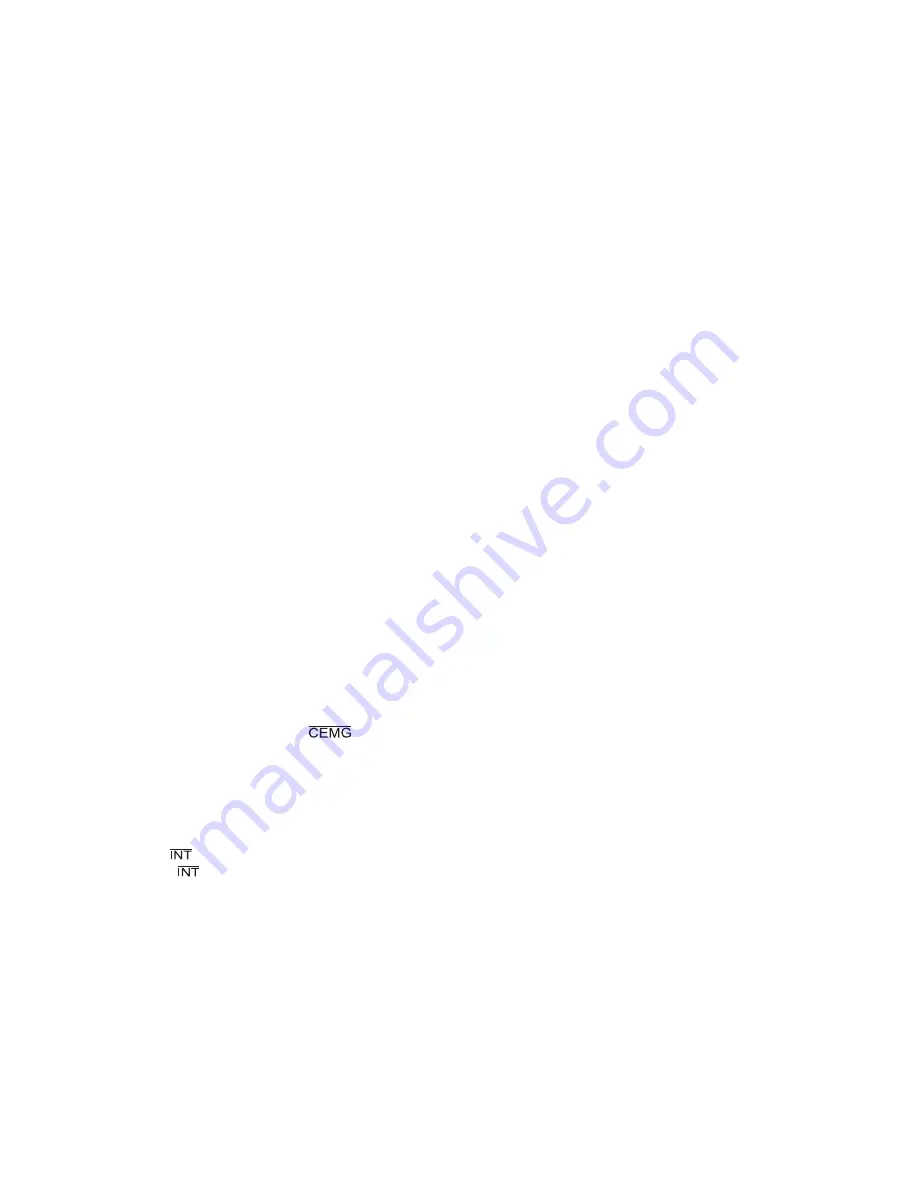
-
3
-
EZ
signal
is
received.
♦
Mechanical
input
signals
The
following
four
signals
can
be
input
for
each
axis.
1)
+EL:
When
this
signal
is
turned
ON,
while
feeding
in
the
positive
(+)
direction,
movement
on
this
axis
stops
immediately
(with
deceleration).
