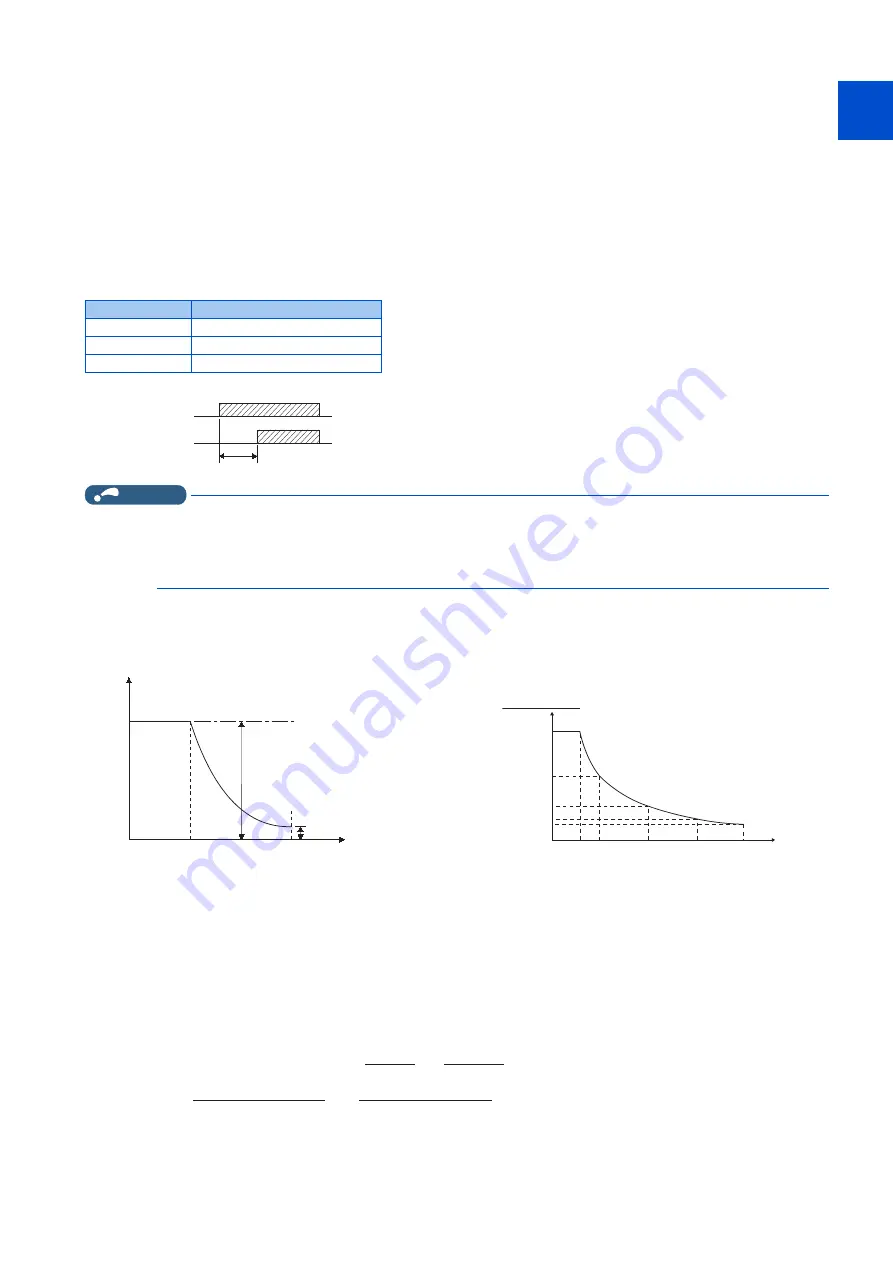
11
12
13
14
15
16
17
18
19
20
259
11. (H) Protective Function Parameters
11.10 Stall prevention operation
Adjusting the stall prevention operation signal and output timing (OL
signal, Pr.157)
• If the output current exceeds the stall prevention operation level and stall prevention is activated, or the fast-response
current limit is enabled, Overload warning (OL) signal turns ON for 100 ms or more. The output signal turns OFF when the
output current falls to the stall prevention operation level or less.
