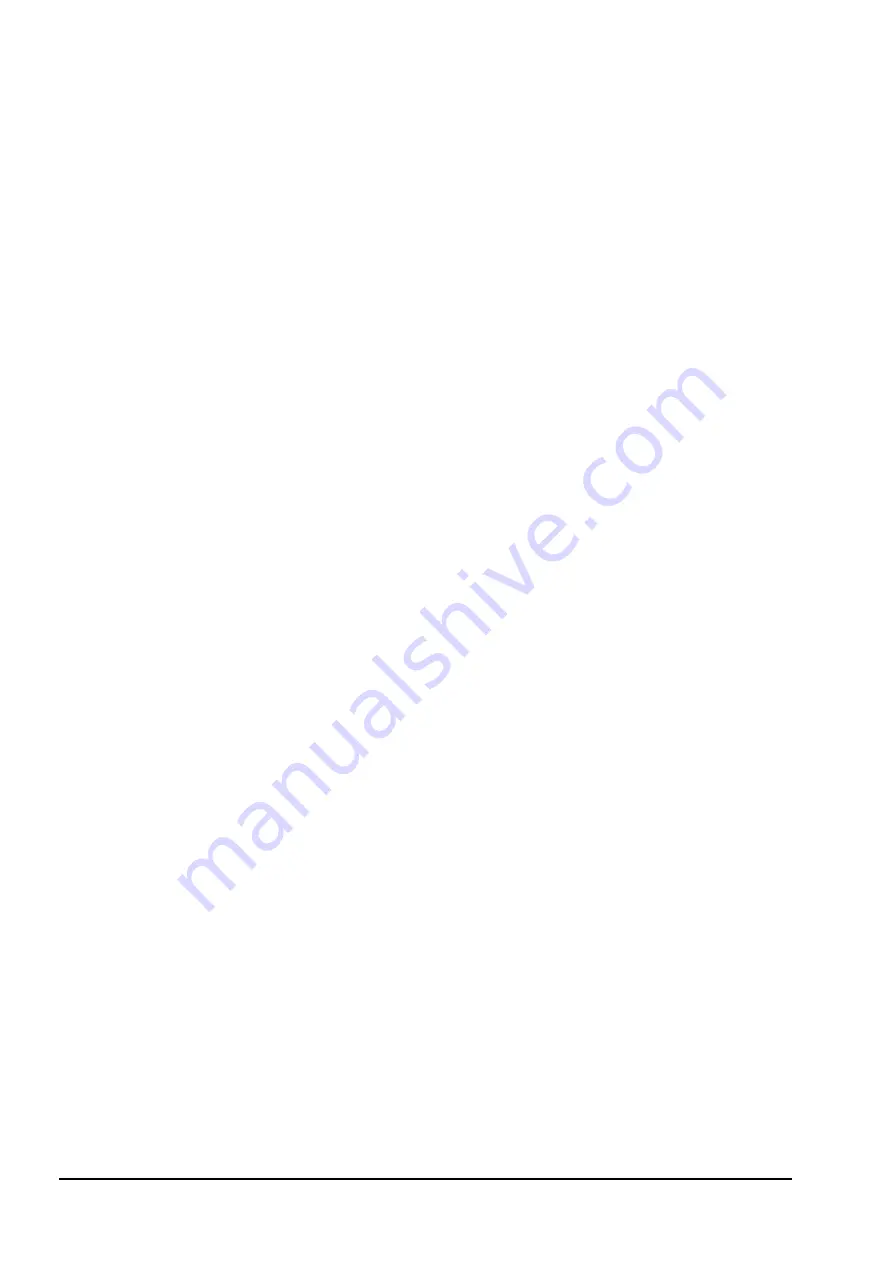
SECTION 10A
PUMPS
Page 16
TD-25M EXTRA
DRESSTA
EQUIPMENT PUMP
8. INSPECTION AND REPAIR (Refer to Fig. 10A.7)
NOTE: All parts must be thoroughly cleaned and kept clean during inspection and assembly. The
close tolerance of the parts makes this requirement very important. Clean all removed parts using
a commercial solvent that is compatible with the system oil. Compressed air may be used in
cleaning but it must be filtered to remove water and contamination.
1. Discard the shaft seals (36), seal rings (5 and 28), O-rings (4, 6 and 27, 29 and 40, 49),
back-up rings (3 and 30), wear plates (46, 48) and seal packs (8 and 21) subassemblies. Use
a new seal kit for reassembly. Wash the metal parts, blow them dry with air and place on
a clean surface for inspection.
2. Check the pumping cartridges wear surfaces for pickup, scoring and excessive wear. Slight
heat discoloration of the flex side plates (9 and 22) bronze surface is normal. Score marks
deeper than 0.025 [mm] and scratches deeper than 0.05 [mm] indicate a new part is needed.
