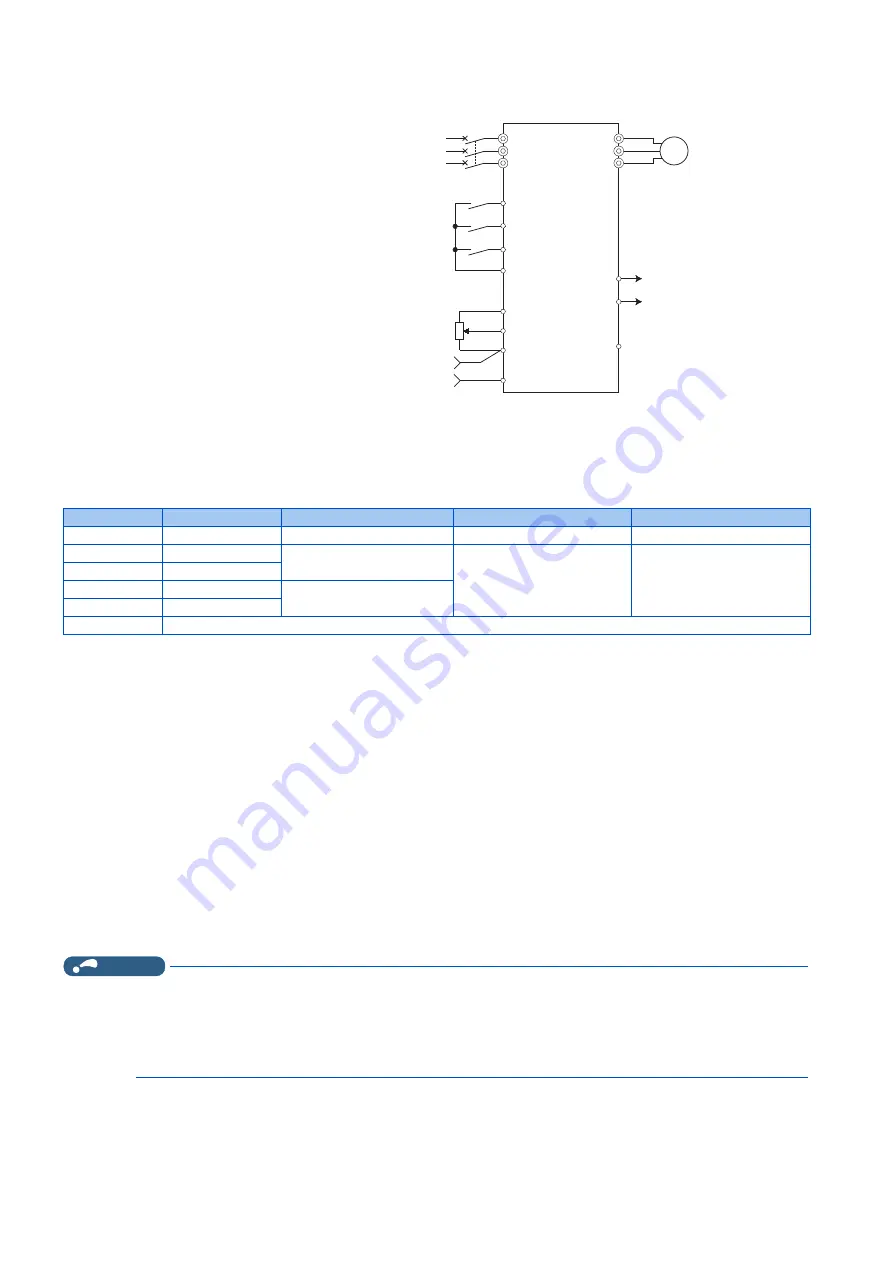
398
15. (A) Application Parameters
15.6 Dancer control
Connection diagram
*1
The main speed command differs according to each operation mode (External, PU, communication).
*2
The applied output terminals differ by the settings of
Pr.190 to Pr.196 (Output terminal function selection)
.
*3
The applied input terminals differ by the settings of
Pr.178 to Pr.189 (Input terminal function selection)
.
*4
The AU signal need not be input.
Dancer control operation selection (Pr.128)
*1
When
Pr.133
≠
"9999", the
Pr.133
setting is valid.
• To enable dancer control, set "40 to 43" in
Pr.128 PID action selection
.
• Dancer control is enabled only when the PID control valid (X14) signal turns ON when "14" is set in one of
Pr.178 to Pr.182
(Input terminal function selection)
and X14 signal is assigned. When the X14 signal is not assigned, dancer control is
enabled only by the
Pr.128
setting.
• Input the main speed command (External, PU, Communication). Dancer control is also supported by the main speed
command in all operation modes.
• Input the set point between the terminals 2 and 5 (the setting can be selected using
Pr.133
or
Pr.609
) and input the
measured value signal (dancer roll position detection signal) between the inverter terminals 4 and 5 (the setting can be
selected using
Pr.610
).
• The action of
Pr.129 PID proportional band, Pr.130 PID integral time, Pr.131 PID upper limit, Pr.132 PID lower limit
and Pr.134 PID differential time
is the same as PID control action. In the relationship between the control amount (%)
and frequency in PID control, 0% is equivalent to the frequencies set in
C2 (Pr.902)
and 100% is equivalent to the
frequencies set in
Pr.125
.
NOTE
• When
Pr.128
is set to "0" or the X14 signal is OFF, regular inverter running not dancer control is performed.
• Dancer control is enabled by turning ON/OFF the bits of terminals assigned the X14 signal by RS-485 communication or over
the network.
• When dancer control is selected, set the PID output suspension function (
Pr.575 Output interruption detection time
=
"9999").
• Sink logic
•
Pr.128
= "41"
•
Pr.182
= "14"
•
Pr.193
= "14"
•
Pr.194
= "15"
•
Pr.133
= Set point
Power supply
MCCB
Inverter
Forward rotation
Reverse rotation
PID control selection
Main speed command
setting potentiometer
*1
R/L1
S/L2
T/L3
STF
STR
RH(X14)
*3
SD
10
2
5
4
*4
U
V
W
*2
(FUP)FU
SE
Motor
M
Upper limit
*2
(FDN)RUN
Lower limit
Output signal common
Feedback value of
dancer roll position
Pr.128 setting
PID action
Additive method
Set point input
Measured value input
0
PID disabled
—
—
—
40
Reverse action
Fixed
Set by
Pr.133
or input by
terminal selected by
Input by terminal selected by
Pr.610
41
Forward action
42
Reverse action
Ratio
43
Forward action
Others
Refer to
Summary of Contents for FR-E800
Page 17: ...16 1 Introduction 1 3 Related manuals MEMO ...
Page 51: ...50 2 Basic Operation 2 8 I O terminal function assignment MEMO ...
Page 89: ...88 3 Parameters 3 4 Parameter list by function group number MEMO ...
Page 135: ...134 5 Speed Control 5 9 Troubleshooting in the speed control MEMO ...
Page 153: ...152 6 Torque Control 6 7 Troubleshooting in torque control MEMO ...
Page 195: ...194 8 E Environment Setting Parameters 8 18 Current average value monitor signal MEMO ...
Page 237: ...236 10 D Operation Command and Frequency Command 10 6 Operation by multi speed setting MEMO ...
Page 339: ...338 13 T Multi Function Input Terminal Parameters 13 9 Start signal operation selection MEMO ...
Page 455: ...454 16 G Control Parameters 16 13 Speed smoothing control MEMO ...