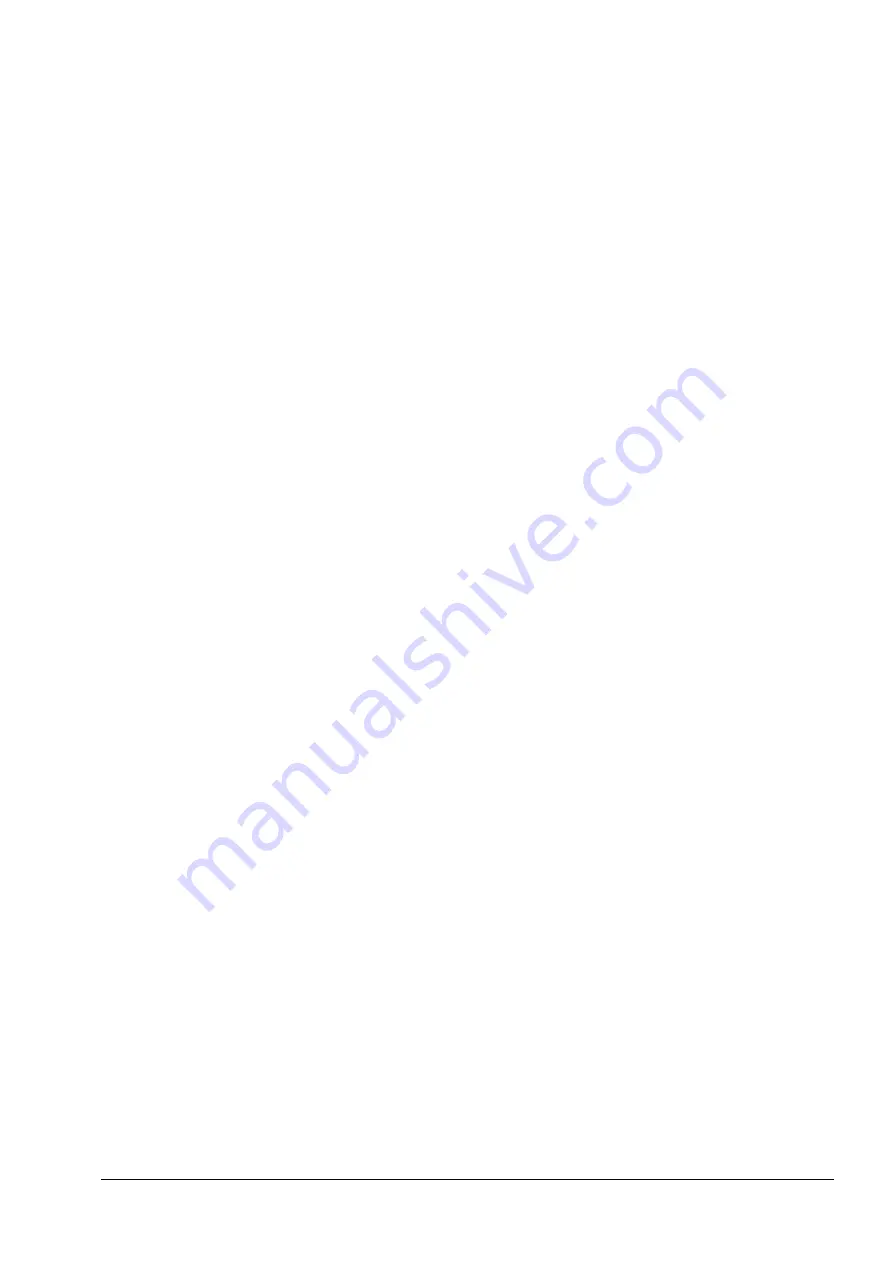
DRIVE TRAIN
SECTION 7
Page 3
DRESSTA
TD-25M EXTRA
OPERATION
When the control lever is moved forward, the pivot ring depresses the Forward direction spool
directing oil to the “F” port at the bottom of the valve. The “F” pressurized oil is also directed
internally to the base of the Reverse spool which pushes the Reverse spool up to the pivot ring.
This action creates a hydraulic detent holding the lever forward.
When pulling the control lever to neutral or reverse, the pivot ring pushes down on the Reverse
spool which displaces the hydraulic detent oil. At the same time the Forward spool follows the pivot
ring up and mid way through its stroke the forward pressure is cut off as well as the reverse
hydraulic detent, allowing the valve to go into neutral. If the lever is pulled all the way to reverse the
same sequence of events happens for the reverse hydraulic detent.
Steering is accomplished in two ways: by moving the control lever to the left or right or by shifting
the HI-LO speed range switches. The two steering methods can be used together and in any
combination.
