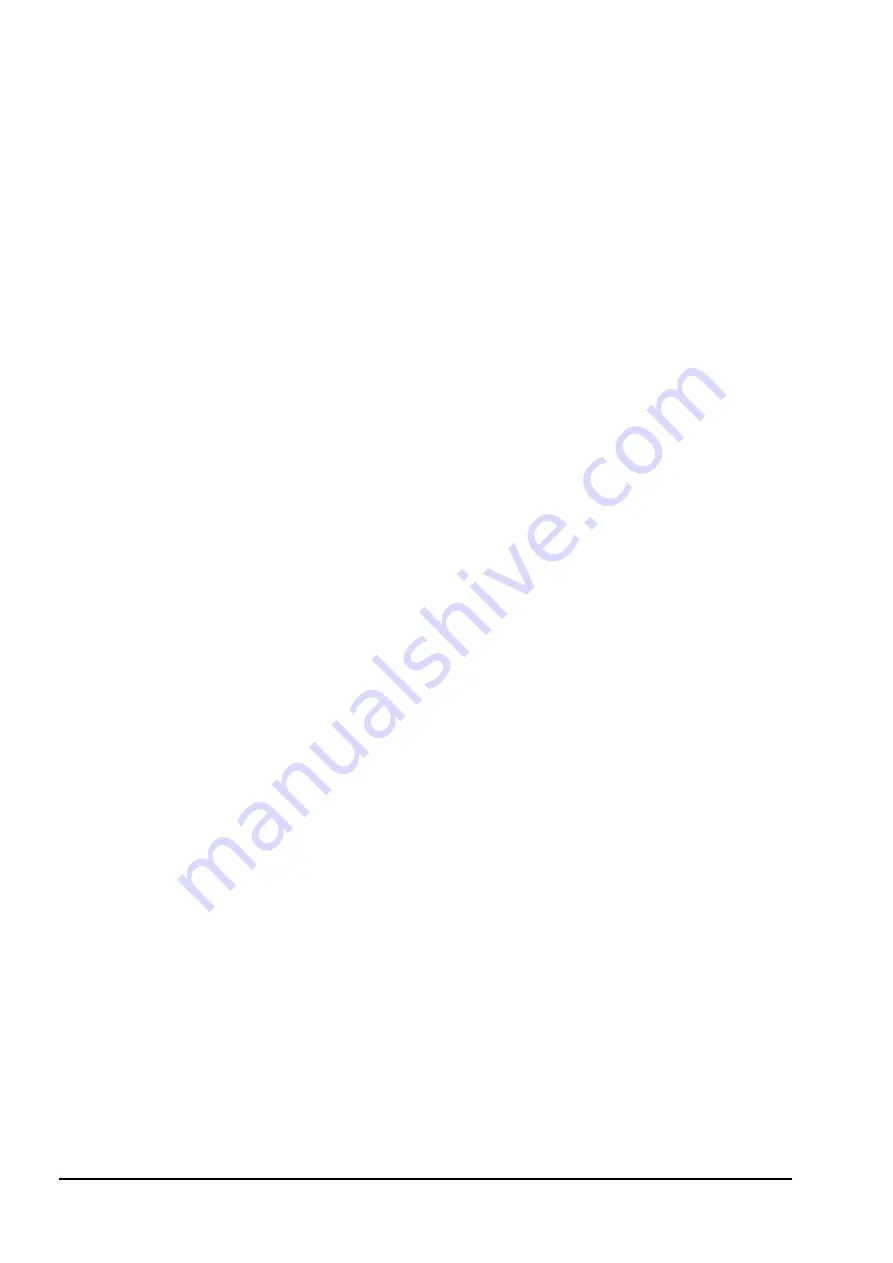
SECTION 10A
PUMPS
Page 2
TD-25M EXTRA
DRESSTA
EQUIPMENT PUMP
2. DESCRIPTION AND OPERATION (Refer to Fig. 10A.7)
The equipment pump rotary vane type consists principally of an inlet housing, three outlet bodies,
a drive shaft and three pumping cartridges. The single inlet port feeds all three pumping cartridges.
Front and Center Pumping Cartridges
The principle components of a cartridge are an elliptical rotor ring, a slotted rotor splined to the
drive shaft, an inlet and outlet support plate fitted with four special seal pack subassemblies, two
flex side plates and ten vanes and inserts fitted to the rotor slots. Fluid enters the cartridge through
the inlet port and is discharged through the outlet of flex side plate and support plate to the outlet
ports.
The rotor is driven within the rotor ring by the pump driveshaft, which is coupled to the torque
converter accessory drive gear. As the rotor turns, centrifugal force on the vanes, aided by under
vane pressure fed from the outlet port, causes the vanes to follow the elliptical inner surface of the
rotor ring. Radial movement of the vanes and turning of the rotor causes the chamber volume
between the vanes to increase as the vanes pass the inlet sections of the rotor ring. This results in
a low pressure condition which allows atmospheric pressure to force fluid into the chambers. An
additional inlet fluid exists through a drilled hole in the rotor ring. This hole connects the inlet port
directly to the inlet areas of the rotor ring and provides an additional flow path for fluid to get into
the cartridge.
