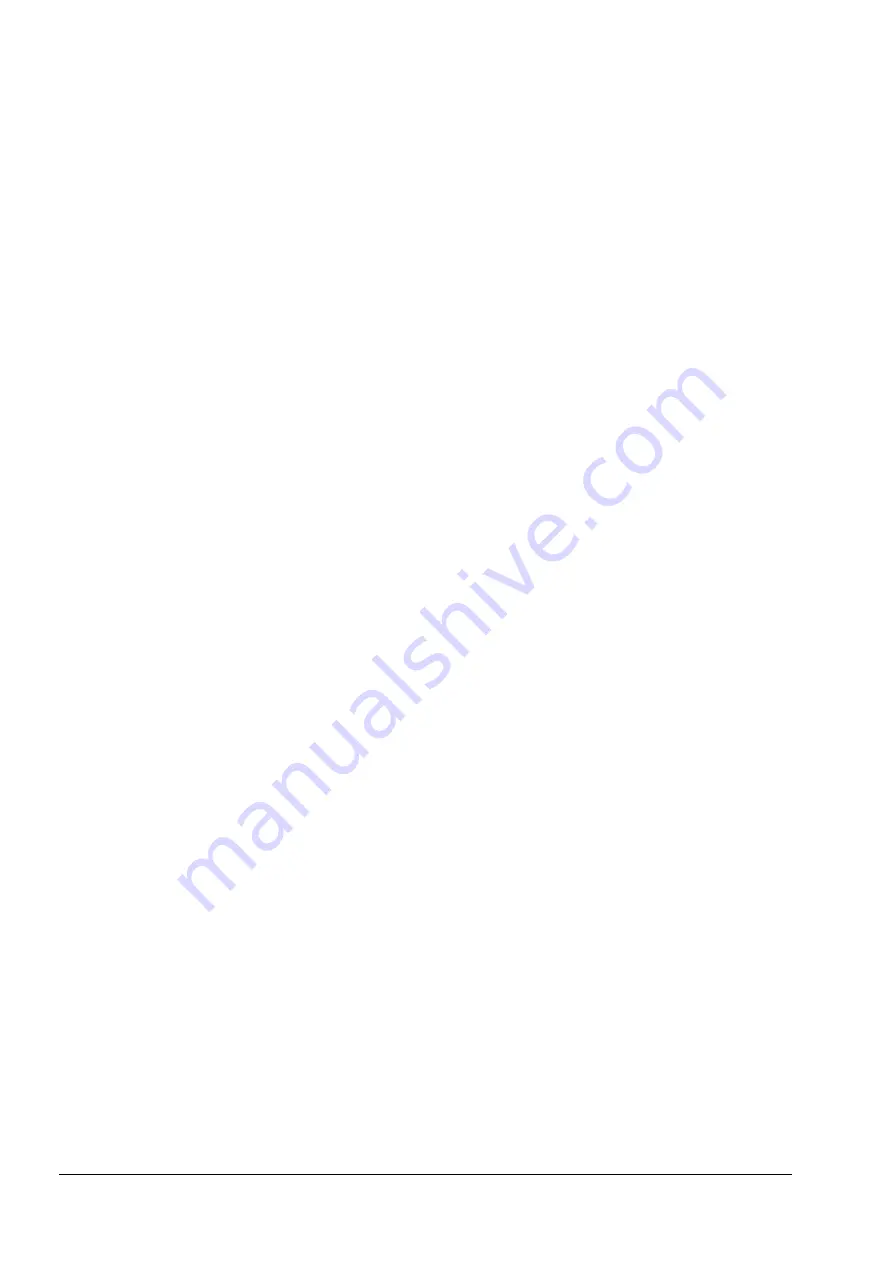
SUSPENSION
SECTION 14
Page 19
DRESSTA
TD-25M EXTRA
TOP IDLER
2. Check the bearing bores in the idler housing for scoring or other evidence of bearings turning in
their bores. Inspect for cracks or other damage. Inspect the idler shaft for excessive wear or
damage. Replace shaft if necessary. Slight burrs can be smoothed down with a stone.
3. Replace all O-rings with new.
4. It is recommended that new seal kit (11) be installed whenever the top idler is disassembled.
Refer to SEAL INSPECTION under METAL TYPE FACE SEALS in this Section.
22. REASSEMBLY (FIG. 14.21)
NOTE: To ease assembly, apply a small amount of oil, same as used to fill idler, to bearing cup
bores of housing (7) and bearing cone diameters of shaft (6) prior to bearing installation.
1. If bearing replacement was necessary press new bearing cups (5 and 8) into idler housing (7)
until they bottom in bore. If bearing cone (8) was removed, press cone into shaft (6) until it
is against shaft shoulder.
2. Insert shaft in idler housing (7) and position assembly in a hydraulic press so that it is supported
by shaft (6). Press bearing cone (5) onto shaft (6). Install retaining ring (4). With assembly still
supported by shaft (6), rotate idler housing. If it does not turn freely, tap end of shaft with
a brass mallet to set bearings.
