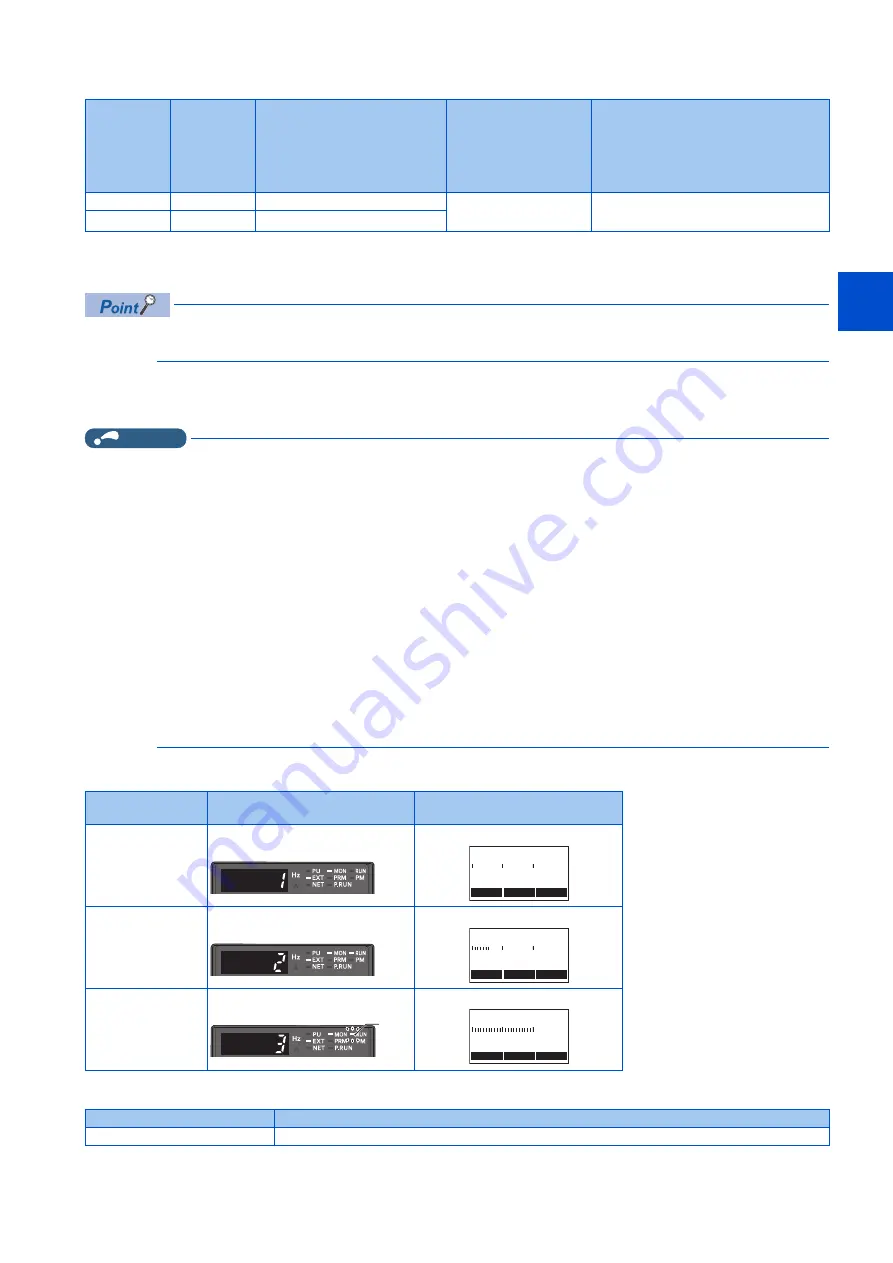
11
12
13
14
15
16
17
18
19
20
349
14. (C) Motor Constant Parameters
14.2 Offline auto tuning
• For tuning accuracy improvement, set the following parameters when the motor constants are known in advance.
*1
The setting is valid only when a value other than "9999" is set in both
Pr.707 (Pr.744)
and
Pr.724 (Pr.745)
.
Performing tuning
• Before performing tuning, check the monitor display of the operation panel if the inverter is in the state ready for tuning. The
motor starts by turning ON the start command while tuning is unavailable.
• In the PU operation mode, press the RUN key on the operation panel.
In the External operation, turn ON the start command (STF signal or STR signal). Tuning starts.
NOTE
• Satisfy the required inverter start conditions to start offline auto tuning. For example, stop the input of the MRS signal.
• To force tuning to end, use the MRS or RES signal or the STOP/RESET key on the operation panel.
(Turning OFF the start signal (STF signal or STR signal) also ends tuning.)
• During offline auto tuning, only the following I/O signals are valid (initial value).
Input terminals <effective signals>: MRS, RES, STF, STR, S1, and S2
Output terminals: RUN, FU, FM, AM, ABC, and SO
• When the rotation speed and the output frequency are selected for terminals FM and AM, the progress status of offline auto
tuning is output in 15 steps from FM and AM (in the standard model).
• Do not perform ON/OFF switching of the Second function selection (RT) signal during offline auto tuning. Auto tuning will not
be performed properly.
• Since the Inverter running (RUN) signal turns ON when tuning is started, pay close attention especially when a sequence which
releases a mechanical brake by the RUN signal has been designed.
• When executing offline auto tuning, input the operation command after switching ON the main circuit power (R/L1, S/L2, T/L3)
of the inverter.
• While
Pr.79 Operation mode selection
= "7", turn ON the PU operation external interlock (X12) signal for tuning in the PU
operation mode.
• During tuning, the monitor is displayed on the operation panel as follows.
• Note: Offline auto tuning time (with the initial setting)
First motor
Pr.
Second
motor Pr.
Name
Mitsubishi Electric
motor (SF-PR, SF-PR-
SC, SF-JR, SF-HR, SF-
JRCA, SF-HRCA, SF-
V5RU, GM-[], GM-DZ, or
GM-DP)
Other motors
707
744
Motor inertia (integer)
9999 (initial value)
Jm =
Pr.707
× 10^(
-Pr.724
) (kg·m
2
)
724
745
Motor inertia (exponent)
Tuning status
Operation panel indication
LCD operation panel (FR-LU08)
display
(1) Setting
(2) During tuning
(3) Normal
completion
AutoTune 12:34
TUNE
1
--- STOP
PU
PREV
NEXT
AutoTune 12:34
TUNE
2
STF
FWD
PU
PREV
NEXT
Blinking
AutoTune 12:34
TUNE
Completed
3
STF STOP
PU
PREV
NEXT
Offline auto tuning setting
Time
Pr.96
= "1"
About 25 to 100 s. (The time depends on the inverter capacity and motor type.)
Summary of Contents for FR-E800
Page 17: ...16 1 Introduction 1 3 Related manuals MEMO ...
Page 51: ...50 2 Basic Operation 2 8 I O terminal function assignment MEMO ...
Page 89: ...88 3 Parameters 3 4 Parameter list by function group number MEMO ...
Page 135: ...134 5 Speed Control 5 9 Troubleshooting in the speed control MEMO ...
Page 153: ...152 6 Torque Control 6 7 Troubleshooting in torque control MEMO ...
Page 195: ...194 8 E Environment Setting Parameters 8 18 Current average value monitor signal MEMO ...
Page 237: ...236 10 D Operation Command and Frequency Command 10 6 Operation by multi speed setting MEMO ...
Page 339: ...338 13 T Multi Function Input Terminal Parameters 13 9 Start signal operation selection MEMO ...
Page 455: ...454 16 G Control Parameters 16 13 Speed smoothing control MEMO ...