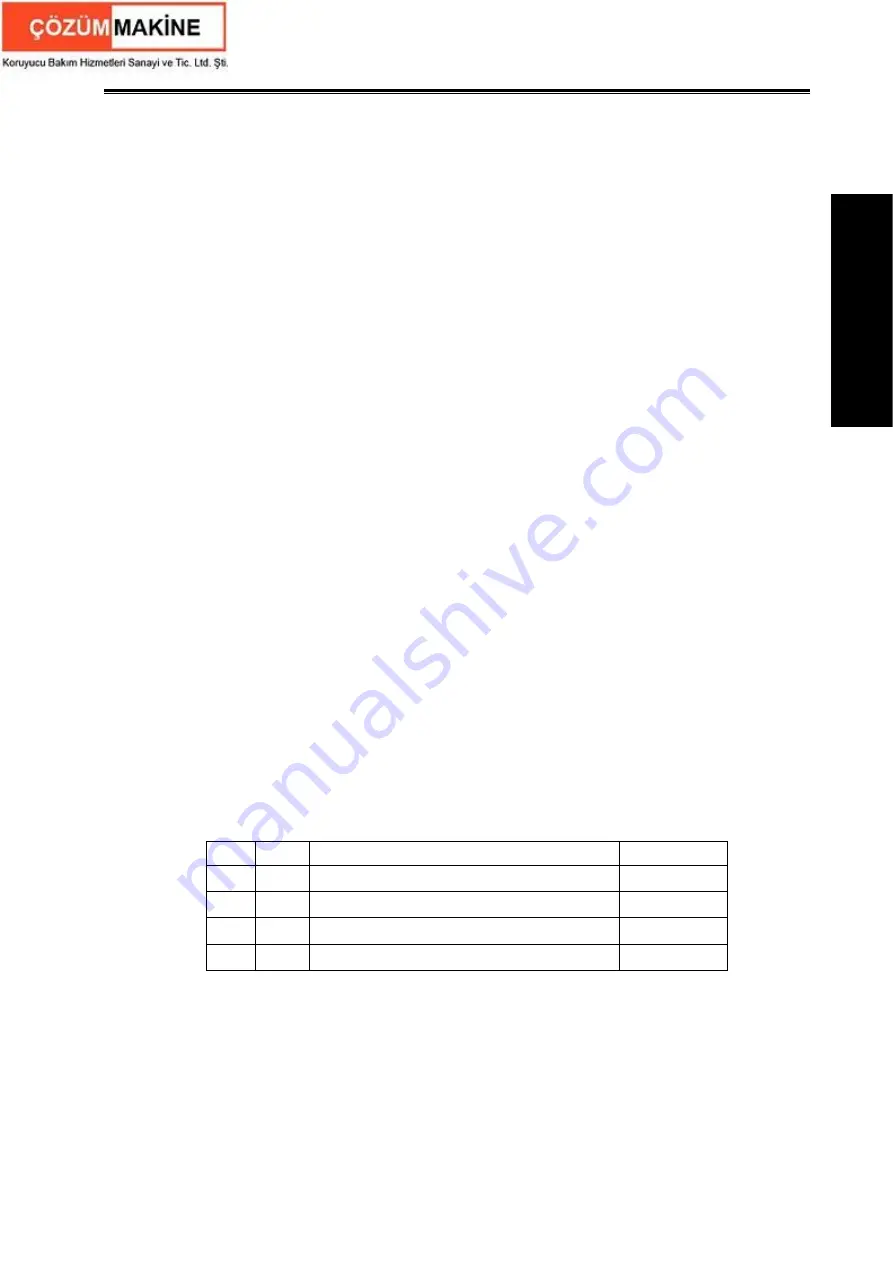
Chapter
Ⅳ
Tool Nose Radius Compensation
147
Ⅰ
Programming
defined by the motion command.
Note 1: In tool traversing compensation mode, when the system executes the tool offset, NO. 5002 Bit6 sets
the valid method of the tool offset:
LWM=0: it is valid in the block of T code
LWM=1: it is valid in the axis movement block
Note 2: No.5001 Bit6
(
EVO
)
sets the valid method of modifying tool wear tool when the system executes the
program:
EVO =0: it is valid in the next specified T code
EVO =1: it is valid in the next buffer block
Note: After the tool wear value is modified, the system executes the wear value in the tool traversing method
to avoid the too big wear value.
Note 3: It is suggested that the program should be complied according to the normative method, that is, the
tool change is executed in the safe position and then the absolute value command is used to position
to the starting point of the machining.
Note 4: In the coordinate offset compensation mode, when the system executes the tool offset and executes T
function command instead of movement command, it uses G50 to set the coordinate system, the
displayed absolute coordinate value is that the coordinate value set by G50 adds or subtracts the
unexecuted tool compensation value.
Note 5: T command can use the leading zero. When T00
□□
is commanded or only tool offset number is
commanded in the program and the current tool number is not changed, the system only
correspondingly modifies the current tool offset value.
Note 6: After executing the miscellaneous function lock is valid, the system does not execute the tool change
when T command is executed but the tool offset is executed. When using the miscellaneous function
lock checks the program function, it is executed in the safety position.
3.3.2 Tool Life Management
When the tool life management is used, TLF (No. 8132#0) is set to “1”.
The tools are divided into many groups. Each group specifies its corresponding tool life (the used
time or used times), and the used time or times are accumulated. When the current tool life arrives,
the next tool in the same group is selected according to the preset order. The system alarms when all
tool life are used in the same group.
3.3.2.1 Tool Life Management Data
Set the used most group number in No. 6813. Bit0 and Bit1 (GS1 and GS2) of No.6800 set the
actual group number and the most tool in each group.
GS2 GS1
Group number
Tool number
0 0 1/8 of 1
~
most group number (N0.6813)
1
~
16
0 1 1/4 of 1
~
most group number (N0.6813)
1
~
8
1 0 1/2 of 1
~
most group number (N0.6813)
1
~
4
1 1 1
~
most group number (N0.6813)
1
~
2
Note 1: After the above No. 6813 or No.6800 Bit0 and Bit1 (GS1 and GS2) are changed, inputting programs of
tool life data resets the tool life;
Note 2: The same tool number appears in any time in programs of tool life data;
Note 3: T command is consisted of the tool selection number and the tool offset number;
Note 4: No.5002 Bit 0 must be set to 0 when the tool life management function is used.
3.3.2.2 Tool Life Timing/Counting
When the tool life counting method in the input program of tool life data is not specified, LTM
(No.6800#2) value is set to confirm the time or times to specify the tool life.
Summary of Contents for 988T
Page 6: ...GSK988T Turning CNC System User Manual VI ...
Page 14: ...GSK988T Turning CNC System User Manual XIV ...
Page 15: ...Chapter 1 Programming Fundamentals 1 Ⅰ Programming Ⅰ PROGRAMMING ...
Page 16: ...GSK988T Turning CNC System User Manual 2 Ⅰ Programming ...
Page 194: ...GSK988T Turning CNC System User Manual 180 Ⅰ Programming ...
Page 195: ...Chapter Ⅰ Overview 181 Ⅱ Operation Ⅱ OPERATION ...
Page 196: ...GSK988T Turning CNC System User Manual 182 Ⅱ Operation ...
Page 217: ...Chapter Ⅲ Windows 203 Ⅱ Operation ...
Page 267: ...Chapter Ⅲ Windows 253 Ⅱ Operation Fig 3 51 Fig 3 52 ...