When
this
signal
is
ON,
no
further
movement
occurs
on
the
axis
in
the
positive
(+)
direction.
(The
motor
can
be
rotated
in
the
negative
(-)
direction.)
2)
-EL:
Functions
the
same
as
the
+EL
signal
except
that
it
works
in
the
negative
(-)
direction.
3)
SD:
This
signal
can
be
used
as
a
deceleration
signal
or
a
deceleration
stop
signal,
according
to
the
software
setting.
When
this
is
used
as
a
deceleration
signal,
and
when
this
signal
is
turned
ON
during
a
high
speed
feed
operation,
the
motor
on
this
axis
will
decelerate
to
the
FL
speed.
If
this
signal
is
ON
and
movement
on
the
axis
is
started,
the
motor
on
this
axis
will
run
at
the
FL
low
speed.
When
this
signal
is
used
as
a
deceleration
stop
signal,
and
when
this
signal
is
turned
ON
during
a
high
speed
feed
operation,
the
motor
on
this
axis
will
decelerate
to
the
FL
speed
and
then
stop.
4)
ORG:
Input
signal
for
a
zero
return
operation.
For
safety,
make
sure
the
+EL
and
-EL
signals
stay
on
from
the
EL
position
until
the
end
of
each
stroke.
The
input
logic
for
these
signals
can
be
changed
using
the
ELL
terminal.
The
input
logic
of
the
SD
and
ORG
signals
can
be
changed
using
software.
♦
Servomotor
I/F
The
following
three
signals
can
be
used
as
an
interface
for
each
axis.
1)
INP:
Input
positioning
complete
signal
that
is
output
by
a
servomotor
driver.
2)
ERC:
Output
deflection
counter
clear
signal
to
a
servomotor
driver.
3)
ALM:
Regardless
of
the
direction
of
operation,
when
this
signal
is
ON,
movement
on
this
axis
stops
immediately
(deceleration
stop).
When
this
signal
is
ON,
no
movement
can
occur
on
this
axis.
While
the
PCL
is
operating
in
the
timer
mode,
it
cannot
be
stopped
using
the
ALM
input.
Even
though
the
PCL
is
stopped,
it
will
output
an
INT
(interrupt
request)
when
an
ALM
signal
is
received.
The
input
logic
of
the
INP,
ERC,
and
ALM
signals
can
be
changed
using
software.
The
ERC
signal
is
a
pulsed
output.
The
pulse
length
can
be
set.
(12
µsec
to
104
msec.
A
level
output
is
also
available.)
♦
Output
pulse
specifications
Output
pulses
can
be
set
to
a
common
pulse,
2-pulse
mode
or
90
o
phase
difference
mode.
The
output
logic
can
also
be
selected.
♦
Emergency
stop
signal
(
)
input
When
this
signal
is
turned
ON,
movement
on
all
axes
stops
immediately.
While
this
signal
is
ON,
no
movement
is
allowed
on
either
axes.
This
input
cannot
be
disabled.
The
PCL
will
stop
when
this
signal
is
present,
even
it
is
in
the
timer
mode.
♦
Interrupt
signal
output
An
signal
(interrupt
request)
can
be
output
for
many
reasons.
The
terminal
output
signal
can
use
ORed
logic
for
lots
of
conditions
on
each
axis.
(When
more
than
one
LSI
is
used,
wired
OR
connections
are
not
possible.)
Summary of Contents for PCL6113
Page 1: ...User s Manual For PCL6113 6123 6143 Pulse Control LSI Nippon Pulse Motor Co Ltd...
Page 11: ...5 3 Terminal Assignment Diagram 3 1 PCL6113 3 2 PCL6123...
Page 20: ...14 5 Block Diagram...
Page 115: ...109 11 Stop timing by error...
Page 116: ...110 13 External Dimensions 13 1 PCL6113...
Page 117: ...111 13 2 PCL6123...
Page 118: ...112 13 3 PCL6143...