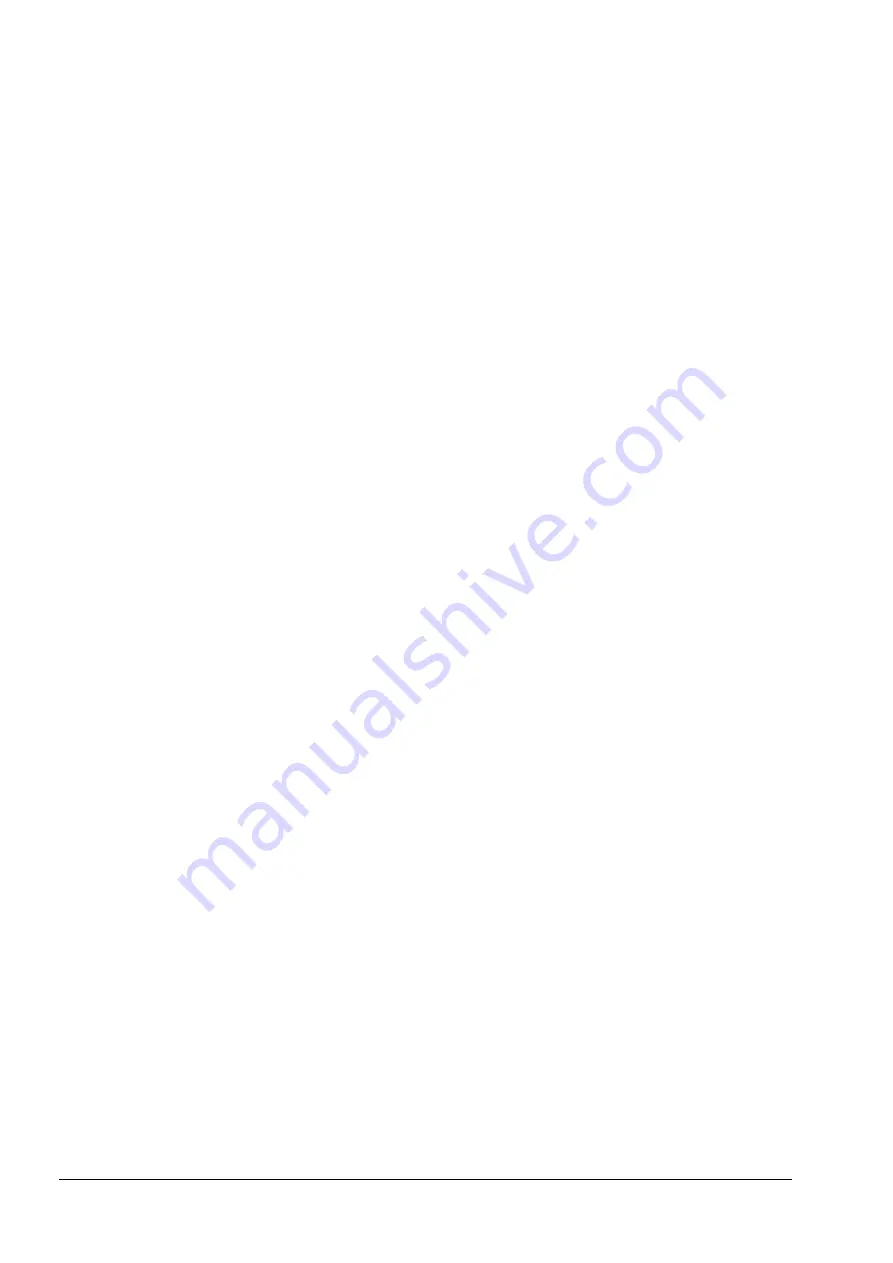
SECTION 8
ELECTRICAL
Page 2
TD-25M EXTRA
DRESSTA
WIRING DIAGRAM
The cranking motor (25) solenoid is actuated by closed contacts of magnetic starting switch (60)
and it draws the cranking motor spool in, engaging the drive gear for the starter and connecting the
battery cable to motor for cranking. Both the magnetic switch and starter solenoid are spring
tensioned to remain in the "disengaged" position. When the starting switch (39) is released, both
units are released, breaking the circuit.
IMPORTANT: When the booster battery is used for engine startup, electric system master switch
must be in the ON position. Alternator can be damaged when the engine startup takes place with
the master switch in the OFF position.
b. Charging Circuit
The charging circuit contains the alternator (24) and the batteries (64). Once the engine is running,
the alternator output is used to supply the power demands as well as recharge the batteries. An
integral regulator is located in alternator itself. The integral regulator senses the entire system draw
and compensates by increasing or decreasing the voltage output.
c. Fan Circuit
Three temperature sensors supply engine electronic control module (ECM) with control signals,
which, in turn, control fan pump solenoid (51).The fan speed will ramp up or down depending on
the systems’ temperature.
