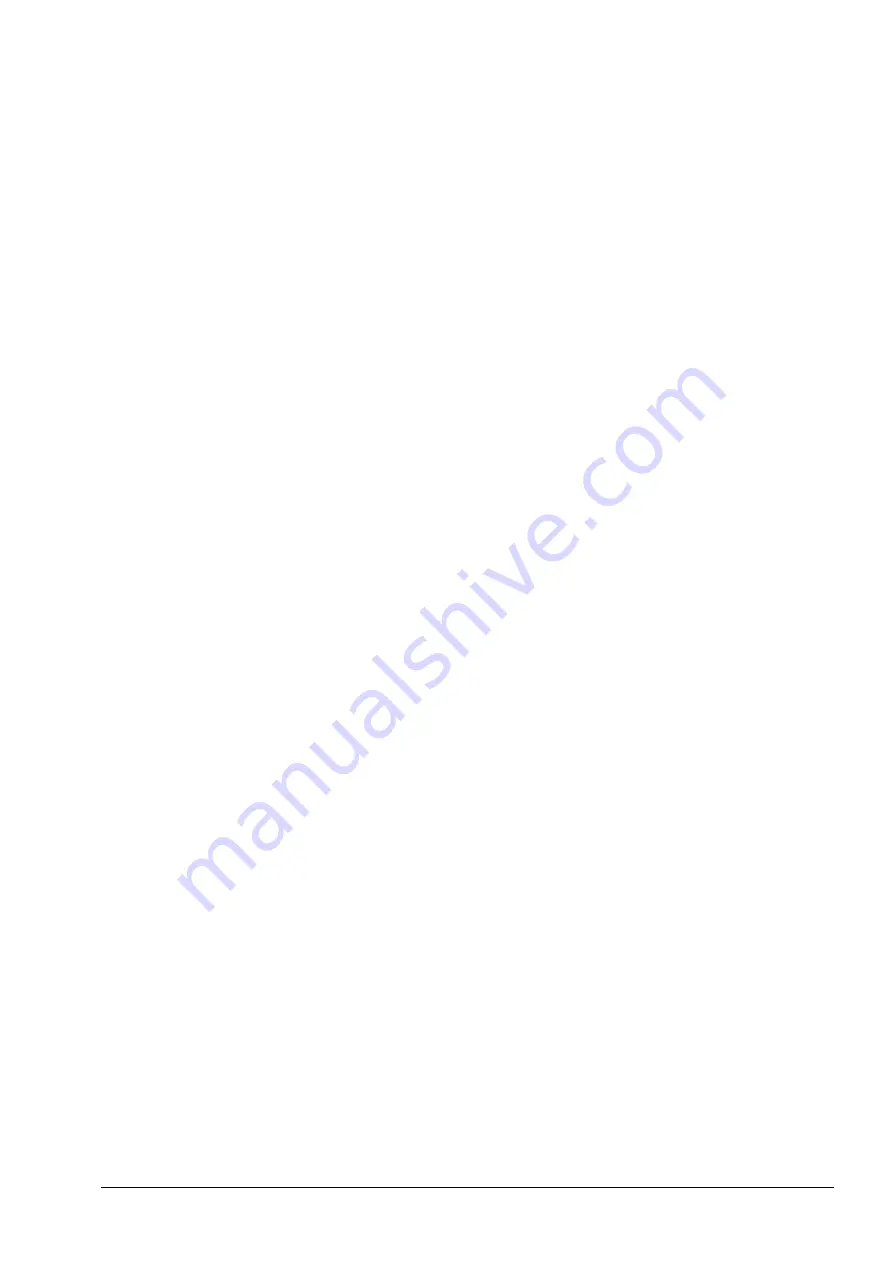
HYDRAULICS
SECTION 10
Page 17
DRESSTA
TD-25M EXTRA
TEST AND ADJUSTMENT
Legend for Fig. 10.10
1. Ripper Lift Cylinder
2. Ripper Pitch Cylinder
3. Blade Lift Cylinder
4. Quick Drop Valve
5. Three Spool Control Valve
6. Blade Pilot Valve
7. Ripper Pilot Valve
8. Directional Valve
9. Shuttle Valves
10. Unloading Valve
11. Blade Tilt/Pitch Cylinder
12. Blade Tilt Control Valve
13. Hydraulic Pump Assy
14. Hydraulic Reservoir
14A. Suction Strainer
15. Breather Valve
16. Return Filters
17. Pilot Pressure Filter
18. Pilot Pressure Valve
19. Double Tilt /Pitch Solenoid Valve
20. Blade Double Tilt/Pitch Cylinder
21. Pin Puller Valve
22. Pin Puller Cylinder
A. Oil Supply from Pressure Regulator Valve
M
Port Located at Steering Valve
B. Drain to Rear Frame
8. If ripper cylinders drift is more than 16 [mm] per minute and blade cylinders drift is more than
18 [mm] per minute lower the blade and ripper and follow below mentioned procedure. Refer to
HYDRAULIC CHART Fig. 10.10.
