
Tool coordinate
system selection
Used to select the tool coordinate
system.
Present position
monitor
Used to display the present position of
the robot in each coordinate system.
External I/O signal
monitor
Used to display the status of digital I/O
signals.
Working time
monitor
Used to display turn-on time of power
supply and operation time.
File selection
Used to select a file to be executed.
Movement
Used to move the robot to a taught
point.
* The TSL3000 neither has a control panel nor the internal automatic operation
function.
: Operation is possible.
:
Operation is partly possible.