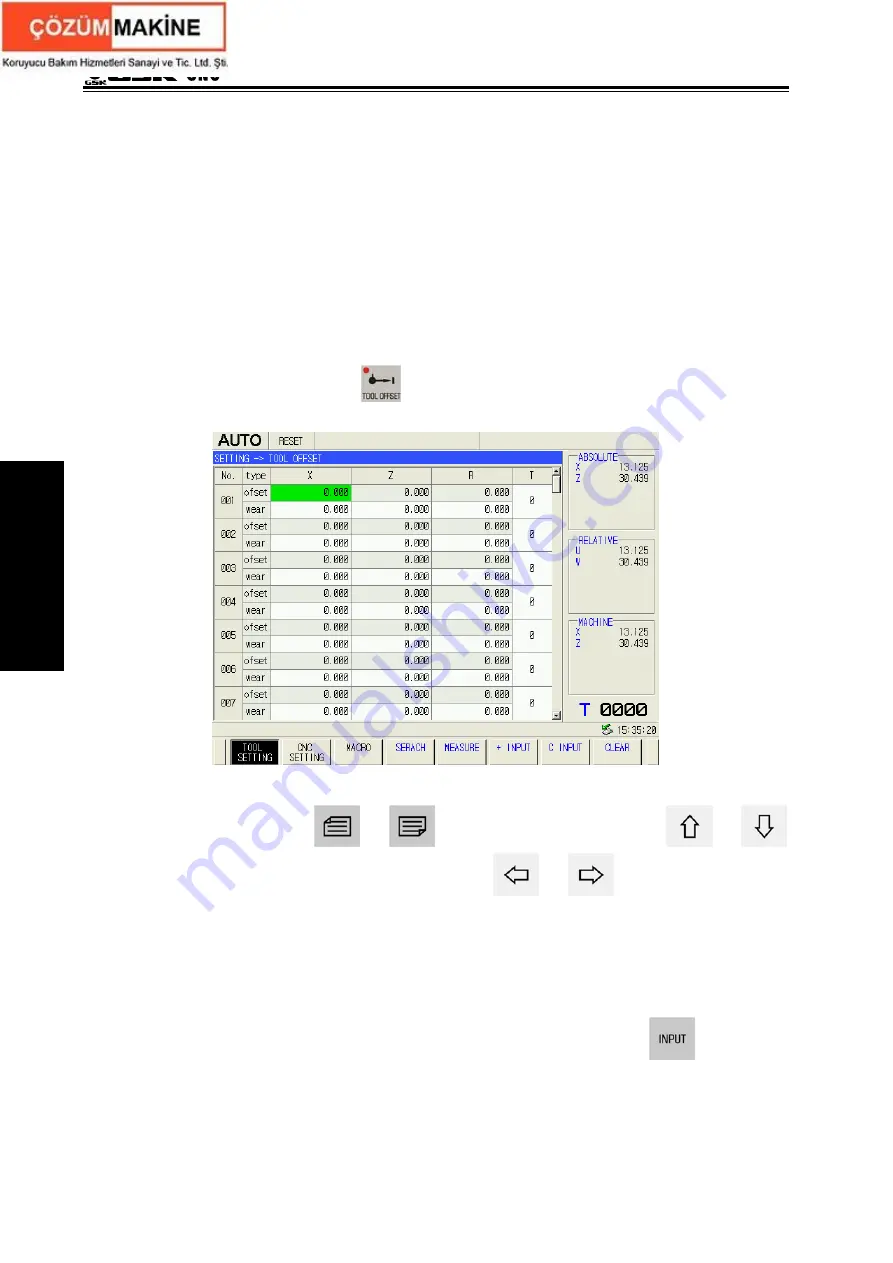
GSK988T Turning CNC System User Manual
282
Ⅱ
Operation
Chapter
Ⅶ
Tool Offset and Setting Tools
To simplify the programming, the actual position of the tool isn’t taken into consideration during
programming and GSK988T provides the methods of in-position tool-setting and trial cutting, etc, and
get the tool offset Value through setting tools.
7.1 Setting the Tool Offset and the Wearing Values
7.1.1 Direct input method
(
1
)
On the setting window, press
to access the tool offset management window, which is
shown as below:
Fig.7-1
(
2
)
On the window, press
or
to select the window, and press
or
to select the tool offset number to be rewritten, and press
or
to select the axial offset
Value, the wearing Value or T value of the assumed tool nose direction to be rewritten, which is
shown as X axis offset of #001 tool offset in the above figure; About the relative relation of the
assumed tool nose, refer to the tool nose radius compensation in the 4
th
chapter in
programming
introduction
.
(
3
)
Directly rewrite the tool offset Value, the wearing Value or the relative assumed tool nose
direction number T through the numerical keys or the backspace key; or press
to make the
selected tool offset value be input, such as X axis offset of #001 tool offset shown as the following
figure, and then rewrite the tool offset Value, the wearing Value or the corresponding assumed tool
nose direction number T through pressing the numerical keys or the backspace key.
Summary of Contents for 988T
Page 6: ...GSK988T Turning CNC System User Manual VI ...
Page 14: ...GSK988T Turning CNC System User Manual XIV ...
Page 15: ...Chapter 1 Programming Fundamentals 1 Ⅰ Programming Ⅰ PROGRAMMING ...
Page 16: ...GSK988T Turning CNC System User Manual 2 Ⅰ Programming ...
Page 194: ...GSK988T Turning CNC System User Manual 180 Ⅰ Programming ...
Page 195: ...Chapter Ⅰ Overview 181 Ⅱ Operation Ⅱ OPERATION ...
Page 196: ...GSK988T Turning CNC System User Manual 182 Ⅱ Operation ...
Page 217: ...Chapter Ⅲ Windows 203 Ⅱ Operation ...
Page 267: ...Chapter Ⅲ Windows 253 Ⅱ Operation Fig 3 51 Fig 3 52 ...