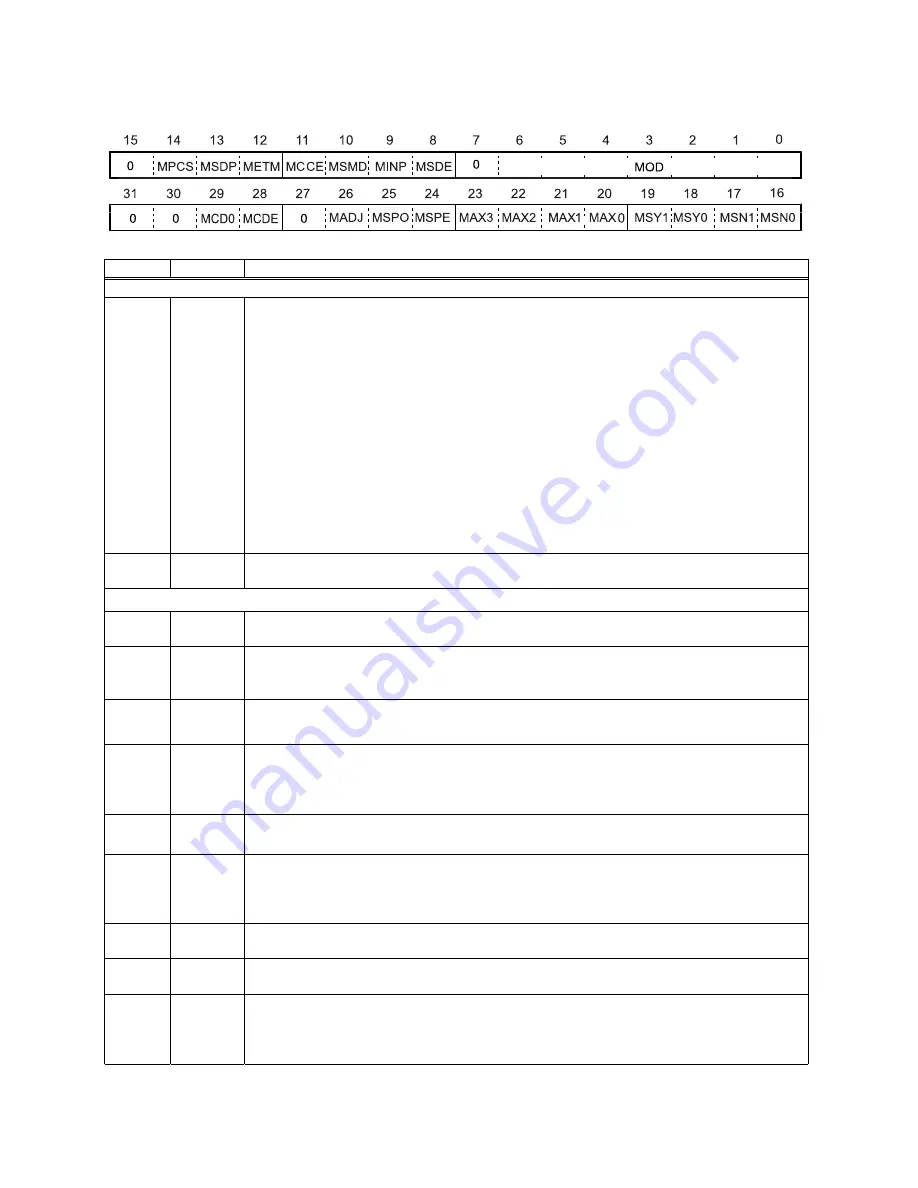
-
36
-
8-3-8.
PRMD
(RMD)
registers
These
pre-registers
are
used
to
set
the
operation
mode.
RMD
is
the
register
for
PRMD.
Bits
Bit
name
Description
Setting
basic
operation
mode
0
to
6
MOD
Set
operation
mode.
000
0000
(00h):
Continuous
positive
rotation
controlled
by
command
control.
000
1000
(08h):
Continuous
negative
rotation
controlled
by
command
control.
000
0001
(01h):
Continuous
operation
controlled
by
pulsar
(PA/PB)
input.
000
0010
(02h):
Continuous
operation
controlled
by
external
signal
(+DR/-DR)
input.
001
0000
(10h):
Positive
rotation
zero
return
operation.
001
1000
(18h):
Negative
rotation
zero
return
operation.
100
0001
(41h):
Positioning
operation
(specify
the
incremental
target
position)
100
0111
(47h):
Timer
operation
101
0001
(51h):
Positioning
operation
controlled
by
pulsar
(PA/PB)
input.
101
0110
(56h):
Positioning
operation
controlled
by
external
signal
(+DR/-DR)
input.
110
0010
(62h):
Continuous
linear
interpolation
110
0011
(63h):
Linear
interpolation
7
Not
defined
(Always
set
0)
Optical
setting
items
8
MSDE
0:
SD
input
will
be
ignored.
(Checking
can
be
done
with
RSTS
in
sub
status)
1:
Decelerates
(deceleration
stop)
by
turning
ON
the
input.
9
MINP
0:
Delay
using
an
INP
input
will
be
possible.
(Checking
can
be
done
with
RSTS
in
sub
status)
1:
Completes
operation
by
turning
ON
the
INP
input.
10
MSMD Specify
an
acceleration/deceleration
type
for
high
speed
feed.
(0:
Linear
accel/decel.
1:
S-curve
accel/decel.)
11
MCCE
1:
Stop
counting
output
pulses
on
COUNTER1
and
2.
This
is
used
to
move
a
mechanical
part
without
changing
the
PLC
control
position
When
the
counter
input
selection
(RENV3:
CIS1,
CIS2)
is
set
to
EA/EB,
the
PCL
will
not
stop
counting
when
this
bit
is
set.
12
METM
Specify
the
operation
complete
timing.
(0:
End
of
cycle.
1:
End
of
pulse.)
When
selecting
continuous
operation
using
the
pre-register,
select
"end
of
cycle."
13
MSDP
Specify
the
ramping-down
point
for
high
speed
feed.
(0:
Automatic
setting.
1:
Manual
setting.)
Effective
for
positioning
operations
and
linear
interpolation
feeding.
When
automatic
setting
is
selected,
set
PRUR
=
PRDR
and
PRUS
=
PRDS.
14
MPCS
1:
While
in
automatic
operation,
control
the
number
of
pulses
after
the
PCS
input
is
turned
ON.
(Override
2
for
the
target
position.)
15
Not
defined
(Always
set
0)
16
to
17 MSN0
to
1
When
you
want
to
control
an
operation
block,
specify
a
sequence
number
using
2
bits.
By
reading
the
main
status
(MSTSW),
a
sequence
number
currently
being
executed
(SSC0
to
1)
can
be
checked.
Setting
the
sequence
number
does
not
affect
the
operation.
Summary of Contents for PCL6113
Page 1: ...User s Manual For PCL6113 6123 6143 Pulse Control LSI Nippon Pulse Motor Co Ltd...
Page 11: ...5 3 Terminal Assignment Diagram 3 1 PCL6113 3 2 PCL6123...
Page 20: ...14 5 Block Diagram...
Page 115: ...109 11 Stop timing by error...
Page 116: ...110 13 External Dimensions 13 1 PCL6113...
Page 117: ...111 13 2 PCL6123...
Page 118: ...112 13 3 PCL6143...