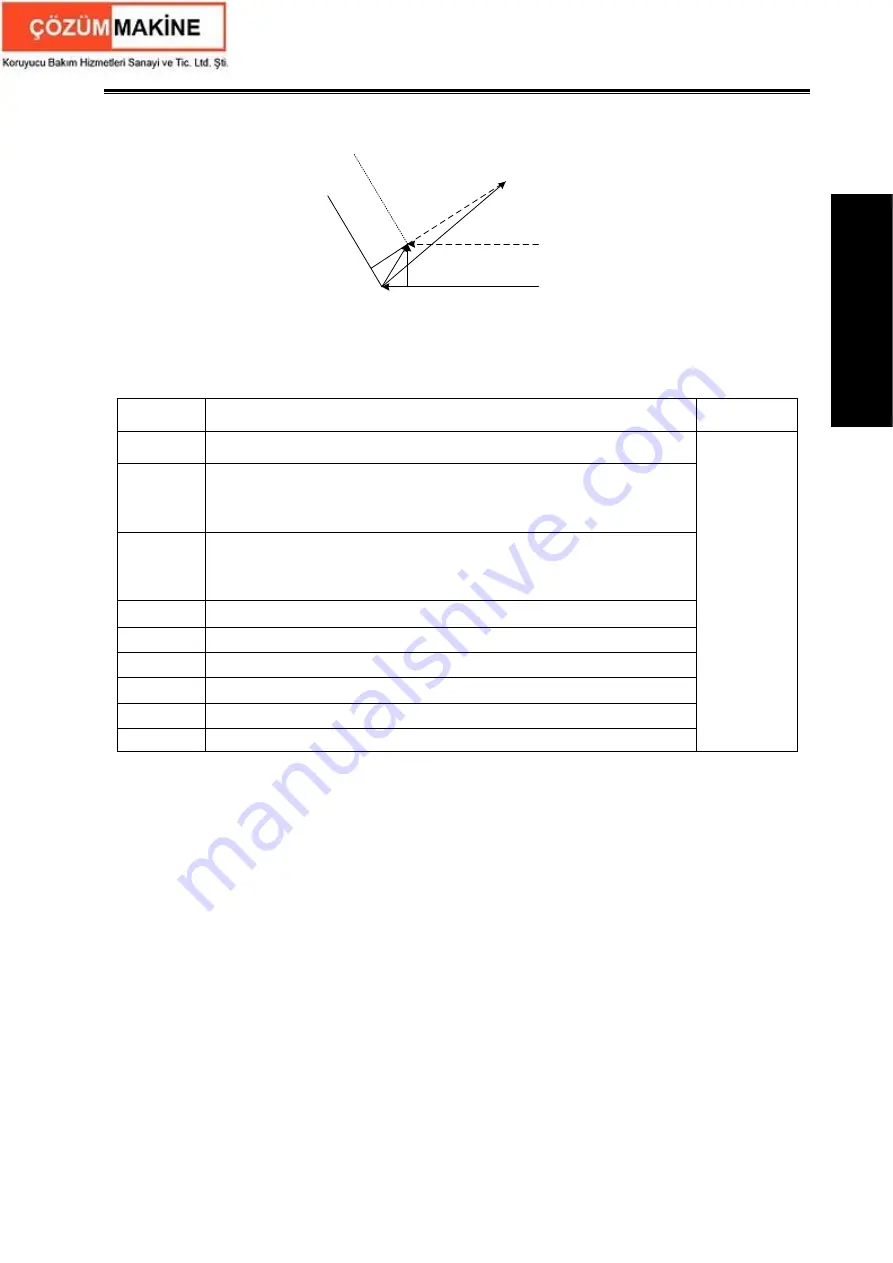
Chapter
Ⅳ
Tool Nose Radius Compensation
157
Ⅰ
Programming
Tool nose radius
center path
(
I,K
)
r
r
A
S
N2
N1
G42
G4
0
B(X,Z)
N1 G42 mode tool nose center moves to A point
N2 G40 Xp__ Zp__ I__ K__ tool nose center moves to B point
Fig. 4-11 G40 execution process
Command explanation:
Table 4-2
Commands Function
specifications
Remark
G40
Cancel the tool nose radius compensation
G41
Tool nose radius left compensation is specified by G41 in rear tool
post coordinate system and tool nose radius right compensation is
specified by G41 in front tool post coordinate system
G42
Tool nose radius right compensation is specified by G42 in rear tool
post coordinate system and tool nose radius left compensation is
specified by G42 in front tool post coordinate system
Xp
X and its parallel axis
Yp
Y and its parallel axis
Zp
Z and its parallel axis
I
X and the cancel vector (radius value) of its parallel axis
J
Y and the cancel vector (radius value) of its parallel axis
K
Z and the cancel vector (radius value) of its parallel axis
See Fig.4-11
and 4-12
4.1.5 Compensation direction
Specify its direction according to relative position between tool nose and workpiece when
executing tool nose radius compensation as Fig. 4-12 and Fig.4-13.
Summary of Contents for 988T
Page 6: ...GSK988T Turning CNC System User Manual VI ...
Page 14: ...GSK988T Turning CNC System User Manual XIV ...
Page 15: ...Chapter 1 Programming Fundamentals 1 Ⅰ Programming Ⅰ PROGRAMMING ...
Page 16: ...GSK988T Turning CNC System User Manual 2 Ⅰ Programming ...
Page 194: ...GSK988T Turning CNC System User Manual 180 Ⅰ Programming ...
Page 195: ...Chapter Ⅰ Overview 181 Ⅱ Operation Ⅱ OPERATION ...
Page 196: ...GSK988T Turning CNC System User Manual 182 Ⅱ Operation ...
Page 217: ...Chapter Ⅲ Windows 203 Ⅱ Operation ...
Page 267: ...Chapter Ⅲ Windows 253 Ⅱ Operation Fig 3 51 Fig 3 52 ...