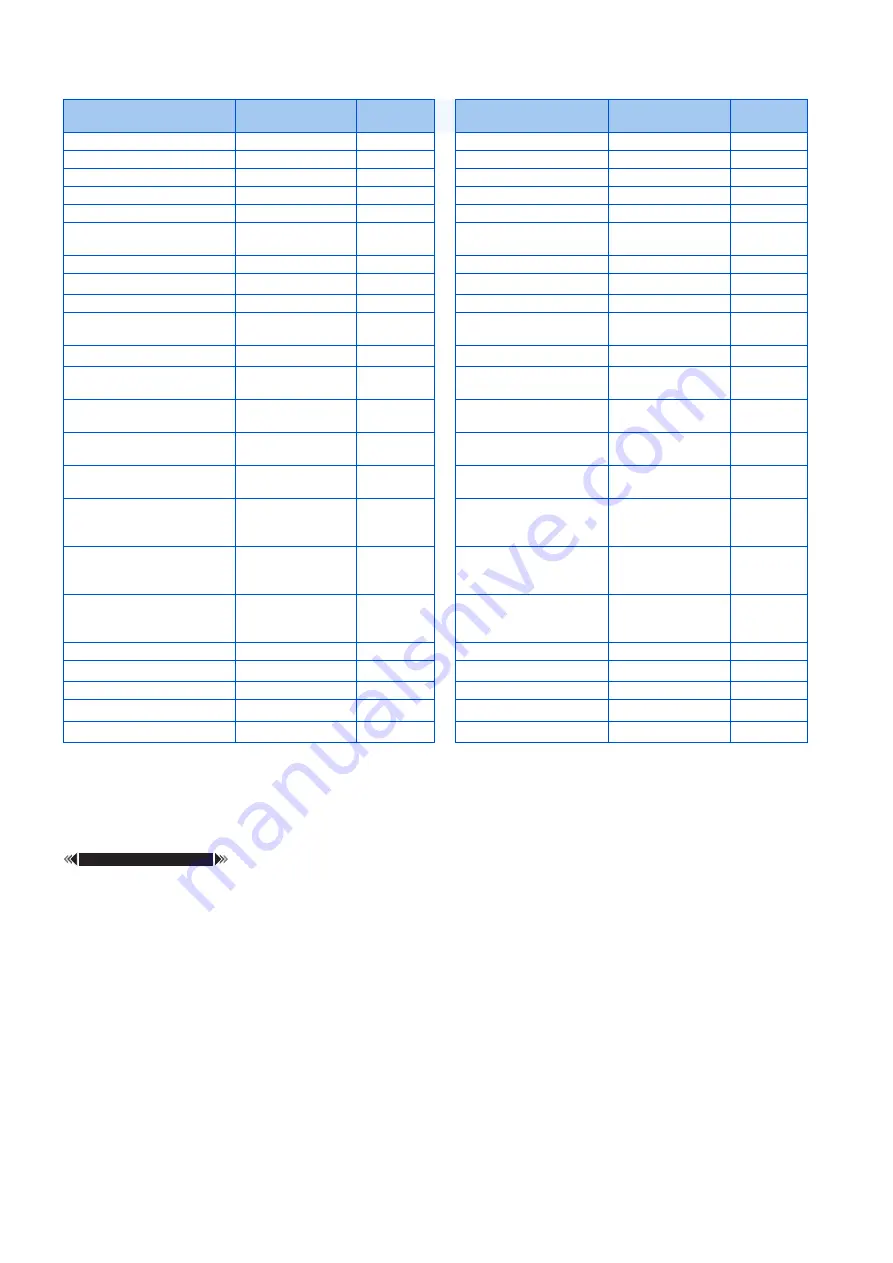
100
4. Control Method
4.2 Changing the control method and mode
—: Not available
*1
When the inverter operation is switched to the test operation, the indication is changed to 0. When PM sensorless vector control is selected again
after the test operation, the output current peak value and the electronic thermal relay load factor from the last operation are displayed.
*2
When the inverter operation is switched to the test operation, the accumulated thermal value is reduced because the output current is considered
as 0.
*3
During the test operation, only the average power saving, average power saving rate, and average power cost savings can be monitored.
*4
Enabled under Vector control only.
Parameters referred to
Operation panel main monitor selection
Pr.158 AM terminal function selection
Changing the control method with external terminals (RT signal, X18
signal)
• Control method (V/F control, Advanced magnetic flux vector control, Real sensorless vector control, Vector control) can
be switched using external terminals.
The control method can be switched using either the Second function selection (RT) signal or the V/F switchover (X18)
signal.
• Set the second motor in
Pr.450 Second applied motor
and set the second motor's control method in
Pr.451 Second
motor control method selection
. Turning ON the RT signal or X18 signal enables the second function, enabling the
switchover of the control method.
Monitor item
Monitoring on the
operation panel
Output via
FM/AM
Monitor item
Monitoring on the
operation panel
Output via
FM/AM
Output frequency
○
○
Feedback pulse
×
—
Output current
×
×
Trace status
○
—
Output voltage
×
×
User monitor 1
○
—
Fault indication
○
—
User monitor 2
○
—
Frequency setting value
○
○
User monitor 3
○
—
Motor speed
○
○
Communication station
number (PU port)
○
—
Motor torque
○
○
Station number (CC-Link)
○
—
Converter output voltage
○
○
Energy saving effect
Δ
Δ
Brake duty
×
×
Cumulative energy saving
Δ
—
Electronic thermal O/L relay
load factor
×
PID set point
○
○
Output current peak value
×
PID measured value
○
○
Converter output voltage peak
value
○
○
PID deviation
○
—
Output power
×
×
Inverter I/O terminal
monitor
○
—
Load meter
×
×
Option input terminal
monitor
○
—
Motor excitation current
×
×
Option output terminal
monitor
○
—
Position pulse
×
—
Option input terminal
monitor 1 (for
communication)
○
—
Cumulative energization time
○
—
Option input terminal
monitor 2 (for
communication)
○
—
Reference voltage output
—
○
Option output terminal
monitor (for
communication)
○
—
Actual operation time
○
—
Motor thermal load factor
×
×
Motor load factor
×
×
Inverter thermal load factor
○
Cumulative energy
Δ
—
PID measured value 2
○
○
Commanded torque
○
PID manipulated variable
○
—
Torque current command
○
Dancer main speed setting
○
○
Summary of Contents for FR-E800
Page 17: ...16 1 Introduction 1 3 Related manuals MEMO ...
Page 51: ...50 2 Basic Operation 2 8 I O terminal function assignment MEMO ...
Page 89: ...88 3 Parameters 3 4 Parameter list by function group number MEMO ...
Page 135: ...134 5 Speed Control 5 9 Troubleshooting in the speed control MEMO ...
Page 153: ...152 6 Torque Control 6 7 Troubleshooting in torque control MEMO ...
Page 195: ...194 8 E Environment Setting Parameters 8 18 Current average value monitor signal MEMO ...
Page 237: ...236 10 D Operation Command and Frequency Command 10 6 Operation by multi speed setting MEMO ...
Page 339: ...338 13 T Multi Function Input Terminal Parameters 13 9 Start signal operation selection MEMO ...
Page 455: ...454 16 G Control Parameters 16 13 Speed smoothing control MEMO ...