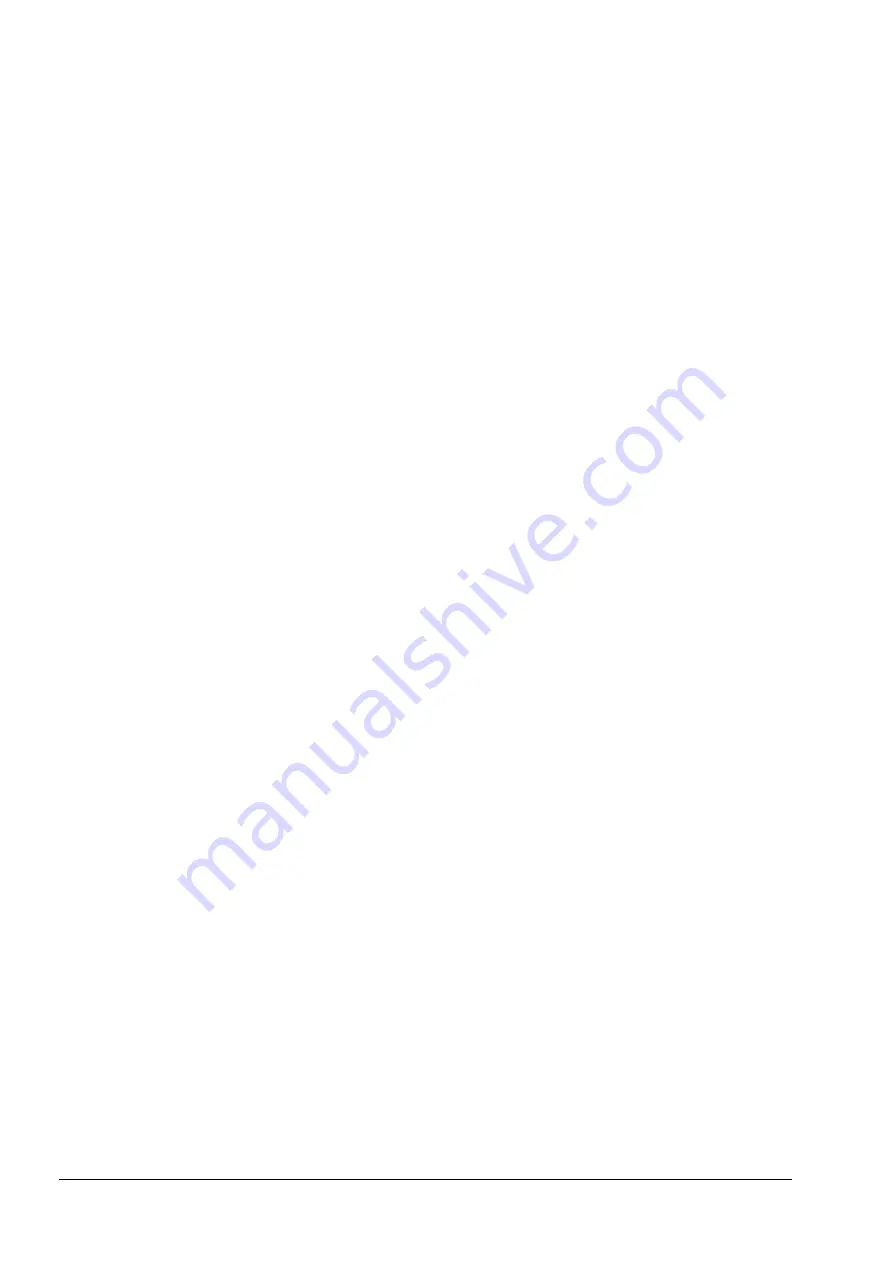
SECTION 7
DRIVE TRAIN
Page 2
TD-25M EXTRA
DRESSTA
GENERAL
Power from the engine is transmitted through a flywheel drive ring to the torque converter (2). Drive
shaft (3) couples the output flange of the torque converter with input yoke (4) of transmission (5).
The converter delivers torque according to the variation in load on the oil used as the medium, and
transmits the power to the transmission (5). When the transmission is engaged, power is
transmitted from the output shaft of the transmission to the pinion shaft of steering drive (8), and by
steering drive clutches to the steering drive output shaft (10), then through final drives (13) and
sprockets (14 and 15) to the tracks.
3. DRIVE TRAIN MAIN COMPONENTS
The torque converter (2, Fig. 7.1)
contains a single stage, single phase, three element converter
assembly and a drive gear to drive the drive train charge and scavenge pump, the equipment
pump and the fan drive pump. The torque converter main function is to multiply engine torque.
The transmission (5)
is designed to provide high speed shifting by use of hydraulically actuated
clutch packs. It has three forward and three reverse speeds. Gears are mounted on four shafts:
directional (input) shaft, range (output) shaft, countershaft and reverse idler shaft.
