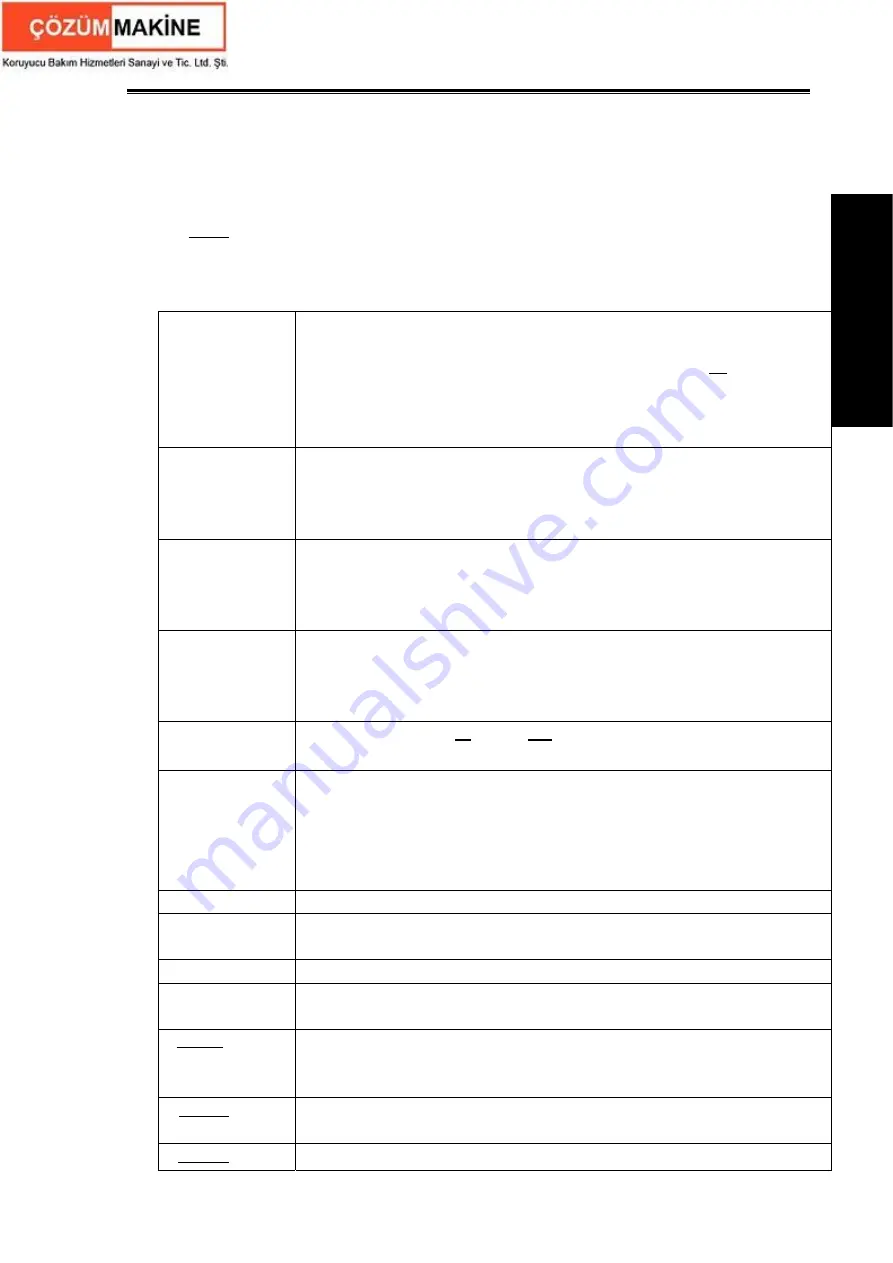
Chapter
Ⅱ
G Commands
87
Ⅰ
Programming
3. The tool can stop in Auto mode and traverse in Manual mode when G75 is executed, but
the tool must return to the position before executing in Manual mode when G75 is
executed again, otherwise the following path will be wrong;
4. When the system is executing the single block, the program pauses after the system has
executed end point of current path;
5. R
(
Δ
d
)
must be omitted in grooving, and so there is no travel of tool retraction when the tool
cuts to radial cutting end point.