•
Pr.157 OL signal output timer
can be used to set whether to output the OL signal immediately, or whether to output it
after a certain time period has elapsed.
• This function also operates during regeneration avoidance operation ("OLV" (overvoltage stall)).
• For the OL signal, set "3" (positive logic) or "103" (negative logic) in any parameter from
Pr.190 to Pr.196 (Output terminal
function selection)
to assign the function to the output terminal.
NOTE
• If the stall prevention operation has lowered the output frequency to 1 Hz and kept the level for 3 seconds, the stall prevention
stop (E.OLT) is activated to shut off the inverter output.
• Changing the terminal assignment using
Pr.190 to Pr.196 (Output terminal function selection)
may affect the other
functions. Set parameters after confirming the function of each terminal.
Setting for stall prevention operation in the high-frequency range (Pr.22,
Pr.23, Pr.66)
• When operating at the rated motor frequency or higher, acceleration may not be made because the motor current does
not increase. Also, when operating in the high-frequency range, the current flowing to the locked motor becomes less than
the rated output current of the inverter. Even if the motor is stopped, the protective function does not operate (OL). In a
case like this, the stall prevention level can be reduced in the high-frequency range to improve the motor's operating
characteristics. This is useful when operating up to the high speed range, such as when using a centrifuge. Normally, set
Pr.66 Stall prevention operation reduction starting frequency
to 60 Hz, and
Pr.23 Stall prevention operation level
compensation factor at double speed
to 100%.
• Calculation formula for stall prevention operation level
• When
Pr.23
= "9999" (initial value), the stall prevention operation level is constant at the
Pr.22
level up to 590 Hz.
Pr.157 setting
Description
0 (initial value)
Output immediately.
0.1 to 25
Output after the set time (s).
9999
Not output.
Overload state
(OL operation)
OL output signal
Pr.157
Set time(s)
Output frequency (Hz)
Pr.22
Always at the
Pr.22
level
when
Pr.23
= "9999"
Pr.66
400Hz
Stall prevention operation
level (%)
Stall prevention operation level
as set in
Pr.23
Output frequency (Hz)
Setting example (
Pr.22
= 150%,
Pr.23
= 100%,
Pr.66
= 60Hz)
18
0
100
60
200
300
400
24
36
72
120
Stall prevention operation
level (%)
= A + B × [
Pr.22
- A
] × [
Pr.23
- 100
]
Pr.22
- B
100
A =
Pr.66
(Hz) ×
Pr.22
(%)
, B =
Pr.66
(Hz) ×
Pr.22
(%)
Output frequency (Hz)
400 Hz
Stall prevention operation level (%)
in the high-frequency range
Where,
Summary of Contents for FR-E800
Page 17: ...16 1 Introduction 1 3 Related manuals MEMO ...
Page 51: ...50 2 Basic Operation 2 8 I O terminal function assignment MEMO ...
Page 89: ...88 3 Parameters 3 4 Parameter list by function group number MEMO ...
Page 135: ...134 5 Speed Control 5 9 Troubleshooting in the speed control MEMO ...
Page 153: ...152 6 Torque Control 6 7 Troubleshooting in torque control MEMO ...
Page 195: ...194 8 E Environment Setting Parameters 8 18 Current average value monitor signal MEMO ...
Page 237: ...236 10 D Operation Command and Frequency Command 10 6 Operation by multi speed setting MEMO ...
Page 339: ...338 13 T Multi Function Input Terminal Parameters 13 9 Start signal operation selection MEMO ...
Page 455: ...454 16 G Control Parameters 16 13 Speed smoothing control MEMO ...