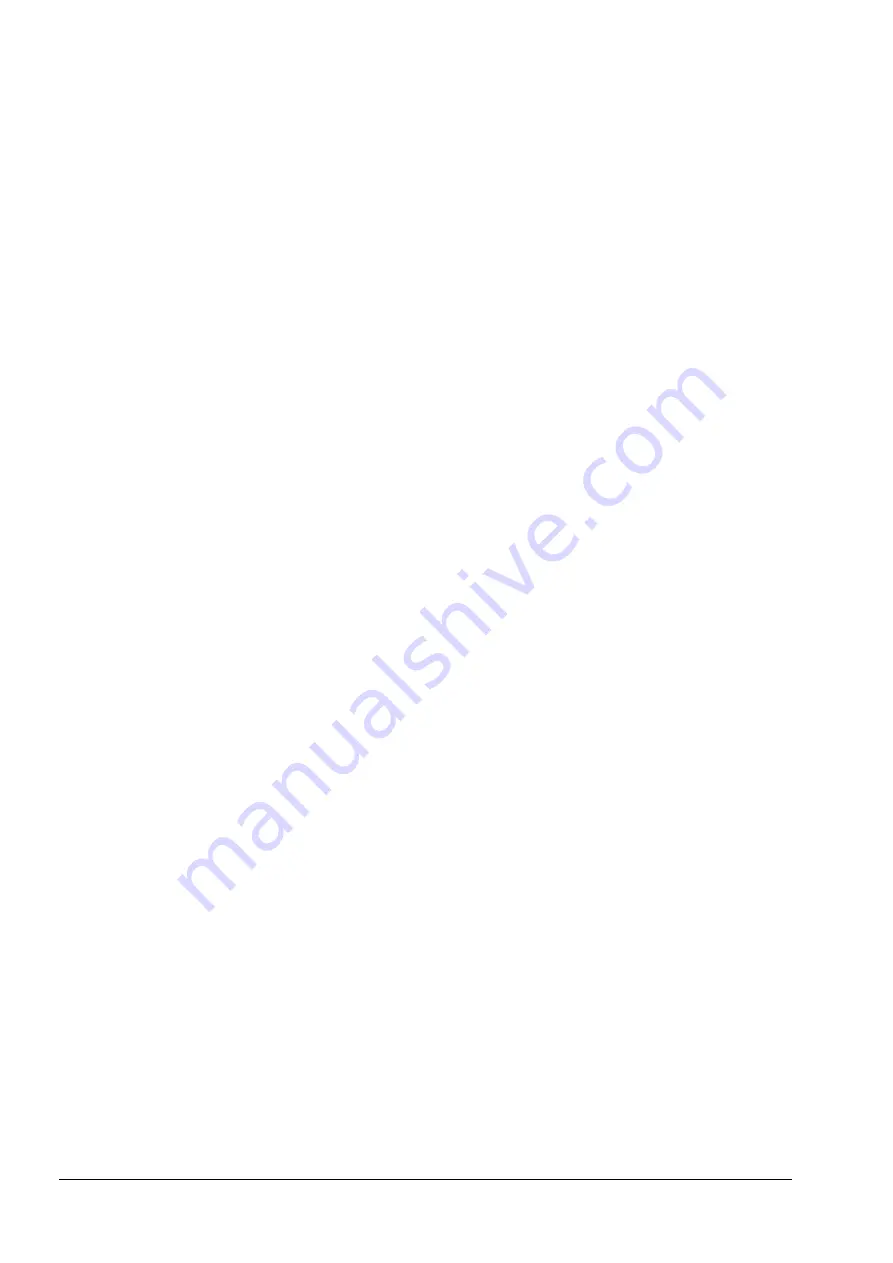
SECTION 8
ELECTRICAL
Page 20
TD-25M EXTRA
DRESSTA
WIRING DIAGRAM
There are two extra magnetic switches beside the
WO
switch mentioned above in the auto
downshift system.
•
engine RPM (CS);
•
torque converter output RPM (CIW)
Based on the pulse train coming from these sensors the microprocessor controller will compute the
torque converter kinematics ratio. If the controller is fed with a pulse train from the
CS
sensor, the
red diode
L23
is to come on. Similarly, if the pulse train from
CIW
sensor is fed, then
L22
will come
on.
The controller will operate as described below depending on the torque converter kinematics ratio.
•
if the ratio ranges from 0.75 to 1 – a manual gear change is possible with
Up
and
Dn
buttons as described above;
•
if the ratio ranges from 0.40 to 0.75 - a manual downshift is possible with
Dn
button as
described above; however the controller will not allow for up shift with
Up
button;
•
if the ratio is less than 0.40, and the machine rides in say, the third gear, the controller will
automatically downshift and after about 5 seconds will recheck the ratio. If the ratio is still
below 0.40 (the machine is riding in the second gear), another downshift will take place,
diodes will come on as per algorithm described for a manual downshift. Manual up shift will
be deactivated unless the ratio is over 0.75, regardless of the gear engaged (excluding third
gear).
