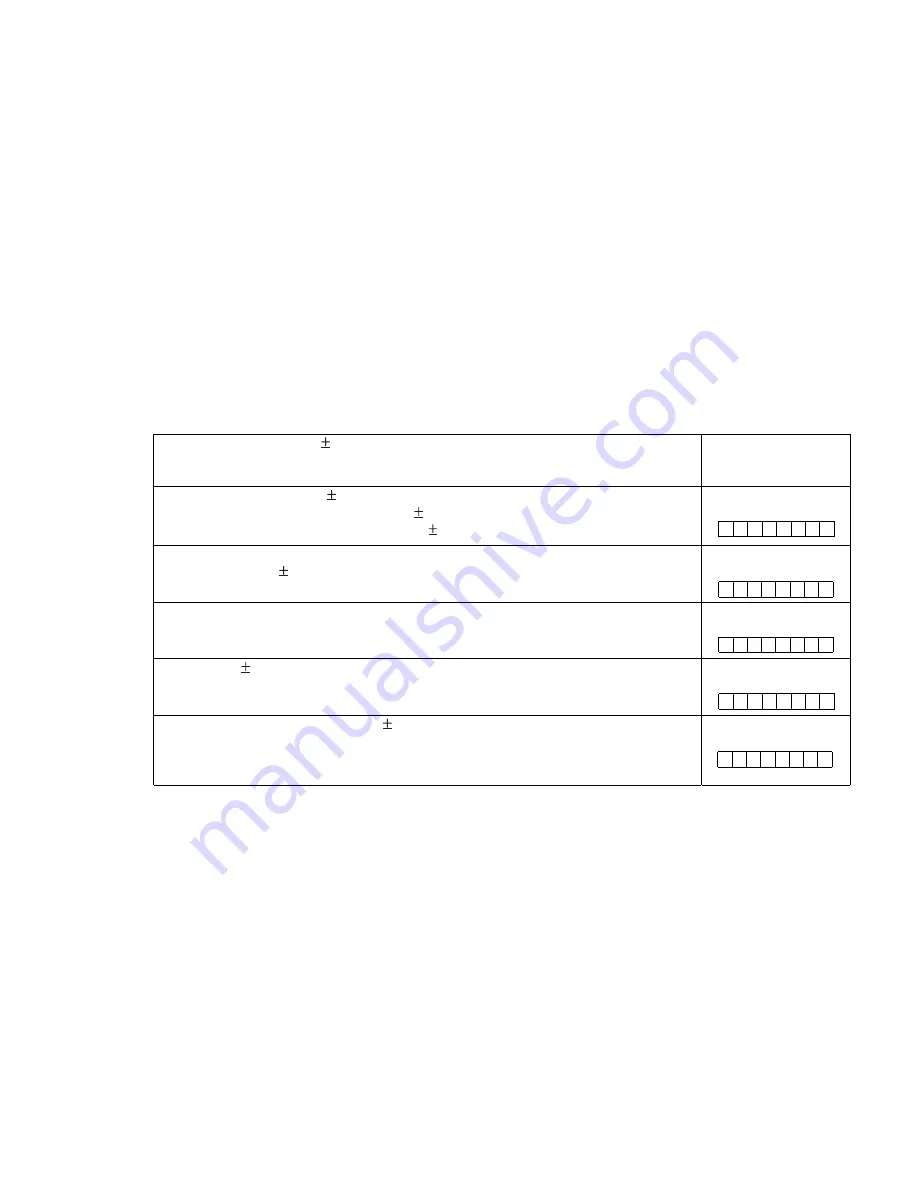
-
77
-
11-4.
Mechanical
external
input
control
11-4-1.
+EL,
-EL
signal
When
an
end
limit
signal
(a
+EL
signal
when
feeding
in
the
+
direction)
in
the
feed
direction
turns
ON
while
operating,
the
axis
will
stop
immediately
or
decelerate
and
stop.
After
stopping,
even
if
the
EL
signal
is
turned
OFF,
the
axis
will
remain
stopped.
For
safety,
keep
the
EL
signal
ON
until
the
axis
reaches
the
end
of
the
stroke.
If
the
EL
signal
is
ON
when
writing
a
start
command,
the
axis
cannot
start
moving
in
the
direction
of
the
particular
EL
signal
that
is
ON.
By
setting
ELM
in
the
RENV1
(environment
setting
1)
register,
the
stopping
pattern
for
use
when
the
EL
signal
is
turned
ON
can
be
set
to
immediate
stop
or
deceleration
stop
(high
speed
start
only).
The
minimum
pulse
width
of
the
EL
signal
is
2
cycles
of
reference
clock
cycles
(0.4
µ
s)
when
the
input
filter
is
OFF.
