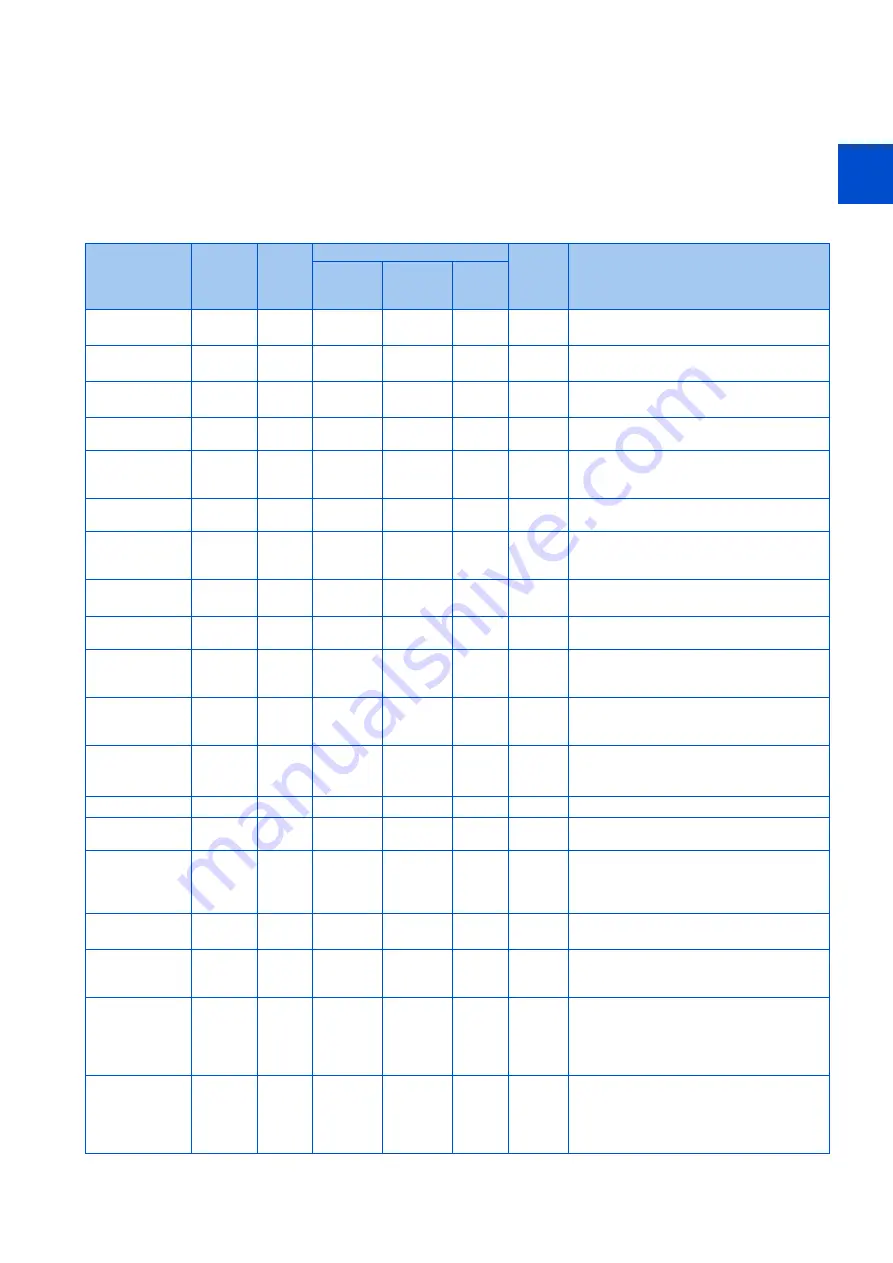
11
12
13
14
15
16
17
18
19
20
271
12. (M) Item and Output Signal for Monitoring
12.2 Monitor item selection on operation panel or via communication
Monitor item list (Pr.52, Pr.774 to Pr.776, Pr.992)
• Use
Pr.52, Pr.774 to Pr.776, or Pr.992
to select the monitor item to be displayed on the operation panel.
