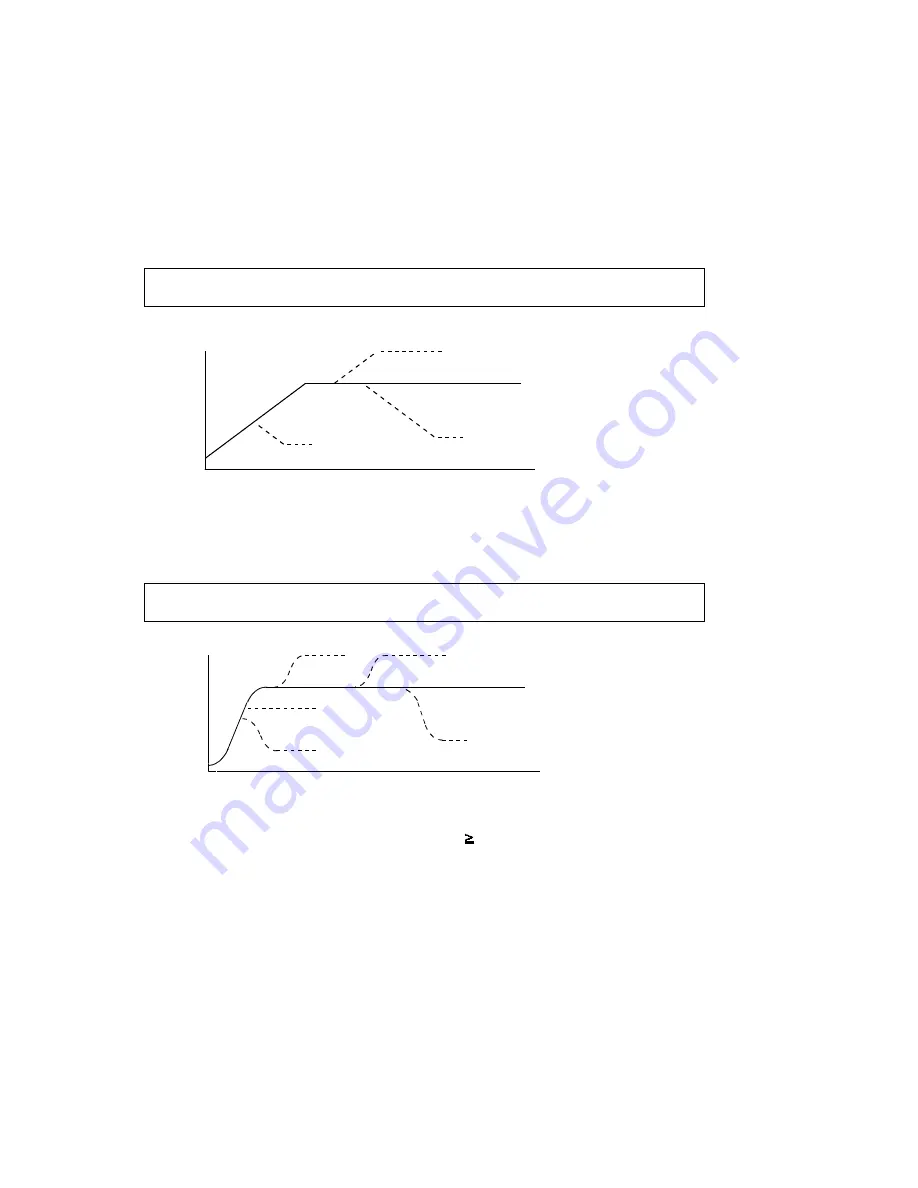
-
71
-
10-5.
Changing
speed
patterns
while
in
operation
By
changing
the
RFH,
RUR,
RDR,
RUS,
or
RDS
registers
during
operation,
the
speed
and
acceleration
can
be
changed
on
the
fly.
However,
if
the
ramping-down
point
was
set
to
automatic
(MSDP
=
0
in
the
RDM
register)
for
the
positioning
mode,
do
not
change
the
values
for
RFL,
RUR,
RDR,
RUS,
or
RDS.
The
automatic
ramping-down
point
function
will
not
work
correctly.
When
using
S-curve
acceleration/deceleration,
and
the
ramp
down
point
auto
setting
is
selected,
if
you
want
to
change
the
speed
during
operation,
you
must
set
PRUS
=
PRDS
=
0.
If
the
PCL
reached
the
ramp
down
point
while
still
accelerating
and
started
to
ramp
down,
it
would
stop
feeding
without
decelerating
to
the
FL
speed.
Therefore,
in
this
case,
you
must
be
careful
about
changing
the
speed
timing.
When
using
linear
acceleration/deceleration,
you
do
need
not
to
be
concerned
about
this
timing.
An
example
of
changing
the
speed
pattern
by
changing
the
speed,
during
a
linear
acceleration/deceleration
operation
1)
Use
a
small
RFH
while
accelerating
or
decelerating
the
axis
until
it
reaches
the
correct
speed.
2),
3)
Change
RFH
after
the
acceleration/deceleration
is
complete.
The
axis
will
continue
accelerating
or
decelerating
until
it
reaches
the
new
speed.
An
example
of
changing
the
speed
pattern
by
changing
the
speed
during
S-curve
acceleration/deceleration
operation
1)
Use
a
small
RFH
and
if
((change
speed)
<
(speed
before
change))
and
the
axis
will
accelerate/decelerate
using
an
S-curve
until
it
reaches
the
correct
speed.
5)
Use
a
small
RFH
and
if
((change
speed)
(speed
before
change))
and
the
axis
will
accelerate/decelerate
without
changing
the
S-curve's
characteristic
until
it
reaches
the
correct
speed.
4)
Use
a
large
RFH
while
accelerating
and
the
axis
will
accelerate
to
the
original
speed
entered
without
changing
the
S-curve's
characteristic.
Then
it
will
accelerate
again
until
it
reaches
the
newly
set
speed.
2),
3)
If
RFH
is
changed
after
the
acceleration/deceleration
is
complete,
the
axis
will
accelerate/decelerate
using
an
S-curve
until
it
reaches
the
correct
speed.
Speed
Time
1)
2)
3)
Speed
Time
1)
2)
3)
5)
4)
Summary of Contents for PCL6113
Page 1: ...User s Manual For PCL6113 6123 6143 Pulse Control LSI Nippon Pulse Motor Co Ltd...
Page 11: ...5 3 Terminal Assignment Diagram 3 1 PCL6113 3 2 PCL6123...
Page 20: ...14 5 Block Diagram...
Page 115: ...109 11 Stop timing by error...
Page 116: ...110 13 External Dimensions 13 1 PCL6113...
Page 117: ...111 13 2 PCL6123...
Page 118: ...112 13 3 PCL6143...