When
the
input
filter
is
OFF
the
minimum
pulse
time
for
the
EL
signal
is
two
reference
clock
cycles
(0.1
µ
s).
When
the
input
filter
is
ON,
the
PCL
will
not
respond
to
pulse
signals
shorter
than
the
specified
time.
By
reading
the
SSTSW
(sub
status),
you
can
monitor
the
EL
signal.
By
reading
the
REST
register,
you
can
check
for
an
error
interrupt
caused
by
the
EL
signal
turning
ON.
When
in
the
timer
mode,
this
signal
is
ignored.
Even
in
this
case,
the
EL
signal
can
be
monitored
by
reading
SSTSW
(sub
status).
The
input
logic
of
the
EL
signal
can
be
set
for
each
axis
using
the
ELL
input
terminal.
Set
the
input
logic
of
the
EL
signal
<ELL
input
terminal>
L:
Positive
logic
input
H:
Negative
logic
input
Stop
method
to
when
the
EL
signal
turns
ON
<Set
ELM
(bit
3)
in
RENV1>
0:
Immediate
stop
by
turning
ON
the
EL
signal
1:
Deceleration
stop
by
turning
ON
the
EL
signal
[RENV1]
(WRITE)
7
0
-
-
-
-
n
-
-
-
Setting
the
±EL
input
filter
<Set
FLTR
(bit
26)
in
RENV1>
1:
Inset
filters
to
EL,
SD,
ORG,
ALM,
and
INP
inputs.
When
the
filter
is
inserted,
pulses
shorter
than
the
FTM
set
value
are
ignored.
[RENV1]
(WRITE)
31
24
-
-
-
-
-
n
-
-
Select
the
input
filter
characteristics
<Set
FTM
(bits
20,
21)
in
RENV1>
00:
3.2
µ
s
10:
200
µ
s
01:
25
µ
s
11:
1.6
ms
[RENV1]
(WRITE)
23
16
-
-
n
n
-
-
-
-
Reading
the
EL
signal
<SPEL
(bit
12),
SMEL
(bit
13)
in
SSTSW>
SPEL
=
0:Turn
OFF
the
+EL
signal
SPEL
=
1:
Turn
ON
the
+EL
signal
SMEL
=
0:Turn
OFF
the
-EL
signal
SMEL
=
1:
Turn
ON
the
-EL
signal
[SSTSW]
(READ)
15
8
-
-
n
n
-
-
-
-
Reading
the
stop
cause
when
the
EL
signal
turns
on
<ESPL
(bit
0),
ESML
(bit
1)
in
REST>
ESPL
=
1:
Stop
by
turning
ON
the
+EL
signal
ESML
=
1:
Stop
by
turning
ON
the
-EL
signal
[REST]
(READ)
7
0
-
-
-
-
-
-
n
n
11-4-2.
SD
signal
If
the
SD
signal
input
is
disabled
by
setting
MSDE
in
the
PRMD
register
(operation
mode),
the
SD
signal
will
be
ignored.
If
the
SD
signal
is
enabled
and
the
SD
signal
is
turned
ON
while
in
operation,
the
axis
will:
1)
decelerate,
2)
latch
and
decelerate,
3)
decelerate
and
stop,
or
4)
latch
and
perform
a
deceleration
stop,
according
to
the
setting
of
SDM
and
SDLT
in
the
RENV1
register
(environment
setting
1).
1)
Deceleration
<
SDM
(bit
4)
=
0,
SDLT
(bit
5)
=
0
in
RENV1
register>
-While
feeding
at
low
speed,
the
SD
signal
is
ignored.
While
in
high
speed
operation
the
axis
decelerates
to
the
FL
speed
when
the
SD
signal
is
turned
ON.
After
decelerating,
or
while
decelerating,
if
the
SD
signal
turns
OFF,
the
axis
will
accelerate
to
the
FH
speed.
-
If
the
SD
signal
is
turned
ON
when
the
high
speed
command
is
written,
the
axis
will
operate
at
FL
speed.
When
the
SD
signal
is
turned
OFF,
the
axis
will
accelerate
to
FH
speed.
Summary of Contents for PCL6113
Page 1: ...User s Manual For PCL6113 6123 6143 Pulse Control LSI Nippon Pulse Motor Co Ltd...
Page 11: ...5 3 Terminal Assignment Diagram 3 1 PCL6113 3 2 PCL6123...
Page 20: ...14 5 Block Diagram...
Page 115: ...109 11 Stop timing by error...
Page 116: ...110 13 External Dimensions 13 1 PCL6113...
Page 117: ...111 13 2 PCL6123...
Page 118: ...112 13 3 PCL6143...