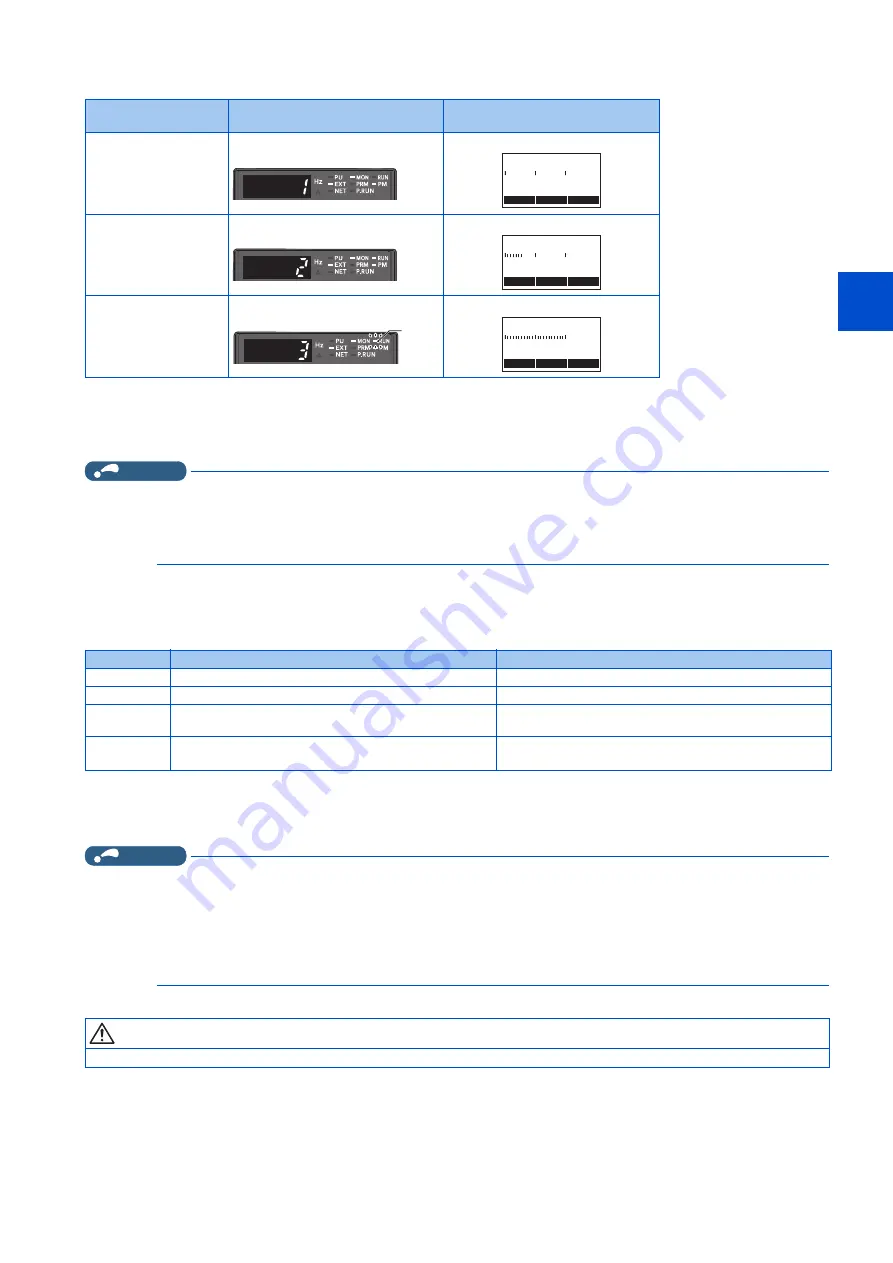
11
12
13
14
15
16
17
18
19
20
359
14. (C) Motor Constant Parameters
14.3 Offline auto tuning for a PM motor (motor constant tuning)
• During tuning, the monitor is displayed on the operation panel as follows.
• When offline auto tuning ends, press the STOP/RESET key on the operation panel during PU operation. In the External
operation, turn OFF the start signal (STF signal or STR signal). This operation resets the offline auto tuning, and the
monitor display of the operation panel returns to normal. (Without this operation, next operation cannot be started.)
NOTE
• The motor constants measured once during offline auto tuning are stored as parameters and their data are held until offline
auto tuning is performed again. However, the tuning data is cleared when performing All parameter clear.
• Changing
Pr.71
after tuning completion will change the motor constant. For example, if the
Pr.71
setting is changed to "8093"
after tuned with
Pr.71
= "8090", the tuning data become invalid. To use the tuned data, set "8090" again in
Pr.71
.
• If offline auto tuning has ended in error (see the following table), motor constants are not set.
Perform an inverter reset and perform tuning again.
• When tuning is ended forcibly by pressing the STOP/RESET key or turning OFF the start signal (STF or STR) during
tuning, offline tuning does not end properly. (The motor constants have not been set.)
Perform an inverter reset and perform tuning again.
NOTE
• An instantaneous power failure occurring during tuning will result in a tuning error.
After power is restored, the inverter starts normal operation. Therefore, when the STF (STR) signal is ON, the motor starts
forward (reverse) rotation.
• Any fault occurring during tuning is handled as in the normal operation. However, if the retry function is set, no retry is
performed even when a protective function that performs a retry is activated.
• The set frequency monitor displayed during the offline auto tuning is 0 Hz.
Tuning status
Operation panel indication
LCD operation panel (FR-LU08)
display
(1) Setting
(2) During tuning
(3) Normal completion
AutoTune 12:34
TUNE
1
--- STOP
PU
PREV
NEXT
AutoTune 12:34
TUNE
2
STF
FWD
PU
PREV
NEXT
Blinking
AutoTune 12:34
TUNE
Completed
3
STF STOP
PU
PREV
NEXT
Error display
Error cause
Countermeasures
8
Forced end
Set "1" in
Pr.96 (Pr.463)
and retry.
9
Inverter protective function operation
Make the setting again.
92
The converter output voltage fell to 75% of the rated voltage.
Check for the power supply voltage fluctuation.
Check the
Pr.83 Rated motor voltage
setting.
93
Calculation error.
The motor is not connected.
Check the motor wiring and make the setting again.
CAUTION
• Note that the motor may start running suddenly.
Summary of Contents for FR-E800
Page 17: ...16 1 Introduction 1 3 Related manuals MEMO ...
Page 51: ...50 2 Basic Operation 2 8 I O terminal function assignment MEMO ...
Page 89: ...88 3 Parameters 3 4 Parameter list by function group number MEMO ...
Page 135: ...134 5 Speed Control 5 9 Troubleshooting in the speed control MEMO ...
Page 153: ...152 6 Torque Control 6 7 Troubleshooting in torque control MEMO ...
Page 195: ...194 8 E Environment Setting Parameters 8 18 Current average value monitor signal MEMO ...
Page 237: ...236 10 D Operation Command and Frequency Command 10 6 Operation by multi speed setting MEMO ...
Page 339: ...338 13 T Multi Function Input Terminal Parameters 13 9 Start signal operation selection MEMO ...
Page 455: ...454 16 G Control Parameters 16 13 Speed smoothing control MEMO ...