When the machine is started with both speed range switches in LO-LO positions both tracks are
in LO-LO. With the lever pushed to forward the machine travels in FWD, LO-LO (both tracks
in LO-LO). Initial movement of the lever to the right drops right LO clutch steering pressure causing
the right steering clutch to be in a neutral condition. The neutral condition is indicated by a “feel
point” or effort increase in the control lever movement. Further movement of the lever further
decreases pressure at the right brake, which is moved to the end of the lever stroke will result in a
pivot turn to the right. By shifting both range switches to their upper position both tracks shift up to
HI-HI (both tracks in HI-HI). If traveling in HI-HI and the lever is pulled to the right the following
occurs. The initial lever movement lowers signal pressure causing a sequence valve to
automatically shift the right track from HI to LO. With further lever travel to the right the right LO
track will go to the neutral condition as indicated by the “feel point” as discussed earlier. Further
lever movement will result in a pivot turn. As the lever is moved back to the upright position the LO
clutch engages and then up into HI. Speed range switch steering results in full power turns.
With the lever pushed to forward and both speed range switches in LO-LO positions the machine
travels in FWD, LO-LO (both tracks in LO-LO). By shifting the right switch to HI position, the right
track shifts up to HI. Both machine tracks are engaged, while the right track features the higher
speed and, as a result, the machine will make a gradual turn to the left. To cause the machine to
make a gradual turn to the right proceed in similar manner by controlling the left hand track power.
The machine will make a gradual turn so long as one of the speed range switches gets reactivated.
Then the machine will revert to straight travel in a range it was engaged in prior to the gradual turn
activation.
A transmission range gear is selected by pushing the drive train control lever up-shift and
down-shift buttons.
For a complete Machine Speed and Direction Changes description and operation, refer to
OPERATOR’S MANUAL.
Two Speed Steering Valve (Fig.’s 7.4, 7.5 and 7.6)
The two speed steering valve contains three valves. Two of them: upper LC, RC, FB and lower
HI-LO are mounted above rear main frame cover and one - manifold J under this cover.
The upper valve
consists of three basic sections: LC left clutch section, RC right clutch section
and the FB foot brake section.
The LC and RC clutch sections control the flow of oil to the clutch packs to drive each track
individually. Both of the sections contain a metering spools which are each held in the rear drive
position by pilot pressure CL and CR respectively from the drive train control valve.
Summary of Contents for TD-25M EXTRA
Page 1: ...SMTD25MEX07 1E SERVICE MANUAL TD 25M EXTRA SERIAL NUMBERS 75001 AND UP DRESSTA ...
Page 2: ......
Page 4: ......
Page 5: ...SECTION 1 INTRODUCTION ...
Page 6: ......
Page 8: ......
Page 25: ...SECTION 5 STEERING ...
Page 26: ......
Page 27: ...STEERING SECTION 5 DRESSTA TD 25M EXTRA CONTENTS GENERAL 1 DESCRIPTION 1 ...
Page 28: ......
Page 30: ......
Page 31: ...SECTION 6 COOLING SYSTEM ...
Page 32: ......
Page 34: ......
Page 49: ...SECTION 7 DRIVE TRAIN ...
Page 50: ......
Page 52: ......
Page 60: ......
Page 62: ......
Page 83: ...SECTION 7B HYDRAULIC TORQUE CONVERTER ...
Page 84: ......
Page 86: ......
Page 115: ...SECTION 7C TRANSMISSION ...
Page 116: ......
Page 208: ......
Page 209: ...SECTION 7E STEERING DRIVE ...
Page 210: ......
Page 212: ......
Page 251: ...SECTION 7F FINAL DRIVE ...
Page 252: ......
Page 254: ......
Page 272: ......
Page 273: ...SECTION 8 ELECTRICAL ...
Page 274: ......
Page 276: ......
Page 283: ...ELECTRICAL SECTION 8 Page 7 DRESSTA TD 25M EXTRA Fig 8 1 Wiring Diagram earlier version ...
Page 284: ......
Page 285: ......
Page 286: ...SECTION 8 Page 10 ELECTRICAL TD 25M EXTRA DRESSTA Fig 8 1A Wiring Diagram later version ...
Page 331: ...SECTION 9 FRAME ...
Page 332: ......
Page 334: ......
Page 336: ...SECTION 9 FRAME Page 2 TD 25M EXTRA DRESSTA GENERAL Fig 9 2 View of Frame ...
Page 339: ...SECTION 10 HYDRAULICS ...
Page 340: ......
Page 342: ......
Page 363: ...SECTION 10A PUMPS ...
Page 364: ......
Page 366: ......
Page 387: ...SECTION 10B VALVES ...
Page 388: ......
Page 390: ......
Page 412: ......
Page 413: ...SECTION 10C CYLINDERS ...
Page 414: ......
Page 416: ......
Page 449: ...SECTION 10E RESERVOIRS AND FILTERS ...
Page 450: ......
Page 452: ......
Page 459: ...SECTION 12 POWER ...
Page 460: ......
Page 462: ......
Page 478: ......
Page 479: ...SECTION 13 SUPERSTRUCTURE ...
Page 480: ......
Page 482: ......
Page 491: ...SECTION 14 SUSPENSION ...
Page 492: ......
Page 542: ......
Page 543: ...SECTION 15 TRACK OR WHEELS ...
Page 544: ......
Page 546: ......
Page 565: ...SECTION 17 MOUNTED EQUIPMENT ...
Page 566: ......
Page 568: ......