3. Install bearing spacer (9) on shaft (6) and into housing (7). Place assembly on a bench, cover
plate end down. Apply a thin coating of grease to O-ring (10) and install it in retainer (12).
NOTE: Do not at any time handle seal kit
(11) with greasy, oily or dirty hands. Track idler must not
be filled with lubricant until idler and track frame are in position on machine.
4. Before installing seal assembly, be sure seal contacting surfaces of idler housing bore and seal
retainer are clean. Also that rubber rings of seal assembly are correctly positioned on metal
rings. Install seal. Refer to SEAL INSTALLATION under METAL TYPE FACE SEALS in this
Section.
5. Install seal retainer (12) on shaft (6) so that seal bore of retainer uniformly envelops oil seal
rubber ring. Position seal retainer (12) so spring pin (13) holes in shaft (6) and retainer are
aligned. Install pin (13) into retainer (12) and peen over metal area around pin hole. Install cover
(2) with O-ring (3) on top idler assembly. Torque cover bolts to 35 [Nm].
6. Fill idler with recommended lubricant. Refer to OPERATOR'S MANUAL for recommended
lubricant. Clean threads of plug (1) and apply LOCTITE Pipe Sealant with Teflon #592. Install
plug in cover (2) and torque to 20 - 50 [Nm].
23. INSTALLATION
1. Spread block of the track frame bracket with a chisel and slide the top track idler shaft into
top idler block (2, Fig. 14.20) so that spring pin (13, Fig. 14.21) is in a horizontal position.
Align track idler with front idler and other track idler as described in Paragraph 51,
TRACK FRAME ALIGNMENT, in this Section. Remove chisel from top idler block and secure
block to the track frame bracket. For the first torque the bolts (1, Fig. 14.20) located closer to the
dozer centerline (two bolts for each top idler mounting block) and then torque the others. Torque
bolts to 845 [Nm].
2. Lower track chain onto idlers and remove jack. Adjust track chain tension, refer to SECTION 15.
Summary of Contents for TD-25M EXTRA
Page 1: ...SMTD25MEX07 1E SERVICE MANUAL TD 25M EXTRA SERIAL NUMBERS 75001 AND UP DRESSTA ...
Page 2: ......
Page 4: ......
Page 5: ...SECTION 1 INTRODUCTION ...
Page 6: ......
Page 8: ......
Page 25: ...SECTION 5 STEERING ...
Page 26: ......
Page 27: ...STEERING SECTION 5 DRESSTA TD 25M EXTRA CONTENTS GENERAL 1 DESCRIPTION 1 ...
Page 28: ......
Page 30: ......
Page 31: ...SECTION 6 COOLING SYSTEM ...
Page 32: ......
Page 34: ......
Page 49: ...SECTION 7 DRIVE TRAIN ...
Page 50: ......
Page 52: ......
Page 60: ......
Page 62: ......
Page 83: ...SECTION 7B HYDRAULIC TORQUE CONVERTER ...
Page 84: ......
Page 86: ......
Page 115: ...SECTION 7C TRANSMISSION ...
Page 116: ......
Page 208: ......
Page 209: ...SECTION 7E STEERING DRIVE ...
Page 210: ......
Page 212: ......
Page 251: ...SECTION 7F FINAL DRIVE ...
Page 252: ......
Page 254: ......
Page 272: ......
Page 273: ...SECTION 8 ELECTRICAL ...
Page 274: ......
Page 276: ......
Page 283: ...ELECTRICAL SECTION 8 Page 7 DRESSTA TD 25M EXTRA Fig 8 1 Wiring Diagram earlier version ...
Page 284: ......
Page 285: ......
Page 286: ...SECTION 8 Page 10 ELECTRICAL TD 25M EXTRA DRESSTA Fig 8 1A Wiring Diagram later version ...
Page 331: ...SECTION 9 FRAME ...
Page 332: ......
Page 334: ......
Page 336: ...SECTION 9 FRAME Page 2 TD 25M EXTRA DRESSTA GENERAL Fig 9 2 View of Frame ...
Page 339: ...SECTION 10 HYDRAULICS ...
Page 340: ......
Page 342: ......
Page 363: ...SECTION 10A PUMPS ...
Page 364: ......
Page 366: ......
Page 387: ...SECTION 10B VALVES ...
Page 388: ......
Page 390: ......
Page 412: ......
Page 413: ...SECTION 10C CYLINDERS ...
Page 414: ......
Page 416: ......
Page 449: ...SECTION 10E RESERVOIRS AND FILTERS ...
Page 450: ......
Page 452: ......
Page 459: ...SECTION 12 POWER ...
Page 460: ......
Page 462: ......
Page 478: ......
Page 479: ...SECTION 13 SUPERSTRUCTURE ...
Page 480: ......
Page 482: ......
Page 491: ...SECTION 14 SUSPENSION ...
Page 492: ......
Page 542: ......
Page 543: ...SECTION 15 TRACK OR WHEELS ...
Page 544: ......
Page 546: ......
Page 565: ...SECTION 17 MOUNTED EQUIPMENT ...
Page 566: ......
Page 568: ......