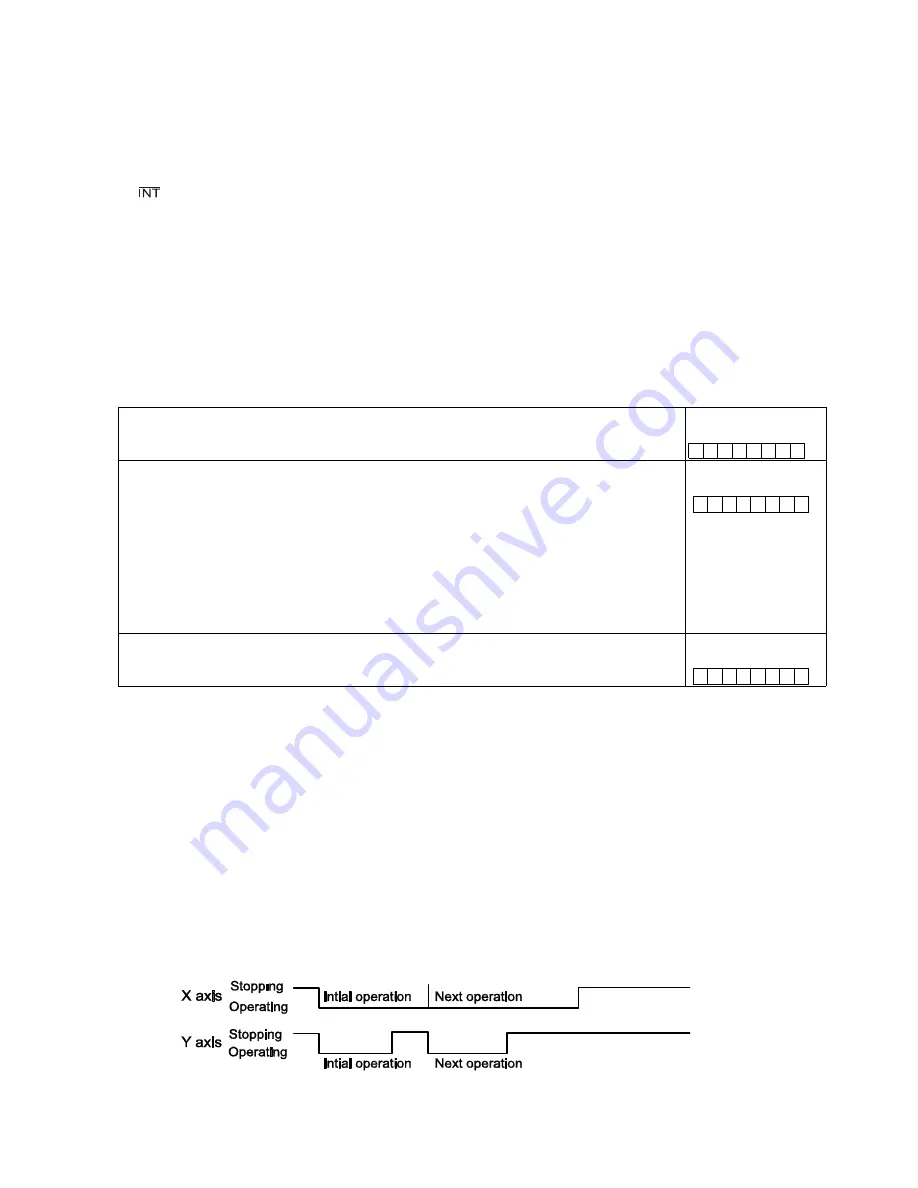
-
94
-
11-11.
Synchronous
starting
This
LSI
can
perform
the
following
operation
by
setting
the
PRMD
(operation
mode)
register
in
advance.
♦
Start
triggered
by
another
axis
stopping.
♦
Start
triggered
by
an
internal
synchronous
signal
from
another
axis.
The
internal
synchronous
signal
output
is
available
with
6
types
of
timing.
They
can
be
selected
by
setting
the
RENV3
(environment
setting
3)
register.
