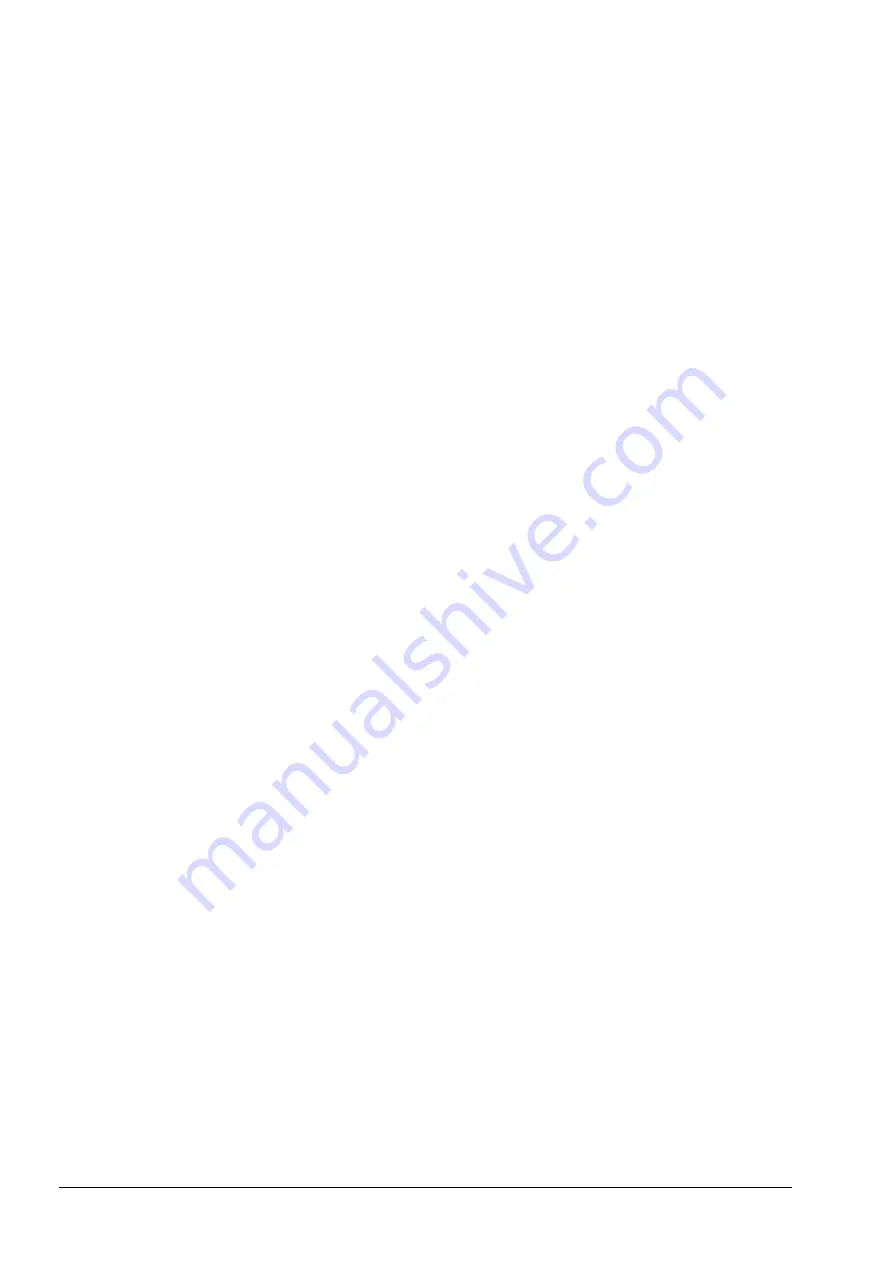
SECTION 10
HYDRAULICS
Page 2
TD-25M EXTRA
DRESSTA
GENERAL
One Spool Control Valve
A one spool control valve is used on machines not equipped with a ripper and it is controlled by
pilot lines from the blade pilot control valve. The valve inlet cover contains an adjustable pilot
operated main pressure relief valve which is used to by pass fluid from the pump back to the
reservoir when the fluid pressure exceeds the relief valve setting. The spool is a spring centered,
four position type with the FLOAT position being magnetically detented at the blade pilot control
valve. Incorporated in the valve section is a spring loaded check valve which assures smooth
operation when the spool is moved from hold to an operating position. An anticavitation valve is
located in the blade lower circuit.
Three Spool Control Valve
A three spool control valve is used on machines equipped with a ripper and it is controlled by pilot
lines from the equipment pilot control valves. The valve inlet cover contains an adjustable pilot
operated main pressure relief valve which is used to by pass fluid from the pump back to the
reservoir when the fluid pressure exceeds the relief valve setting. The blade lift section is a spring
centered, four position type with the FLOAT position being magnetically detented at the blade pilot
control valve. The ripper lift section is used for raising or lower the ripper. The ripper pitch section
is used for pitching the ripper forward or rearward. The two ripper section spools are spring
centered, three position type. Incorporated in all the sections are spring loaded check valves
assure smooth operation when the spool is moved from hold to an operating position. An
anticavitation valves are located in the blade lift section and ripper lift section lower circuits.