9. Plug blade pilot control valve (6) at point
P
. If cylinders drift is much less than checked in point
4 or 7, blade pilot control valve is faulty. Repair or replace the valve. Refer to BLADE PILOT
CONTROL VALVE in SECTION 10B. If cylinders drift is still the same proceed to next point.
10. Plug ripper pilot control valve (7) at point
P
. If cylinders drift is much less than checked in point
4 or 7, ripper pilot control valve is faulty. Repair or replace the valve. Refer to RIPPER PILOT
CONTROL VALVE in SECTION 10B. If cylinders drift is still the same, pilot pressure valve is
faulty. Repair or replace the valve. Refer to PILOT PRESSURE VALVE in SECTION 10B.
11. When proceeding tests are completed, vent hydraulic system and add oil as necessary. Refer
to the OPERATOR’S MANUAL. Visually check for oil leakage.
7B. RIPPER LIFT CYLINDERS DRIFT TEST
/BLADE LIFT CYLINDERS ARE NOT DROPPING/
There are two places that might be a source of leakage; one of hydraulic cylinder could leak post
piston packing and second of control valve could leak at its spool.
Following is a test to trace the source of internal leakage.
1. Raise and lower ripper and blade through its full travel. Oil temperature should be 82 - 88 [°C].
2. Lower the blade to the ground.
3. Fully lower the ripper to raise the rear of machine up.
4. Slightly move the lever to LOWER position releasing it to HOLD before machine drops to
ground.
5. Perform ripper lift cylinders drift test. Check cylinders for drift, rods should travel out of cylinders
no more than 16 [mm] per minute.
6. If ripper cylinders drift is less than 16 [mm] per minute one of cylinders is leaking. Proceed to
PISTON PACKING TEST in this SECTION to find which one is foulty.
7. If ripper cylinders drift is more than 16 [mm] per minute control valve spool is leaking. Proceed to
CONTROL VALVE in SECTION 10B.
8. When proceeding tests are completed, vent hydraulic system and add oil as necessary. Refer to
the OPERATOR’S MANUAL. Visually check for oil leakage.
Summary of Contents for TD-25M EXTRA
Page 1: ...SMTD25MEX07 1E SERVICE MANUAL TD 25M EXTRA SERIAL NUMBERS 75001 AND UP DRESSTA ...
Page 2: ......
Page 4: ......
Page 5: ...SECTION 1 INTRODUCTION ...
Page 6: ......
Page 8: ......
Page 25: ...SECTION 5 STEERING ...
Page 26: ......
Page 27: ...STEERING SECTION 5 DRESSTA TD 25M EXTRA CONTENTS GENERAL 1 DESCRIPTION 1 ...
Page 28: ......
Page 30: ......
Page 31: ...SECTION 6 COOLING SYSTEM ...
Page 32: ......
Page 34: ......
Page 49: ...SECTION 7 DRIVE TRAIN ...
Page 50: ......
Page 52: ......
Page 60: ......
Page 62: ......
Page 83: ...SECTION 7B HYDRAULIC TORQUE CONVERTER ...
Page 84: ......
Page 86: ......
Page 115: ...SECTION 7C TRANSMISSION ...
Page 116: ......
Page 208: ......
Page 209: ...SECTION 7E STEERING DRIVE ...
Page 210: ......
Page 212: ......
Page 251: ...SECTION 7F FINAL DRIVE ...
Page 252: ......
Page 254: ......
Page 272: ......
Page 273: ...SECTION 8 ELECTRICAL ...
Page 274: ......
Page 276: ......
Page 283: ...ELECTRICAL SECTION 8 Page 7 DRESSTA TD 25M EXTRA Fig 8 1 Wiring Diagram earlier version ...
Page 284: ......
Page 285: ......
Page 286: ...SECTION 8 Page 10 ELECTRICAL TD 25M EXTRA DRESSTA Fig 8 1A Wiring Diagram later version ...
Page 331: ...SECTION 9 FRAME ...
Page 332: ......
Page 334: ......
Page 336: ...SECTION 9 FRAME Page 2 TD 25M EXTRA DRESSTA GENERAL Fig 9 2 View of Frame ...
Page 339: ...SECTION 10 HYDRAULICS ...
Page 340: ......
Page 342: ......
Page 363: ...SECTION 10A PUMPS ...
Page 364: ......
Page 366: ......
Page 387: ...SECTION 10B VALVES ...
Page 388: ......
Page 390: ......
Page 412: ......
Page 413: ...SECTION 10C CYLINDERS ...
Page 414: ......
Page 416: ......
Page 449: ...SECTION 10E RESERVOIRS AND FILTERS ...
Page 450: ......
Page 452: ......
Page 459: ...SECTION 12 POWER ...
Page 460: ......
Page 462: ......
Page 478: ......
Page 479: ...SECTION 13 SUPERSTRUCTURE ...
Page 480: ......
Page 482: ......
Page 491: ...SECTION 14 SUSPENSION ...
Page 492: ......
Page 542: ......
Page 543: ...SECTION 15 TRACK OR WHEELS ...
Page 544: ......
Page 546: ......
Page 565: ...SECTION 17 MOUNTED EQUIPMENT ...
Page 566: ......
Page 568: ......