• Refer to the following table to find the setting value for each monitoring. The value in the Pr. setting column is set in each
of the parameters for monitoring (
Pr.52, Pr.774 to Pr.776,
and
Pr.992
) to determine the monitor item. The value in the
Communication column is the monitor code for communication. (The items marked with “—" cannot be selected. The circle
(
○
) in the Negative indication (-) column denotes that the monitored item can be indicated with minus sign during monitoring
via the communication option.
Monitor item
Incremen
t and unit
Pr.
setting
Communication
Negative
indicatio
n (-)
Description
Monitor
code 1
Monitor
code 2
Monitor
number
Output frequency
(speed)
1/0/100
H01
40201
1
○
The inverter output frequency is displayed.
Output
current
0.01 A
2/0/100
H02
40202
2
The inverter output current effective value is
displayed.
Output
voltage
0.1 V
3/0/100
H03
40203
3
The inverter output voltage is displayed.
Fault indication
—
0/100
—
—
—
Each of the last 10 faults is displayed
individually.
Set frequency /
motor speed
setting
H05
40205
5
The set frequency is displayed.
Operation speed
1 (r/min)
H06
40206
6
○
The motor speed is displayed (depending on the
Pr.53
setting). (Refer to
.)
Motor torque
0.1%
H07
40207
7
○
The motor torque is displayed as a percentage
(0% under V/F control), considering the rated
torque as 100%.
Converter output
voltage
0.1 V
H08
40208
8
The DC bus voltage value is displayed.
Regenerative
brake duty
0.1%
H09
40209
9
Brake duty set in
Pr.70
for the regeneration unit
set in
Pr.30
is displayed.
Electronic thermal
O/L relay load
factor
0.1%
10
H0A
40210
A
The motor thermal cumulative value is
displayed, considering the thermal operation
level as 100%.
Output current
peak value
0.01 A
11
H0B
40211
B
The peak value of output current, which is
constantly stored, is displayed. (It is reset with
every startup of the inverter.)
Converter output
voltage peak
value
0.1 V
12
H0C
40212
C
The DC bus voltage peak value, which is
constantly stored, is displayed. (It is reset with
every startup of the inverter.)
Input power
0.01 kW
13
H0D
40213
D
The power at the inverter input side is displayed.
Output power
0.01 kW
14
H0E
40214
E
The power at the inverter output side is
displayed.
Load meter
0.1%
17
H11
40217
11
Torque current is displayed as a percentage,
considering
Pr.56
setting value as 100%. (0% is
displayed under the control mode other than V/
F control.)
Motor excitation
current
0.01 A
18
H12
40218
12
The motor excitation current is displayed.
—
19
H13
40219
13
The position pulse of the encoder is displayed.
(The output voltage is displayed when a vector
control option is not installed.)
Cumulative
energization
time
1h
20
H14
40220
14
The cumulative energization time since the
inverter shipment is displayed. The number of
times an integrated value has reached the
maximum value of 65535 hours can be checked
in
Pr.563
.
Actual operation
time
1 h
23
H17
40223
17
The cumulative operation time is displayed. The
number of times an integrated value has
reached the maximum value of 65535 hours can
be checked in
Pr.564
. Use
Pr.171
to reset the
cumulative operation time. (Refer to
.)
Summary of Contents for FR-E800
Page 17: ...16 1 Introduction 1 3 Related manuals MEMO ...
Page 51: ...50 2 Basic Operation 2 8 I O terminal function assignment MEMO ...
Page 89: ...88 3 Parameters 3 4 Parameter list by function group number MEMO ...
Page 135: ...134 5 Speed Control 5 9 Troubleshooting in the speed control MEMO ...
Page 153: ...152 6 Torque Control 6 7 Troubleshooting in torque control MEMO ...
Page 195: ...194 8 E Environment Setting Parameters 8 18 Current average value monitor signal MEMO ...
Page 237: ...236 10 D Operation Command and Frequency Command 10 6 Operation by multi speed setting MEMO ...
Page 339: ...338 13 T Multi Function Input Terminal Parameters 13 9 Start signal operation selection MEMO ...
Page 455: ...454 16 G Control Parameters 16 13 Speed smoothing control MEMO ...