In a situation when the drive train oil temperature is below 92 [
°
C], the engine coolant temperature
is below 85 [
°
C] and engine inlet air temperature is below 45 [
°
C] the fan is working at minimum
speed below 400 [RPM]. At the same time the fan pump solenoid (51) is supplied from electronic
control module ECM (8) by the max signal. When the temperature in drive train oil is raising the
resistance of sensor (50) is decreasing and signal from ECM is dropping. The fan starts to work at
higher speed. Engine air inlet temperature sensor and engine cooling temperature sensor (refer to
Electrical Diagram at Troubleshooting and Repair Manual QSK Engine Fuel System) are
connected to ECM (8) too. When air inlet temperature or cooling temperature rises the fan starts to
work at higher speed too. The fan will work at max speed ~1560 RPM when drive train oil
temperature reach 115 [
°
C] or engine inlet air temperature reach 61 [
°
C] or engine cooling
temperature reach 95 [
°
C]. Authorized Cummins Engine Service is provided with a program for
checking the signals sourced by the following sensors: both the engine intake air and coolant
temperatures as well as the fan pump coil power supply signal.
d. Drive Train Control Circuit
With the engine started, the machine remains stationary as drive train lock is actuated. The drive
train lock lever shifted upwards (unlocked) will cause drive train system lock switch (101) to
activate, and, as a result, the drive train system lock solenoid valve will energize. Consequently,
pressurized oil will enter the drive train control valve. The following features are available with the
drive train control lever (9) which incorporates both the (UP, DN) buttons and (LH, RH) switches.
1. Gears upshift and downshift. To do it, press the UP or DN button. Once the UP button has been
pressed, the gear will be upshifted that 2
nd
or 3
rd
gear will be engaged. The DN button pressed
will downshift the gears to a lower gear in a sequence. The first gear is a default gear after the
engine start-up. The solenoid valves (98 and 99) will be deenergized at that point. The second
gear will be engaged when the solenoid valve (99) is reenergized; while the third gear requires
the solenoid valve (98) to get reenergized. The drive train electronic controller (10) is in charge
of solenoid valves being reenergized or deenergized. The time duration the control button is
depressed has no bearing on gear shifting.
Summary of Contents for TD-25M EXTRA
Page 1: ...SMTD25MEX07 1E SERVICE MANUAL TD 25M EXTRA SERIAL NUMBERS 75001 AND UP DRESSTA ...
Page 2: ......
Page 4: ......
Page 5: ...SECTION 1 INTRODUCTION ...
Page 6: ......
Page 8: ......
Page 25: ...SECTION 5 STEERING ...
Page 26: ......
Page 27: ...STEERING SECTION 5 DRESSTA TD 25M EXTRA CONTENTS GENERAL 1 DESCRIPTION 1 ...
Page 28: ......
Page 30: ......
Page 31: ...SECTION 6 COOLING SYSTEM ...
Page 32: ......
Page 34: ......
Page 49: ...SECTION 7 DRIVE TRAIN ...
Page 50: ......
Page 52: ......
Page 60: ......
Page 62: ......
Page 83: ...SECTION 7B HYDRAULIC TORQUE CONVERTER ...
Page 84: ......
Page 86: ......
Page 115: ...SECTION 7C TRANSMISSION ...
Page 116: ......
Page 208: ......
Page 209: ...SECTION 7E STEERING DRIVE ...
Page 210: ......
Page 212: ......
Page 251: ...SECTION 7F FINAL DRIVE ...
Page 252: ......
Page 254: ......
Page 272: ......
Page 273: ...SECTION 8 ELECTRICAL ...
Page 274: ......
Page 276: ......
Page 283: ...ELECTRICAL SECTION 8 Page 7 DRESSTA TD 25M EXTRA Fig 8 1 Wiring Diagram earlier version ...
Page 284: ......
Page 285: ......
Page 286: ...SECTION 8 Page 10 ELECTRICAL TD 25M EXTRA DRESSTA Fig 8 1A Wiring Diagram later version ...
Page 331: ...SECTION 9 FRAME ...
Page 332: ......
Page 334: ......
Page 336: ...SECTION 9 FRAME Page 2 TD 25M EXTRA DRESSTA GENERAL Fig 9 2 View of Frame ...
Page 339: ...SECTION 10 HYDRAULICS ...
Page 340: ......
Page 342: ......
Page 363: ...SECTION 10A PUMPS ...
Page 364: ......
Page 366: ......
Page 387: ...SECTION 10B VALVES ...
Page 388: ......
Page 390: ......
Page 412: ......
Page 413: ...SECTION 10C CYLINDERS ...
Page 414: ......
Page 416: ......
Page 449: ...SECTION 10E RESERVOIRS AND FILTERS ...
Page 450: ......
Page 452: ......
Page 459: ...SECTION 12 POWER ...
Page 460: ......
Page 462: ......
Page 478: ......
Page 479: ...SECTION 13 SUPERSTRUCTURE ...
Page 480: ......
Page 482: ......
Page 491: ...SECTION 14 SUSPENSION ...
Page 492: ......
Page 542: ......
Page 543: ...SECTION 15 TRACK OR WHEELS ...
Page 544: ......
Page 546: ......
Page 565: ...SECTION 17 MOUNTED EQUIPMENT ...
Page 566: ......
Page 568: ......