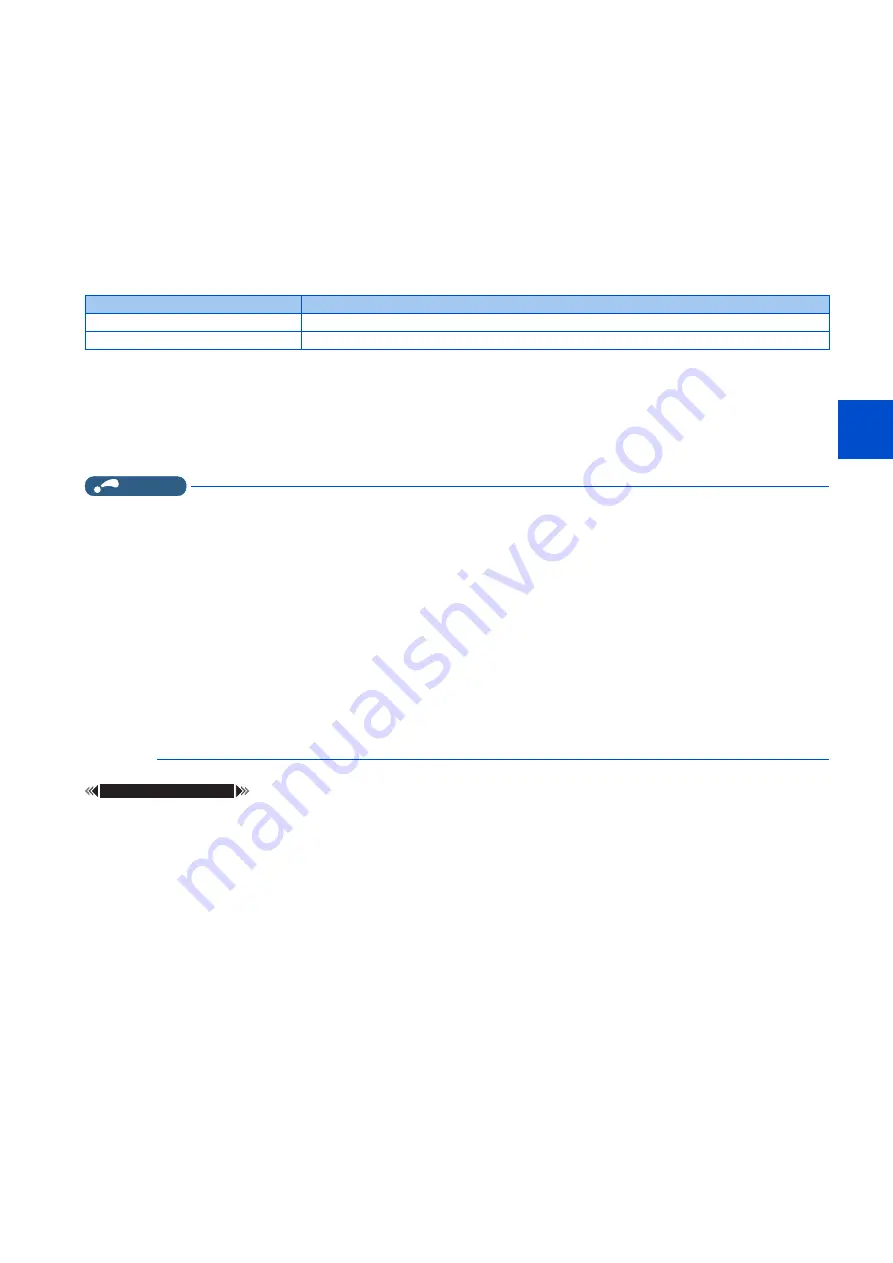
11
12
13
14
15
16
17
18
19
20
451
16. (G) Control Parameters
16.11 Encoder feedback control
• Example: when the rated speed of a motor (4 poles) is 1740 r/min at 60 Hz
Feedback gain (Pr.368)
• Set
Pr.368 Feedback gain
when the rotation is unstable or response is slow.
• Response of the feedback will become slow when the acceleration/deceleration time is long. In such case, increase the
setting value of
Pr.368
.
Overspeed detection (Pr.285)
• To prevent malfunction when the correct pulse signal cannot be detected from the encoder, when
[detection frequency] - [output frequency] >
Pr.285
during encoder feedback control, a protective function (E.MB1) will be activated to shut off the inverter output.
• Overspeed detection is not performed when
Pr.285
= "9999".
NOTE
• Couple the encoder on the same axis as the motor axis without any mechanical clatter, with speed ratio of 1:1.
• Encoder feedback control is not performed during the acceleration and deceleration to prevent unstable operation such as
hunting.
• Encoder feedback control is performed after the output frequency has reached [set frequency] ± [speed feedback range] once.
• When the following status occurs during encoder feedback control operation, the inverter output is not shut off, the output
frequency becomes the value obtained by [set frequency] ± [speed feedback range], and tracking of the motor speed is not
performed.
When
Pr.376
= "0" and the pulse signal from the encoder is lost due to a break or other reasons
When correct pulse signal cannot be detected due to induction noise or other reasons
When the motor is forcefully accelerated (regenerative rotation) or decelerated (motor lock) due to large external force
• Use the Inverter running (RUN) signal when releasing the brake from the motor with a brake. (The brake may not be released
when the Output frequency detection (FU) signal is used.)
• Do not turn OFF the external power supply for the encoder during encoder feedback control. Normal encoder feedback control
will not be possible.
Parameters referred to
Pr.81 Number of motor poles
,
Slip Nsp = Synchronous speed - Rated speed
= 1800 - 1740
= 60 (r/min)
Frequency equivalent to slip (fsp) = Nsp × Number of poles/120
= 60 × 4/120
= 2 (Hz)
Pr.368 setting
Description
Pr.368
> 1
Response will become faster but it may cause overcurrent or unstable operation.
1 >
Pr.368
Response will become slower but the operation will become more stable.
Summary of Contents for FR-E800
Page 17: ...16 1 Introduction 1 3 Related manuals MEMO ...
Page 51: ...50 2 Basic Operation 2 8 I O terminal function assignment MEMO ...
Page 89: ...88 3 Parameters 3 4 Parameter list by function group number MEMO ...
Page 135: ...134 5 Speed Control 5 9 Troubleshooting in the speed control MEMO ...
Page 153: ...152 6 Torque Control 6 7 Troubleshooting in torque control MEMO ...
Page 195: ...194 8 E Environment Setting Parameters 8 18 Current average value monitor signal MEMO ...
Page 237: ...236 10 D Operation Command and Frequency Command 10 6 Operation by multi speed setting MEMO ...
Page 339: ...338 13 T Multi Function Input Terminal Parameters 13 9 Start signal operation selection MEMO ...
Page 455: ...454 16 G Control Parameters 16 13 Speed smoothing control MEMO ...