Fluid is trapped between the vanes and carried past a sealing land to the outlet section of the rotor
ring. As the outlet section is approached, the chamber volume decreases and fluid is forced out
into the system. System pressure is fed under the vanes, assuring their sealing contact against the
rotor ring during normal operation. In the intra-vane cartridge, full system pressure is continuously
applied only to the area between the vane and insert. This area is small and thrust is
correspondingly light. During vane travel through pressure areas, full system pressure is applied
against the bottom area of the outer vane. The valving of pressure to and from the bottom area of
the vane is through holes drilled in the rotor. This selective application of pressure maintains the
vane in substantially constant radial hydraulic balance in all positions. Vane tip wear is
compensated automatically.
As the vane wears, pressure moves the vane father out in the rotor slot holding the vane
tip against the rotor ring. The pump ring is shaped so that two pumping chambers are formed
180 [
o
] apart. Thus, opposing hydraulic forces which develop side loads on the shaft cancel out
to form a hydraulic balance.
The flex side plates for both inlet and outlet are symmetrical. Pressure is fed behind each side
plate into two kidney shaped cavities, which are sealed by special seal pack subassemblies.
The two flex side plates and their associated kidney shaped cavities function in the following
manner. As pressure also builds up in the outlet, pressure also builds up in the cavities. The
pressure in the cavities hold the flex side plates in hydraulic balance against the rotor and provide
optimum running clearance for minimum internal leakage and minimum friction. The flex side
plates also provide passages for feeding under vane pressure to the space between the vane and
insert. The bronze faces of the flex side plates ride next to the rotor and provide excellent wear and
cold start characteristics. The inlet and outlet support plates hold the flex side plates in position and
contain passages which allow fluid pass from the inlet to the pumping cartridge and from the
cartridge to the outlet port.
Summary of Contents for TD-25M EXTRA
Page 1: ...SMTD25MEX07 1E SERVICE MANUAL TD 25M EXTRA SERIAL NUMBERS 75001 AND UP DRESSTA ...
Page 2: ......
Page 4: ......
Page 5: ...SECTION 1 INTRODUCTION ...
Page 6: ......
Page 8: ......
Page 25: ...SECTION 5 STEERING ...
Page 26: ......
Page 27: ...STEERING SECTION 5 DRESSTA TD 25M EXTRA CONTENTS GENERAL 1 DESCRIPTION 1 ...
Page 28: ......
Page 30: ......
Page 31: ...SECTION 6 COOLING SYSTEM ...
Page 32: ......
Page 34: ......
Page 49: ...SECTION 7 DRIVE TRAIN ...
Page 50: ......
Page 52: ......
Page 60: ......
Page 62: ......
Page 83: ...SECTION 7B HYDRAULIC TORQUE CONVERTER ...
Page 84: ......
Page 86: ......
Page 115: ...SECTION 7C TRANSMISSION ...
Page 116: ......
Page 208: ......
Page 209: ...SECTION 7E STEERING DRIVE ...
Page 210: ......
Page 212: ......
Page 251: ...SECTION 7F FINAL DRIVE ...
Page 252: ......
Page 254: ......
Page 272: ......
Page 273: ...SECTION 8 ELECTRICAL ...
Page 274: ......
Page 276: ......
Page 283: ...ELECTRICAL SECTION 8 Page 7 DRESSTA TD 25M EXTRA Fig 8 1 Wiring Diagram earlier version ...
Page 284: ......
Page 285: ......
Page 286: ...SECTION 8 Page 10 ELECTRICAL TD 25M EXTRA DRESSTA Fig 8 1A Wiring Diagram later version ...
Page 331: ...SECTION 9 FRAME ...
Page 332: ......
Page 334: ......
Page 336: ...SECTION 9 FRAME Page 2 TD 25M EXTRA DRESSTA GENERAL Fig 9 2 View of Frame ...
Page 339: ...SECTION 10 HYDRAULICS ...
Page 340: ......
Page 342: ......
Page 363: ...SECTION 10A PUMPS ...
Page 364: ......
Page 366: ......
Page 387: ...SECTION 10B VALVES ...
Page 388: ......
Page 390: ......
Page 412: ......
Page 413: ...SECTION 10C CYLINDERS ...
Page 414: ......
Page 416: ......
Page 449: ...SECTION 10E RESERVOIRS AND FILTERS ...
Page 450: ......
Page 452: ......
Page 459: ...SECTION 12 POWER ...
Page 460: ......
Page 462: ......
Page 478: ......
Page 479: ...SECTION 13 SUPERSTRUCTURE ...
Page 480: ......
Page 482: ......
Page 491: ...SECTION 14 SUSPENSION ...
Page 492: ......
Page 542: ......
Page 543: ...SECTION 15 TRACK OR WHEELS ...
Page 544: ......
Page 546: ......
Page 565: ...SECTION 17 MOUNTED EQUIPMENT ...
Page 566: ......
Page 568: ......