It goes without saying that with the auto downshift mode disabled, the manual up shift is
immediately activated, regardless of the ratio.
c. Presetting mode
Presetting mode is provided with the highest priority in a gear change system. Generally,
presetting allows the machine motion at well predefined gears; gear can be defined regardless the
machine motion forward or reverse. The controller ignores
Up
and
Dn
buttons in this gear change
mode. The auto downshift mode is not operational either, regardless the
WO
switch position.
Machines are provided with two presetting modes which can be chosen with a gear mode change
switch (presetting)
WB
that can be found at the instrument panel.
1/2 Presetting mode
In this mode the
WB
switch is set to
1/2
position which in turn, will cause a yellow diode
L29
to
come on. The machine will move forward in the first gear (green diode
L18
will come on,
L17
and
L16
will come off, while solenoid valves
EZ2
and
EZ3
will get deactivated), and in the second gear
reverse (diode
L17
will come on,
L18
and
L16
will come off,
EZ2
activated,
EZ3
deactivated). The
display will show the active gear, while the motion direction will be signaled with a suitable diode.
There are two pressure switches in the drive control system that will provide information to the
microprocessor controller on the machine motion direction.
WF
– which will shot the controller to
the machine ground in case the machine would move forward; its operation will cause the yellow
diode
L8
to come on, as well as
WR
- which will shot the controller to the machine ground in case
the machine would move reverse; its operation will cause the yellow diode
L9
to come on. When
the machine is stopped both sensors will not provide any signal to the controller and diodes
L8
and
L9
will be off. Fig. 8.1D. provides a control system schematic in this operation mode.
Summary of Contents for TD-25M EXTRA
Page 1: ...SMTD25MEX07 1E SERVICE MANUAL TD 25M EXTRA SERIAL NUMBERS 75001 AND UP DRESSTA ...
Page 2: ......
Page 4: ......
Page 5: ...SECTION 1 INTRODUCTION ...
Page 6: ......
Page 8: ......
Page 25: ...SECTION 5 STEERING ...
Page 26: ......
Page 27: ...STEERING SECTION 5 DRESSTA TD 25M EXTRA CONTENTS GENERAL 1 DESCRIPTION 1 ...
Page 28: ......
Page 30: ......
Page 31: ...SECTION 6 COOLING SYSTEM ...
Page 32: ......
Page 34: ......
Page 49: ...SECTION 7 DRIVE TRAIN ...
Page 50: ......
Page 52: ......
Page 60: ......
Page 62: ......
Page 83: ...SECTION 7B HYDRAULIC TORQUE CONVERTER ...
Page 84: ......
Page 86: ......
Page 115: ...SECTION 7C TRANSMISSION ...
Page 116: ......
Page 208: ......
Page 209: ...SECTION 7E STEERING DRIVE ...
Page 210: ......
Page 212: ......
Page 251: ...SECTION 7F FINAL DRIVE ...
Page 252: ......
Page 254: ......
Page 272: ......
Page 273: ...SECTION 8 ELECTRICAL ...
Page 274: ......
Page 276: ......
Page 283: ...ELECTRICAL SECTION 8 Page 7 DRESSTA TD 25M EXTRA Fig 8 1 Wiring Diagram earlier version ...
Page 284: ......
Page 285: ......
Page 286: ...SECTION 8 Page 10 ELECTRICAL TD 25M EXTRA DRESSTA Fig 8 1A Wiring Diagram later version ...
Page 331: ...SECTION 9 FRAME ...
Page 332: ......
Page 334: ......
Page 336: ...SECTION 9 FRAME Page 2 TD 25M EXTRA DRESSTA GENERAL Fig 9 2 View of Frame ...
Page 339: ...SECTION 10 HYDRAULICS ...
Page 340: ......
Page 342: ......
Page 363: ...SECTION 10A PUMPS ...
Page 364: ......
Page 366: ......
Page 387: ...SECTION 10B VALVES ...
Page 388: ......
Page 390: ......
Page 412: ......
Page 413: ...SECTION 10C CYLINDERS ...
Page 414: ......
Page 416: ......
Page 449: ...SECTION 10E RESERVOIRS AND FILTERS ...
Page 450: ......
Page 452: ......
Page 459: ...SECTION 12 POWER ...
Page 460: ......
Page 462: ......
Page 478: ......
Page 479: ...SECTION 13 SUPERSTRUCTURE ...
Page 480: ......
Page 482: ......
Page 491: ...SECTION 14 SUSPENSION ...
Page 492: ......
Page 542: ......
Page 543: ...SECTION 15 TRACK OR WHEELS ...
Page 544: ......
Page 546: ......
Page 565: ...SECTION 17 MOUNTED EQUIPMENT ...
Page 566: ......
Page 568: ......