Relevant definitions
:
Starting point of
radial cutting cycle
Starting position of axial tool infeed for each radial cutting cycle, defined by
A
n
(n=1,2,3……),X coordinate of A
n
is the same that of starting point A,
the
different value of X coordinate between A
n
and A
n-1
is
Δ
k. The starting
point A
1
of the first radial cutting cycle is the same as the starting point A,
and Z starting point (A
f
) of the last axial cutting cycle is the same that of
cutting end point.
End point of radial
tool infeed
Starting position of radial tool infeed for each radial cutting cycle, defined
by B
n
(n=1,2,3……), X coordinates of B
n
is the same that of cutting end
point,
Z coordinates of B
n
is the same that of A
n
, and the end point (B
f
) of
the last radial tool infeed is the same that of cutting end point.
End point of axial
tool retraction
End
position of axial tool infeed(travel of tool infeed is
Δ
d) after each axial
cutting cycle reaches the end point of axial tool infeed, defining with
C
n
(n=1,2,3……), X coordinate of C
n
is the same that of cutting end point,
and the different value of Z coordinate between C
n
and A
n
is
Δ
d.
End point of
radial cutting
cycle
End
position of radial tool retraction from the end point of axial tool
retraction, defined by D
n
(n=1,2,3……), X coordinate of D
n
is the same that
of starting point, Z coordinates of D
n
is the same that of C
n
(the different
value of Z coordinate between it and A
n
is
Δ
d).
Cutting end point It is defined by X
(
U
)
Z
(
W
)
,and is defined with B
f
of the last radial
tool infeed.
R
(
e
)
It is the travel of tool retraction after each radial(X) tool infeed without sign
symbols and its value range is referred to the following table. The
command value is reserved and the value of system parameter NO.5139 is
rewritten after R
(
e
)
is executed. The value of NO.5139 is regarded as the
travel of tool retraction when R
(
e
)
is not input.
X
X absolute coordinate value of cutting end point B
f
(unit: mm).
U
Different value of X absolute coordinate between cutting end point B
f
and
starting point.
Z
Z absolute coordinate value of cutting end point B
f
(unit: mm).
W
Different value of Z absolute coordinate between cutting end point B
f
and
starting point.
P
(
Δ
i
)
It is the travel(diameter value) of radial(X) discontinuous tool infeed for
each axial cutting cycle without sign symbols and its value range is referred
to the following table.
Q
(
Δ
k
)
It is the travel of Z discontinuous tool infeed without sign symbols of the
axial(Z) cutting, and the value range is referred to the following table.
R
(
Δ
d
)
It is the travel of axial (Z) tool retraction after cutting to end point of radial
Summary of Contents for 988T
Page 6: ...GSK988T Turning CNC System User Manual VI ...
Page 14: ...GSK988T Turning CNC System User Manual XIV ...
Page 15: ...Chapter 1 Programming Fundamentals 1 Ⅰ Programming Ⅰ PROGRAMMING ...
Page 16: ...GSK988T Turning CNC System User Manual 2 Ⅰ Programming ...
Page 194: ...GSK988T Turning CNC System User Manual 180 Ⅰ Programming ...
Page 195: ...Chapter Ⅰ Overview 181 Ⅱ Operation Ⅱ OPERATION ...
Page 196: ...GSK988T Turning CNC System User Manual 182 Ⅱ Operation ...
Page 217: ...Chapter Ⅲ Windows 203 Ⅱ Operation ...
Page 267: ...Chapter Ⅲ Windows 253 Ⅱ Operation Fig 3 51 Fig 3 52 ...