By
setting
the
RIRQ
(event
interrupt
cause)
register,
an
signal
can
be
output
at
the
same
time
the
internal
synchronous
signal
is
output.
You
can
determine
the
cause
of
event
interrupt
by
reading
the
RIST
register.
The
operation
status
can
be
checked
by
reading
the
RSTS
(extension
status)
register.
11-11-1.
Start
triggered
by
another
axis
stopping
If
the
start
condition
is
specified
as
a
"Stop
on
two
or
more
axes,"
when
any
of
the
specified
axes
stops
after
operating,
and
the
other
axes
never
start
(remain
stopped),
the
axis
which
is
supposed
to
start
when
the
conditions
are
met
will
start
operation.
Example
1
below
shows
how
to
specify
a
"stop
on
two
or
more
axes."
In
the
example,
while
the
X
axis
(or
Y
axis)
is
working,
the
Y
(or
X)
axis
remains
stopped.
Then,
the
U
axis
starts
operation
when
triggered
by
the
X
(or
Y)
axis
stopping.
Specify
the
synchronous
starting
method
<Set
MSY0
to
1
(bits
18
&
19)
in
PRMD>
11:
Start
triggered
by
specified
axis
stopping.
[PRMD]
(WRITE)
23
16
-
-
-
-
n
n
-
-
Select
an
axis
for
confirming
a
stop
(setting
example)
<Specify
the
axis
using
MAX0
to
Max3
(bits
20
to
23)
in
PRMD>
0001:
Start
when
the
X
axis
stops
0010:
Start
when
the
Y
axis
stops
0100:
Start
when
the
Z
axis
stops
1000:
Start
when
the
U
axis
stops
0011:
Start
when
both
the
X
and
Y
axes
have
stopped
0101:
Start
when
both
the
X
and
Z
axes
have
stopped
1011:
Start
when
the
X,
Y,
and
U
axes
have
all
stopped
1111:
Start
when
all
of
the
axes
have
stopped
[PRMD]
(WRITE)
23
16
n
n
n
n
-
-
-
-
Read
the
operation
status
<CND
(bits
0
to
3)
in
RSTS>
0100:
Wait
for
another
axis
to
stop.
[RSTS]
(READ)
7
0
-
-
-
-
n
n
n
n
[Example
1]
After
setting
steps
1)
to
3),
start
both
the
X
and
Y
axes.
When
both
the
axes
stop,
the
U
axis
will
start.
1)
Set
MSY0
to
1
(bits
18
to
19)
in
PRMD
for
the
U
axis
to
"11."
(Start
triggered
by
another
axis
stopping)
2)
Set
MAX0
to
3
(bits
20
to
23)
in
PRMD
for
the
U
axis
to
"0011."
(When
the
Y
axis
and
then
the
X
axis
stops)
3)
Write
a
start
command
for
the
U
axis.
Operation
examples
Settings
Operation
mode
for
the
X
axis
in
initial
operation: MSY0
to
1
=
00,
MAX0
to
3
=
0000
Operation
mode
calling
for
the
X
axis
in
the
next
operation: MSY0
to
1
=
11,
MAX0
to
3
=
0011
Operation
mode
for
the
Y
axis
in
initial
operation: MSY0
to
1
=
00,
MAX0
to
3
=
0000
Operation
mode
calling
for
the
Y
axis
in
the
next
operation: MSY0
to
1
=
11,
MAX0
to
3
=
0011
(X
axis
positioning
operation
time)
>
(Y
axis
positioning
operation
time)
Summary of Contents for PCL6113
Page 1: ...User s Manual For PCL6113 6123 6143 Pulse Control LSI Nippon Pulse Motor Co Ltd...
Page 11: ...5 3 Terminal Assignment Diagram 3 1 PCL6113 3 2 PCL6123...
Page 20: ...14 5 Block Diagram...
Page 115: ...109 11 Stop timing by error...
Page 116: ...110 13 External Dimensions 13 1 PCL6113...
Page 117: ...111 13 2 PCL6123...
Page 118: ...112 13 3 PCL6143...