The steering drive (8)
is a unit constructed into a housing similar to a transmission. This design
affords ease of assembly and service. The machine is equipped with the two speed steering drive.
The two speed steering drive contains one low range clutch pack, one high range clutch pack, one
brake clutch pack and a planetary on each side of the machine. The low and high range clutch
packs are hydraulically applied and spring released whereas the brake clutch packs are spring
applied and hydraulically released. An inner planetary provides the reduction in speed for the low
range. If a hydraulic failure occurs or the engine is stopped, the steering drive will automatically
apply the brakes.
The final drive (13)
consist of a set of spur gears and a planetary on each side at the rear of the
machine. Power is transmitted from the steering drive to each of the final drives. Double reduction
in the final drive is accomplished by a pinion to bullgear arrangement for the first reduction and
a planetary set for the final reduction.
OPERATION
4. DRIVE TRAIN SYSTEM VALVES
Drive Train Control Valve (12, Fig.’s 7.2 and 7.3)
The drive train control valve is a manually controlled direction, range and steering control valve.
The valve is used to direct main oil pressure to the transmission range selector valve for
transmission control and to the steering control valve for range and steering control. A detent
mechanism holds the control lever in the desired transmission direction.
Main pressure from the charge pump through hydraulic damper, pressure filter and drive train
neutral lock solenoid valve enters the drive train control valve at the “M” port and is distributed to
the direction and steering spools. When the control lever is in the centered “neutral” position, oil is
active at the selected steering ports but is blocked at the direction spools.
Summary of Contents for TD-25M EXTRA
Page 1: ...SMTD25MEX07 1E SERVICE MANUAL TD 25M EXTRA SERIAL NUMBERS 75001 AND UP DRESSTA ...
Page 2: ......
Page 4: ......
Page 5: ...SECTION 1 INTRODUCTION ...
Page 6: ......
Page 8: ......
Page 25: ...SECTION 5 STEERING ...
Page 26: ......
Page 27: ...STEERING SECTION 5 DRESSTA TD 25M EXTRA CONTENTS GENERAL 1 DESCRIPTION 1 ...
Page 28: ......
Page 30: ......
Page 31: ...SECTION 6 COOLING SYSTEM ...
Page 32: ......
Page 34: ......
Page 49: ...SECTION 7 DRIVE TRAIN ...
Page 50: ......
Page 52: ......
Page 60: ......
Page 62: ......
Page 83: ...SECTION 7B HYDRAULIC TORQUE CONVERTER ...
Page 84: ......
Page 86: ......
Page 115: ...SECTION 7C TRANSMISSION ...
Page 116: ......
Page 208: ......
Page 209: ...SECTION 7E STEERING DRIVE ...
Page 210: ......
Page 212: ......
Page 251: ...SECTION 7F FINAL DRIVE ...
Page 252: ......
Page 254: ......
Page 272: ......
Page 273: ...SECTION 8 ELECTRICAL ...
Page 274: ......
Page 276: ......
Page 283: ...ELECTRICAL SECTION 8 Page 7 DRESSTA TD 25M EXTRA Fig 8 1 Wiring Diagram earlier version ...
Page 284: ......
Page 285: ......
Page 286: ...SECTION 8 Page 10 ELECTRICAL TD 25M EXTRA DRESSTA Fig 8 1A Wiring Diagram later version ...
Page 331: ...SECTION 9 FRAME ...
Page 332: ......
Page 334: ......
Page 336: ...SECTION 9 FRAME Page 2 TD 25M EXTRA DRESSTA GENERAL Fig 9 2 View of Frame ...
Page 339: ...SECTION 10 HYDRAULICS ...
Page 340: ......
Page 342: ......
Page 363: ...SECTION 10A PUMPS ...
Page 364: ......
Page 366: ......
Page 387: ...SECTION 10B VALVES ...
Page 388: ......
Page 390: ......
Page 412: ......
Page 413: ...SECTION 10C CYLINDERS ...
Page 414: ......
Page 416: ......
Page 449: ...SECTION 10E RESERVOIRS AND FILTERS ...
Page 450: ......
Page 452: ......
Page 459: ...SECTION 12 POWER ...
Page 460: ......
Page 462: ......
Page 478: ......
Page 479: ...SECTION 13 SUPERSTRUCTURE ...
Page 480: ......
Page 482: ......
Page 491: ...SECTION 14 SUSPENSION ...
Page 492: ......
Page 542: ......
Page 543: ...SECTION 15 TRACK OR WHEELS ...
Page 544: ......
Page 546: ......
Page 565: ...SECTION 17 MOUNTED EQUIPMENT ...
Page 566: ......
Page 568: ......