Blade Tilt Control Valve or Blade Tilt/Pitch Control Valve
This single spool valve consists of an inlet and outlet portion. The inlet portion spool is a three
position type spring centered. A load check valve is located within the valve. A main relief valve
is located in the port adjacent to the spool cover. An adjustable pilot operated main pressure relief
valve is used to by pass oil from the pump back to reservoir when oil pressure exceeds the relief
valve settings. The tilt (tilt/pitch) valve contains a high pressure carry over tube which directs tilt
(tilt/pitch) pump flow by unloading valve to the main control valve when no demand on the tilt
(tilt/pitch) circuit occurs. The valve is controlled by pilot pressure which is actuated by pilot blade
control valve.
Quick Drop Valve
The quick drop valve is used for accelerated power when lowering of the blade is required.
The valve is front frame mounted and is located in the engine compartment inside of right side of
frame wall. This hydraulically operated valve allows the blade to drop at a faster rate by diverting
return oil through a spool to supplement the blade cylinder input oil from the piston side being used
to lower the blade. The valve only diverts the return oil when the vacuum pressure is created in the
piston side chamber. It occurs during lowering the blade with inadequate oil supply.
Directional Valve
This valve is used so as to control the unloading valve which, in turn, directs the oil from the tilt
pump to the sink at the oil pressure higher than 14 [MPa] in the cylinders lift positions of both the
ripper and the blade.
Unloading Valve
The unloading valve includes: the main spool which connects, or cuts off the tilt pump to the sink,
the spool which connects the tilt pump to the main control valve (one or three spool), and the
sleeve which controls the spools. The purpose of this valve is to direct the oil to the main control
valve when the tilt cylinder does not act and to unload the engine in the movement described
above in Directional Valve description, switching the tilt pump over to the sink.
Summary of Contents for TD-25M EXTRA
Page 1: ...SMTD25MEX07 1E SERVICE MANUAL TD 25M EXTRA SERIAL NUMBERS 75001 AND UP DRESSTA ...
Page 2: ......
Page 4: ......
Page 5: ...SECTION 1 INTRODUCTION ...
Page 6: ......
Page 8: ......
Page 25: ...SECTION 5 STEERING ...
Page 26: ......
Page 27: ...STEERING SECTION 5 DRESSTA TD 25M EXTRA CONTENTS GENERAL 1 DESCRIPTION 1 ...
Page 28: ......
Page 30: ......
Page 31: ...SECTION 6 COOLING SYSTEM ...
Page 32: ......
Page 34: ......
Page 49: ...SECTION 7 DRIVE TRAIN ...
Page 50: ......
Page 52: ......
Page 60: ......
Page 62: ......
Page 83: ...SECTION 7B HYDRAULIC TORQUE CONVERTER ...
Page 84: ......
Page 86: ......
Page 115: ...SECTION 7C TRANSMISSION ...
Page 116: ......
Page 208: ......
Page 209: ...SECTION 7E STEERING DRIVE ...
Page 210: ......
Page 212: ......
Page 251: ...SECTION 7F FINAL DRIVE ...
Page 252: ......
Page 254: ......
Page 272: ......
Page 273: ...SECTION 8 ELECTRICAL ...
Page 274: ......
Page 276: ......
Page 283: ...ELECTRICAL SECTION 8 Page 7 DRESSTA TD 25M EXTRA Fig 8 1 Wiring Diagram earlier version ...
Page 284: ......
Page 285: ......
Page 286: ...SECTION 8 Page 10 ELECTRICAL TD 25M EXTRA DRESSTA Fig 8 1A Wiring Diagram later version ...
Page 331: ...SECTION 9 FRAME ...
Page 332: ......
Page 334: ......
Page 336: ...SECTION 9 FRAME Page 2 TD 25M EXTRA DRESSTA GENERAL Fig 9 2 View of Frame ...
Page 339: ...SECTION 10 HYDRAULICS ...
Page 340: ......
Page 342: ......
Page 363: ...SECTION 10A PUMPS ...
Page 364: ......
Page 366: ......
Page 387: ...SECTION 10B VALVES ...
Page 388: ......
Page 390: ......
Page 412: ......
Page 413: ...SECTION 10C CYLINDERS ...
Page 414: ......
Page 416: ......
Page 449: ...SECTION 10E RESERVOIRS AND FILTERS ...
Page 450: ......
Page 452: ......
Page 459: ...SECTION 12 POWER ...
Page 460: ......
Page 462: ......
Page 478: ......
Page 479: ...SECTION 13 SUPERSTRUCTURE ...
Page 480: ......
Page 482: ......
Page 491: ...SECTION 14 SUSPENSION ...
Page 492: ......
Page 542: ......
Page 543: ...SECTION 15 TRACK OR WHEELS ...
Page 544: ......
Page 546: ......
Page 565: ...SECTION 17 MOUNTED EQUIPMENT ...
Page 566: ......
Page 568: ......