Slight scoring and/or scratches can be removed with an oiled “Arkansas” stone.
NOTE: DO NOT use a dry stone on the bronze surface or scratches will result.
3. Inspect both sides of each vane and insert in order. If pickup, heavy wear or scoring is found,
inspect the appropriate rotors (10, 23 and 41) slot. Replace scored parts.
4. Inspect rotor rings (12, 25 and 43) for vane chatter marks, wear and/or scratches. Replace if
scoring is evident.
NOTE:
Replacement rotor rings (12, 25 and 43) width must be identical to the ring being replaced
or reduced life and/or output flow will result. The minimum rotor ring (12, 25 or 43) to rotor (10, 23
or 41) clearance limits is 0.03 [mm].
NOTE: All pumping cartridge (A, B and C) parts must be free of burrs. Stone the mating surfaces
of each part with an oiled “Arkansas” stone prior to assembly.
NOTE: Pre-assembled replacement cartridge kits are available. If the old cartridge is worn
extensively, a new kit should be used.
5. Vane and rotors (10, 23 and 41) wear can be checked by inserting the vane in the rotor slot
and checking for excessive play. Replace rotor (10, 23 or 41) and vane kit (11, 24 or 42) if wear
is evident.
6. Rotate ball bearing (33) while applying pressure to check for wear, looseness and pitted or
cracked races.
7. Inspect seal and bushing mating surfaces on drive shaft (34) for scoring or wear. Replace the
shaft if marks cannot be removed by light polishing.
Summary of Contents for TD-25M EXTRA
Page 1: ...SMTD25MEX07 1E SERVICE MANUAL TD 25M EXTRA SERIAL NUMBERS 75001 AND UP DRESSTA ...
Page 2: ......
Page 4: ......
Page 5: ...SECTION 1 INTRODUCTION ...
Page 6: ......
Page 8: ......
Page 25: ...SECTION 5 STEERING ...
Page 26: ......
Page 27: ...STEERING SECTION 5 DRESSTA TD 25M EXTRA CONTENTS GENERAL 1 DESCRIPTION 1 ...
Page 28: ......
Page 30: ......
Page 31: ...SECTION 6 COOLING SYSTEM ...
Page 32: ......
Page 34: ......
Page 49: ...SECTION 7 DRIVE TRAIN ...
Page 50: ......
Page 52: ......
Page 60: ......
Page 62: ......
Page 83: ...SECTION 7B HYDRAULIC TORQUE CONVERTER ...
Page 84: ......
Page 86: ......
Page 115: ...SECTION 7C TRANSMISSION ...
Page 116: ......
Page 208: ......
Page 209: ...SECTION 7E STEERING DRIVE ...
Page 210: ......
Page 212: ......
Page 251: ...SECTION 7F FINAL DRIVE ...
Page 252: ......
Page 254: ......
Page 272: ......
Page 273: ...SECTION 8 ELECTRICAL ...
Page 274: ......
Page 276: ......
Page 283: ...ELECTRICAL SECTION 8 Page 7 DRESSTA TD 25M EXTRA Fig 8 1 Wiring Diagram earlier version ...
Page 284: ......
Page 285: ......
Page 286: ...SECTION 8 Page 10 ELECTRICAL TD 25M EXTRA DRESSTA Fig 8 1A Wiring Diagram later version ...
Page 331: ...SECTION 9 FRAME ...
Page 332: ......
Page 334: ......
Page 336: ...SECTION 9 FRAME Page 2 TD 25M EXTRA DRESSTA GENERAL Fig 9 2 View of Frame ...
Page 339: ...SECTION 10 HYDRAULICS ...
Page 340: ......
Page 342: ......
Page 363: ...SECTION 10A PUMPS ...
Page 364: ......
Page 366: ......
Page 387: ...SECTION 10B VALVES ...
Page 388: ......
Page 390: ......
Page 412: ......
Page 413: ...SECTION 10C CYLINDERS ...
Page 414: ......
Page 416: ......
Page 449: ...SECTION 10E RESERVOIRS AND FILTERS ...
Page 450: ......
Page 452: ......
Page 459: ...SECTION 12 POWER ...
Page 460: ......
Page 462: ......
Page 478: ......
Page 479: ...SECTION 13 SUPERSTRUCTURE ...
Page 480: ......
Page 482: ......
Page 491: ...SECTION 14 SUSPENSION ...
Page 492: ......
Page 542: ......
Page 543: ...SECTION 15 TRACK OR WHEELS ...
Page 544: ......
Page 546: ......
Page 565: ...SECTION 17 MOUNTED EQUIPMENT ...
Page 566: ......
Page 568: ......