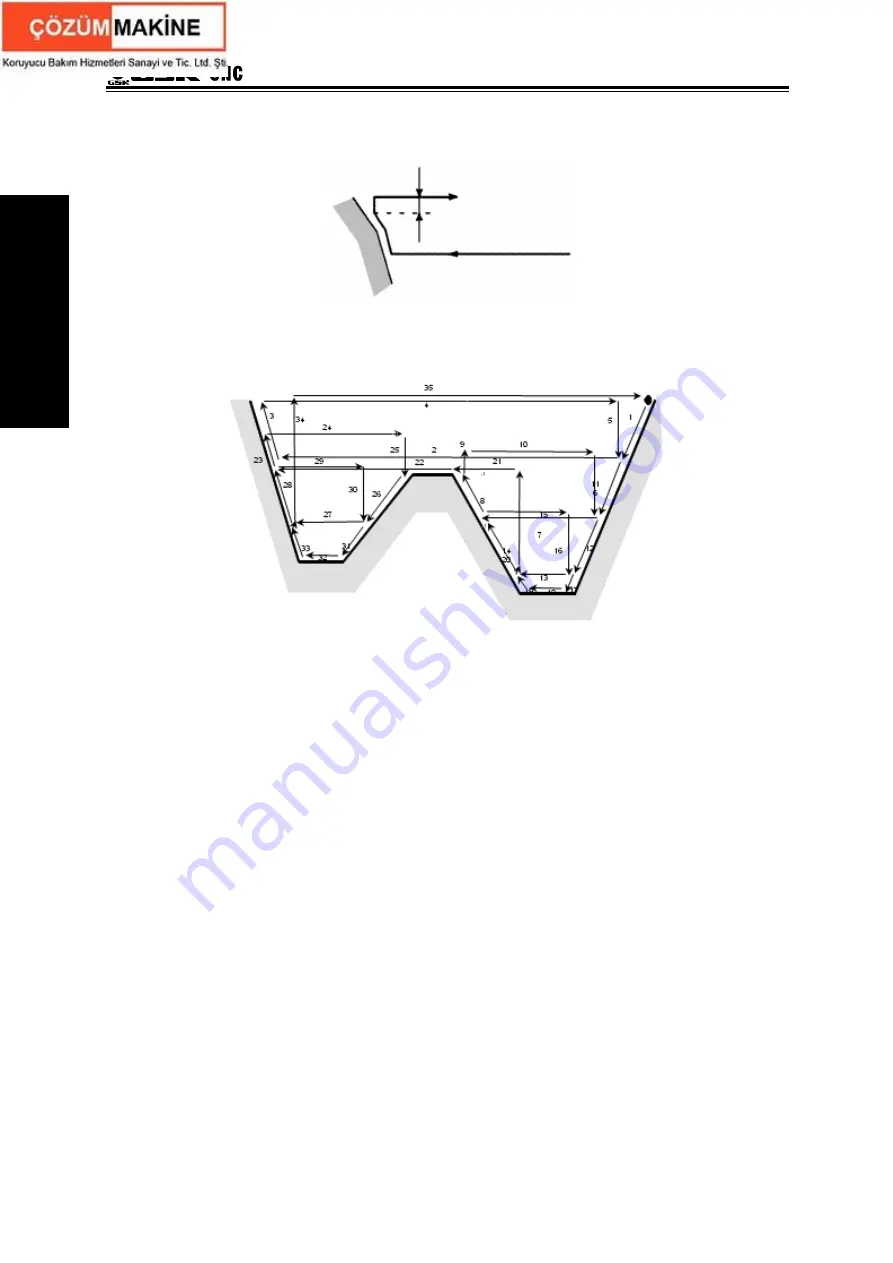
GSK988T Turning CNC System User Manual
72
Ⅰ
Programming
Fig. 2-42
Execution process sketch:
Fig. 2-43
Note 1: For grooving, X (U), Z(W) must be specified, and W0 is done when Z does not move.
Note 2: For grooving, the finishinig allowance is specified to X direction, is invalid for Z direction.
Note 3: For grooving, the tool retraction amount is left to make the tool approach the workpiece(Label 25,
26) with G1 speed after the current grooving is done to execute the next grooving. When the
retraction amount is 0 or the left distance is less than retraction amount, the tool approaches the
workpiece with G1 speed.
Note 4: For grooving, the finishing path (ns
~
nf block), Z dimension must mononously change (always
increase or decrease)
Note 5: For G71 II type, when there is arc in finishing path (ns
~
nf), # 3410 parameter (the arc radius
permits error) cannot be non-zero, i.e., the permitting function of arc radius error cannot be
activated.
Note 6: Radius error is irrelevant to cutting allowance, and radius error is permitted and checks whether
the alarm occurs.
2.15.2 Radial Roughing Cycle G72
Command function
:
G72 is divided into three parts:
⑴
1st blocks for defining the travels of tool infeed and tool retraction, the cutting speed, the
spindle speed and the tool function in roughing;
e
(
set by a parameter
)
Summary of Contents for 988T
Page 6: ...GSK988T Turning CNC System User Manual VI ...
Page 14: ...GSK988T Turning CNC System User Manual XIV ...
Page 15: ...Chapter 1 Programming Fundamentals 1 Ⅰ Programming Ⅰ PROGRAMMING ...
Page 16: ...GSK988T Turning CNC System User Manual 2 Ⅰ Programming ...
Page 194: ...GSK988T Turning CNC System User Manual 180 Ⅰ Programming ...
Page 195: ...Chapter Ⅰ Overview 181 Ⅱ Operation Ⅱ OPERATION ...
Page 196: ...GSK988T Turning CNC System User Manual 182 Ⅱ Operation ...
Page 217: ...Chapter Ⅲ Windows 203 Ⅱ Operation ...
Page 267: ...Chapter Ⅲ Windows 253 Ⅱ Operation Fig 3 51 Fig 3 52 ...